Since the start of Russia's full-scale invasion of Ukraine, Metinvest Group, as part of the Steel Front initiative, has been providing assistance to the military in several areas. LIGA.net has covered these efforts in a series of articles. This publication explores the production of mobile metal shelters for Ukraine’s defenders, which are helping to save soldiers’ lives at the front.
The design of the “life capsules” for soldiers
Steel “hideouts” are bunkers made of corrugated steel of various sizes. They can be used in several formats: as shelters for soldiers, as underground hospitals and as command headquarters consisting of several such bunkers.
Mobile metal shelters
Material: corrugated steel 2-4 mm thick
Weight: up to 2.6 tons
Production time: up to 165 man-hours
Durability: withstands the impact of a 152-mm projectile
Capacity: from 6 to 50 people
Features of installation: 3.5 m from the surface of the ground
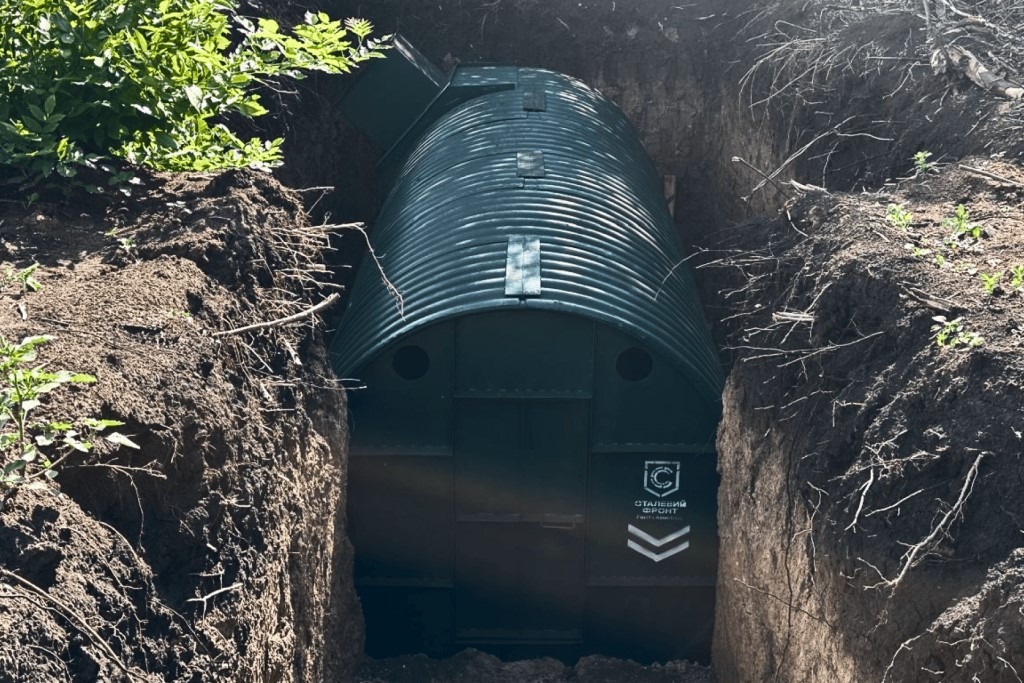
As of October 2024, the Steel Front has supplied the army with over 600 metal “hideouts” of various modifications and 10 command posts. It has also manufactured the country’s first underground stabilisation centre, where military medics are saving the lives of wounded soldiers.
The shelters are delivered to the front line as assembled metal barrels that are buried in designated locations. However, the bunkers are designed in such a way that, if required, they can be shipped in separate segments ready for installation. Once delivered to the front line, the military assemble the bunkers into a single structure and set them up on site.
The idea is not new, but improved
The idea of producing metal shelters is not new, as they also existed in the Soviet Union. However, Metinvest, drawing on the experience of the military and working in cooperation with them, has refined the bunkers, making them more convenient.
At the beginning of the full-scale invasion, the military proposed refining the existing blueprints at their disposal and setting up mass production of shelters. Metinvest engineers, together with the military, made amendments to the existing design. Compared with the original Soviet model, the ‘hideout’s’ length was reduced by two metres to make its installation in field conditions less conspicuous. The structure was also ‘re-cut’ into segments to facilitate its transportation and assembly in field conditions.
As a result, the standard modification of the steel “hideout” is now almost six metres long and two metres in diameter. Inside, specialists have placed an armoury, ventilation systems, a field stove, electrification, hidden storage cabinets in the floor and six bunks for soldiers to rest on. The design of an additional emergency exit was also changed to open inward into the “hideout”. This shelter can accommodate six people.
