Mastering of CC billet casting using stopper mechanisms at Billet Caster 1 is reaching a new level. In 2024, BOF Shop of Kamet-Steel expanded the range of high-quality merchant billet and increased the volume of CC billet production using this technology. This year, steelmakers are facing new challenges to improve the efficiency of submerged entry nozzle casting.
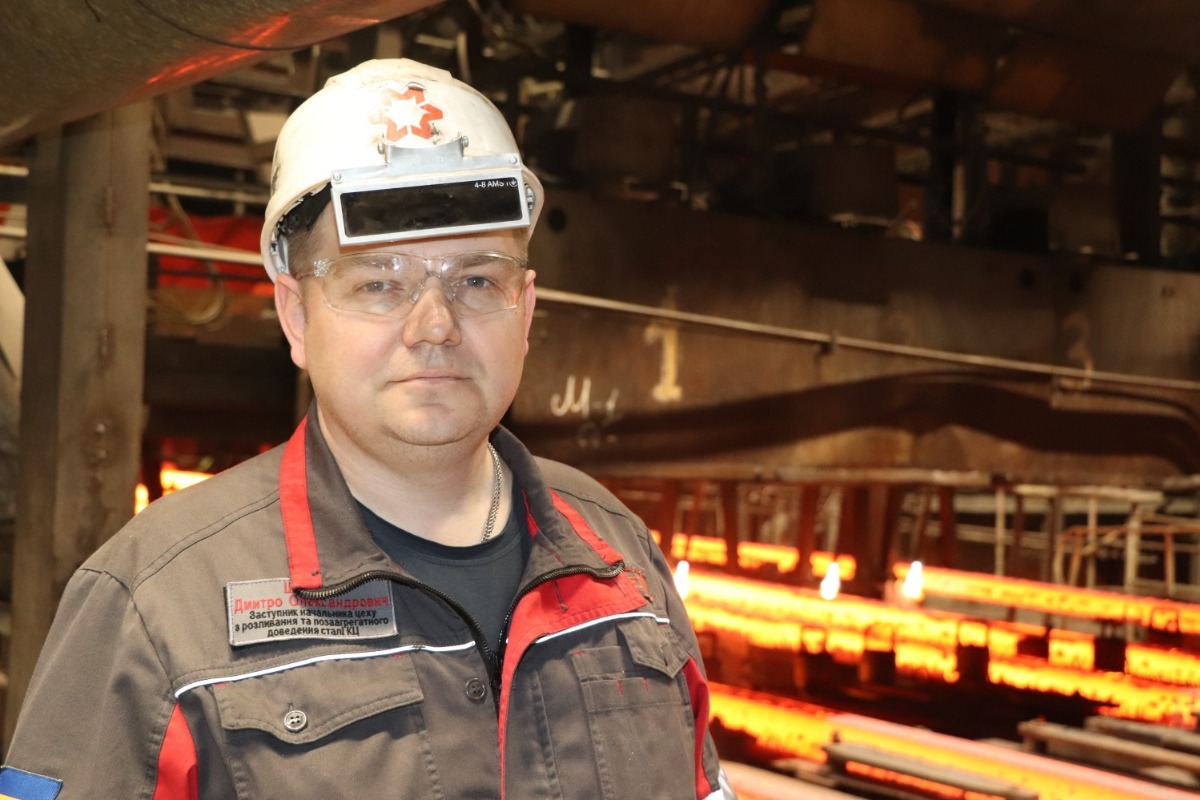
Dmytro Shytikov
It's worth reminding that the main feature of the technology is that the flow of steel is covered by a submerged nozzle in the gap between the tundish and CCM mould. In this way, hot metal is protected from the negative effects of secondary oxidation, which gives the billet improved quality to meet the requirements of customers in both European and domestic markets. This technology makes it possible to produce metal with higher requirements for chemical composition and macrostructure, and the margin profit from it is higher than from conventional billets.
Last year, as part of the programme for new products mastering, specialists of Billet Caster 1 have successfully mastered the production of 200x200 mm CC billets with increased requirements for chemical composition and macrostructure from 40X, 45X1 and 45 steel grades, which are used to produce 130 mm diameter rounds. Successful mastering of the required quality parameters made it possible to transfer the production of such billets from CCM 2 to CCM 1and make the products more efficient. In 2024, 2,940 tonnes of new billets were cast and shipped to Ukrainian and European customers, as well as for the internal needs of Kamet-Steel's rolling mill operators.
Among the key tasks currently being addressed by the team of specialists involved in the programme, in addition to expanding the product line, the primary focus is on developing the AutoStart of the machine's strands during submerged entry nozzle casting. CCM starting in AutoStart mode is primarily about improving the quality of the cast metal by minimising the impact of the human factor on this process.
"Last year, compared to 2023, we made a significant step forward in improving the AutoStart mode for submerged entry nozzle casting, we made over 75% of successful starts without switching to manual mode for the production of 200x200 mm billets and almost 55% for 150x150 mm and 160x160 mm billets. Our goal this year is to achieve maximum AutoStart during casting. To achieve this, we are, in particular, working to improve the performance of stopper cylinders. Totally, in 2024, we produced and shipped 57,306 tonnes of high-quality CC billets to Ukrainian and foreign customers. In 2025, we will continue to expand the capabilities of the submerged entry nozzle casting technology and increase production volumes. The goal is to reach the production of 10,000 tonnes of CC billets per month by the end of the year", says Dmytro SHYTIKOV, BOF Shop Deputy Head for Casting.