Kamet-Steel's leading rolling mill has reached the first decade of its history. In the anniversary year, the rolling mill team continues its steady path of implementing the production programme, expanding the product mix and improving the efficiency of the shop.
The commissioning of the 400/200 mill was, without exaggeration, a step into the rolling technologies of the 21st century. It was in April 2014 that the mill carried out the first trial rolling of a round billet of 40 mm in diameter. From that moment on, as part of the commissioning process, rolled products were systematically mastered together with European specialists who supervised the equipment adjustment. In May, Line 200 produced the first batch of round wire rod in coils.
At the same time, installation and commissioning work continued at Line 400. A month later, a trial rolling of angle 50 was carried out on the section line, and the development of reinforcing bars on the slitting line began. All this time, the key attention was paid to the training of process personnel, with theoretical training in classrooms and practical training directly at the mill, which was the only one in Ukraine at the time.
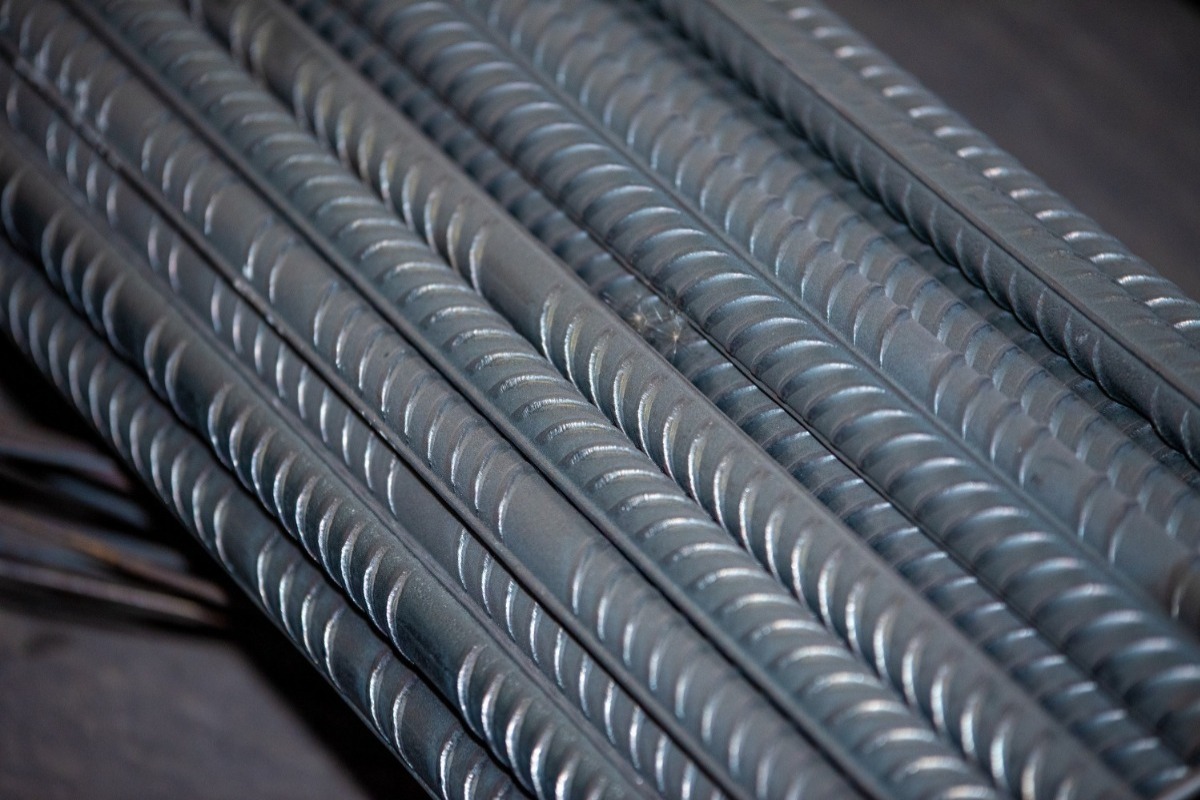
In the first year of operation, the rolling team focused its efforts on maximising the mill's product mix capabilities: four, five or even six new section sizes were rolled out every month.
Further modernisation steps were aimed primarily at achieving a stable section size: to improve the stability of geometric parameters, partial changes were made to calibration procedure, and process instructions were adapted to the operating conditions of the mill. Over time, the mill also unified the replaceable elements of equipment of the stands and the mill's flow line, which helped to reduce losses due to equipment downtime during the transition from one section size to another.
Over the 10 years of operation, Kamet-Steel's Mill 400/200 has mastered 119 section sizes of rolled products, produced and shipped almost 5 million tonnes of products, including over 2.6 million tonnes of wire rod and over 2.2 million tonnes of long products and rebars.