The military’s experience of using underground bunkers highlighted changes that still needed to be made. The metal “hideouts” continued to evolve based on soldiers’ needs and now come in several modifications. For example, in one of these formats, the beds were replaced with seating, allowing the shelter to accommodate 20 to 30 soldiers.
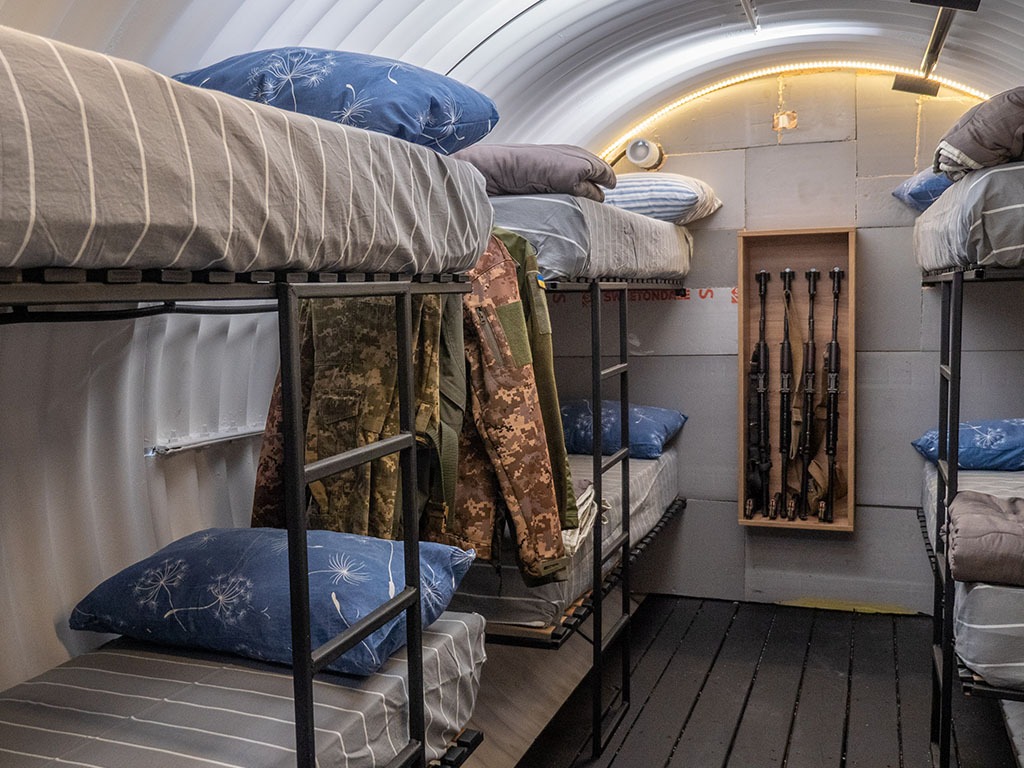
The chief operating officer of Metinvest noted: “A hideout halved in size for drone pilot crews is in high demand. This compact model, measuring three metres in length and two metres in diameter, allows for quick and discreet installation of the ‘hideout’, enabling effective reconnaissance and target engagement by aerial reconnaissance or attack UAV units.”
Proper installation of the shelter is critical to its effectiveness. They are usually buried 3.5 metres or more into the ground. For additional protection, wooden beams are placed on top of the structure and then covered with soil. The military has confirmed that such shelters can withstand direct hits from 152mm shells, some of the most powerful used on the battlefield.
Oleksandr Myronenko stated: “One of the most recent pieces of feedback we received from the military proves that our shelters truly save lives. During a heavy shelling of their position, a group of soldiers went down into a metal ‘hideout’. A KAB-250 exploded nearby, blocking the exits with soil. We maintained constant contact with them, and as soon as their comrades had the opportunity to reach and unblock them, they did so. Thanks to the proper installation of the shelter and the placement of the ventilation openings on the surface, all the soldiers were safe.”
Currently, the Group notes that Metinvest has reached its maximum capacity in military production volumes. Increasing mass production to supply the army with the necessary steel products requires certain conditions, such as engaging more specialists. Today, manufacturing products for the army represents an additional task for metallurgists and miners who are being diverted from their main production activities (steel, semi-finished products and raw materials). Hiring new people is challenging due to migration, mobilisation, issues with deferments and more. The possibility of establishing a permanent team of specialists involved only in the fulfilment of government orders would help to strengthen this area, increase production volumes, and so on.
Production of steel shelters
Stage 1. Preparation
Corrugated sheets are rolled to give them a radial shape. This enhances the structure’s rigidity.
