At Metinvest Group's CGOK beneficiation plant, a mill underwent repairs as part of routine preventive maintenance. This will help sustain high equipment efficiency and ensure the quality of the final products.
As part of routine preventive maintenance, the specialists inspected, maintained and replaced worn components of MShTs 3.6x5.0 mill.
"Mills play a crucial role in the concentrate production process. They grind the ore to the necessary size, which is essential for the following beneficiation stages," explains Oleg KLYMOVYCH, Deputy Head of Ore Beneficiation Plant, CGOK. "MShTs 3.6x5.0 mill is our workhorse, with a planned capacity of 85 tons of crushed ore per hour. It's used in the initial stage of ore crushing, primarily sourced from the Artemovskyi open pit mine, to produce high-grade concentrate with an iron content exceeding 69%."
Quality and timely repairs performed by the plant specialists are essential for maintaining a stable and efficient production process.
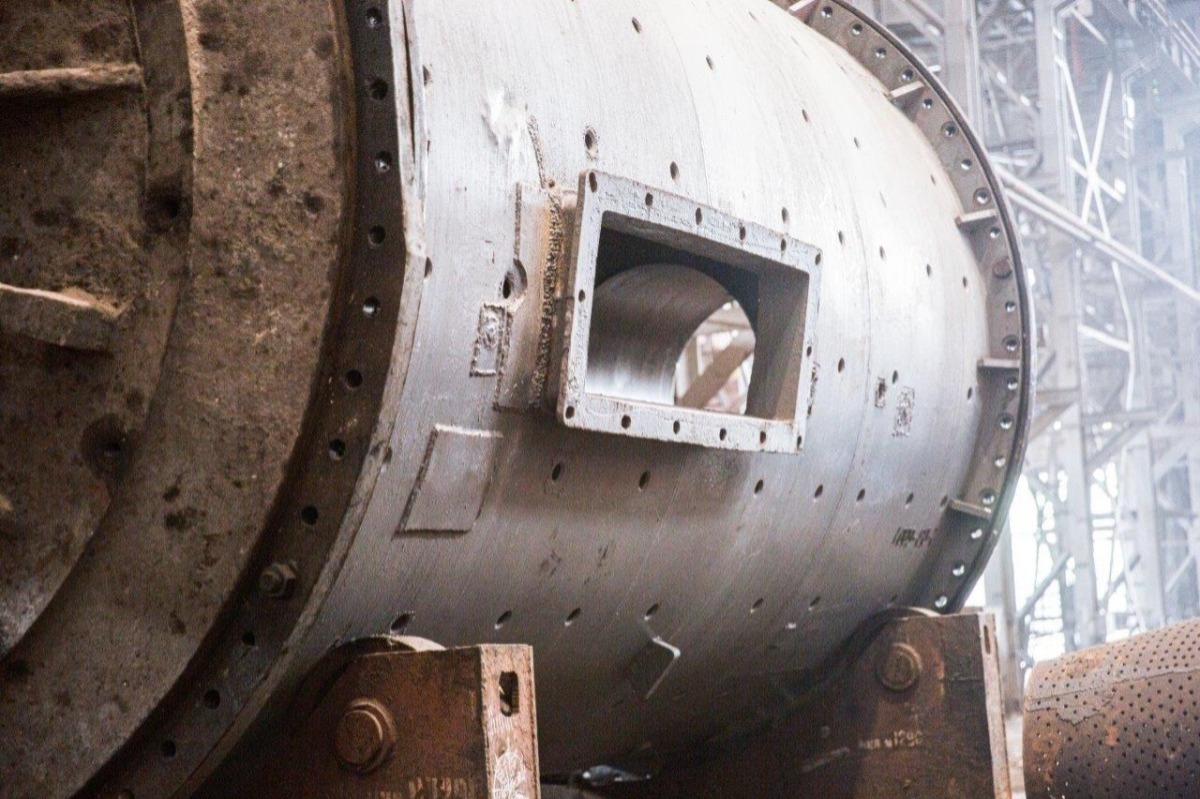
"The specialists completed the scheduled tasks within the designated 48-hour timeframe. To keep the equipment running smoothly, they replaced the drive, gear shaft, bearings and liners. Additionally, repair specialists found and fixed existing problems with the equipment by thoroughly inspecting the rubber armor," said Eduard KOBITSKY, head of the beneficiation plant section.
The beneficiation technicians assure: regularly performing these maintenance tasks helps spot and fix potential problem early, preventing serious problems and avoiding production shutdowns. Moreover, routine preventive maintenance extends the equipment's lifespan, ultimately lowering long-term replacement and repair costs. For instance, promptly replacing the mill's rubber armor or inspecting the gear shaft can prevent costly breakdowns. And, last but not least, performing routine preventive maintenance boosts worker safety by reducing likelihood of emergencies.