Today, the long products department of the rolling mill is characterised by a stable operation, systematic expansion of the product mix and increased production efficiency even in difficult wartime conditions. The most popular products in high demand both in Ukraine and abroad include wire rod with a diameter of 5.5 to 12 mm, rounds with a diameter of 25, 30 and 40 mm, angles, channels, and rebar with a diameter of 8 to 36 mm. Since the beginning of the year, the workers of the rolling shop have shipped nearly 160,000 tonnes of its products to domestic and foreign customers.
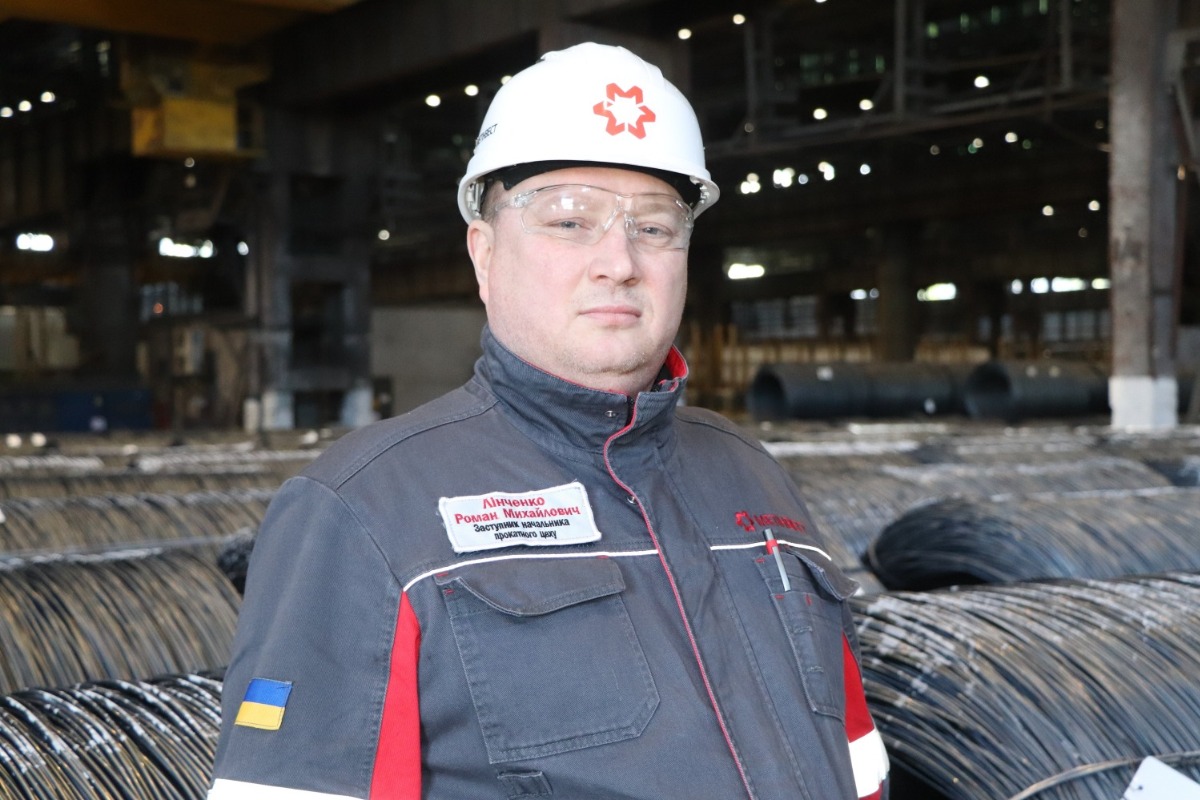
Roman Linchenko
"The most important goals of our team are to fulfil the production programme and improve operational efficiency, primarily by reducing energy consumption. Among the most urgent measures are the adjustments to the billet heating schedules made during the overhaul of the heating furnace at the end of 2023. This allows us to increase hourly productivity of the slitting line while reducing natural gas consumption that results in a reduction in specific gas consumption per tonne of product.
We are also actively working on mastering the production of A800 reinforcing bars with improved mechanical properties due to heat treatment. Thanks to the technological capabilities of the mill, we have certain prospects in this area to produce more marginal products without increasing the cost of continuously cast billets. Our specialists have already completed a trial rolling of a batch of rebar of the most popular diameters, selected the optimal heat hardening mode and received the first positive laboratory results," says Roman LINCHENKO, Deputy Head of the Rolling Shop for Mill 400/200.
The rolling team is an efficient team, each member of which, whether a rollerman, mill operator, crane operator or repairman, is a highly skilled professional with universal knowledge and skills who skilfully performs important tasks on each production line of the modern 400/200 mill, has a perfect knowledge of the specifics of production and does not stop learning new knowledge and competencies through the training programmes available at Kamet-Steel.
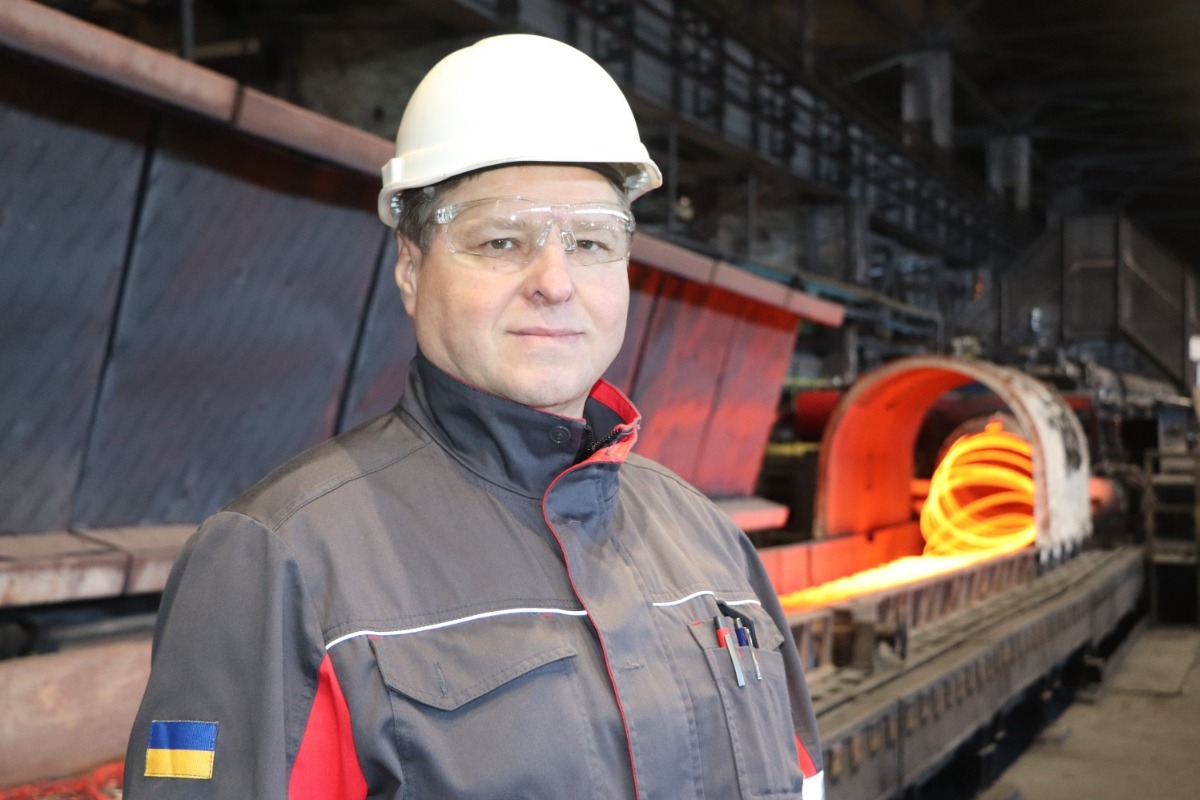
Oleksandr Oliynyk
"Today, the 400/200 mill has become the leading rolling mill of the plant with an average monthly output of 52,000 tonnes of rolled steel, which generates profit for the plant and allows it to maintain a strong position in the domestic and global markets. Over the past ten years, we have come a long way of development, improvement, modernisation, productivity increase and cost reduction for rolled steel production. Everyone working at this high-speed and high-tech mill has learnt to withstand the challenges of the times thanks to their professionalism, ability to work in a team and a conscious desire to keep on acquiring new knowledge, improving production processes, and developing new products.
The rolling shop team is united in this, because only by working together, despite the technical, financial and personnel difficulties of the wartime, we can solve important tasks at each section, including the long product section. That is why I am pleased to congratulate the entire team of rolling shop workers on the first anniversary of Mill 400/200.
Our efficient hero of the day has a lot of potential, and it has the potential to be reconstructed, which could result in two independent high-performance rolling mills - 400 and 200 - capable of producing up to one million tonnes of finished rolled steel per year. And I sincerely wish all of us and our plant the fastest possible peaceful development, which will allow us to implement our wildest hopes and plans," said Oleksandr OLIINYK, Chief Rolling Engineer at Kamet-Steel.