Stage 2. Assembly
Like a LEGO set, the future shelter is made up of individual elements. Experienced specialists use cranes and welding to connect them into a single unit, giving the structure the required shape.
Stage 3. Painting
After thorough cleaning, painters apply a layer of camouflage paint using a spray gun. This serves as an additional measure of safety and invisibility during transport and installation.
Security area for field headquarters
Drawing on its experience in manufacturing steel shelters, Metinvest has improved the bunkers that make up command posts and underground hospitals at the army’s request. Since military commanders and medics with wounded soldiers spend extended periods inside, the bunkers were enlarged in both diameter and unit length.
The command post comprises five to six interconnected underground “hideouts”. Each compartment performs its own function: living quarters, a sanitary area, command headquarters, and so on. They are equipped with showers and boilers, as well as heating, lighting and communication systems, and electronic equipment.
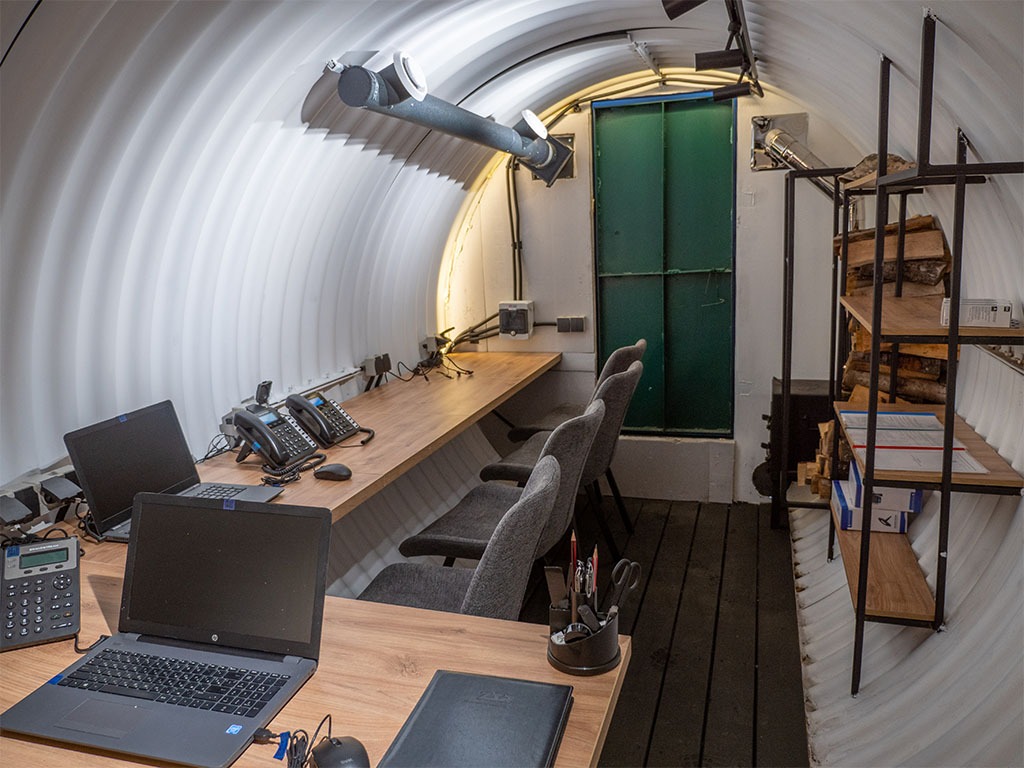
Experience in using command posts has shown that they can be equipped with both electronic warfare protection and internet or other means of communication. Such equipment allows the headquarters to serve for a long time as a shelter and as a place for personnel to rest and work.
Command posts are installed at a depth of at least 3.5 metres. Several layers of soil and wood are laid on top of them: this layer is at least 1.5 metres thick. This method ensures the protection of the military and creates comfortable conditions even during the cold season. Assembling a bunker takes a team of six to ten soldiers approximately eight to ten hours.
Oleksandr Myronenko stated: “People’s lives are the priority at the front line. That is why Metinvest contributes to their preservation. If we can make the space not only safe for the military, but also comfortable, we do so. We will work to ensure that more such command posts are established on the front line and that the ‘underground towns’ are a reliable support for the command of military units.”
Rescue space for the wounded
Ukraine’s first underground stabilisation centre on the front line was established in September 2024. It is based on the same steel bunkers manufactured by Metinvest. The underground hospital is designed to accommodate a grouping of troops at the OTG scale (an operational and tactical grouping that can subordinate various branches of the military and security forces in a specific region). Metinvest states that its specialists have several developments for brigade and battalion levels.
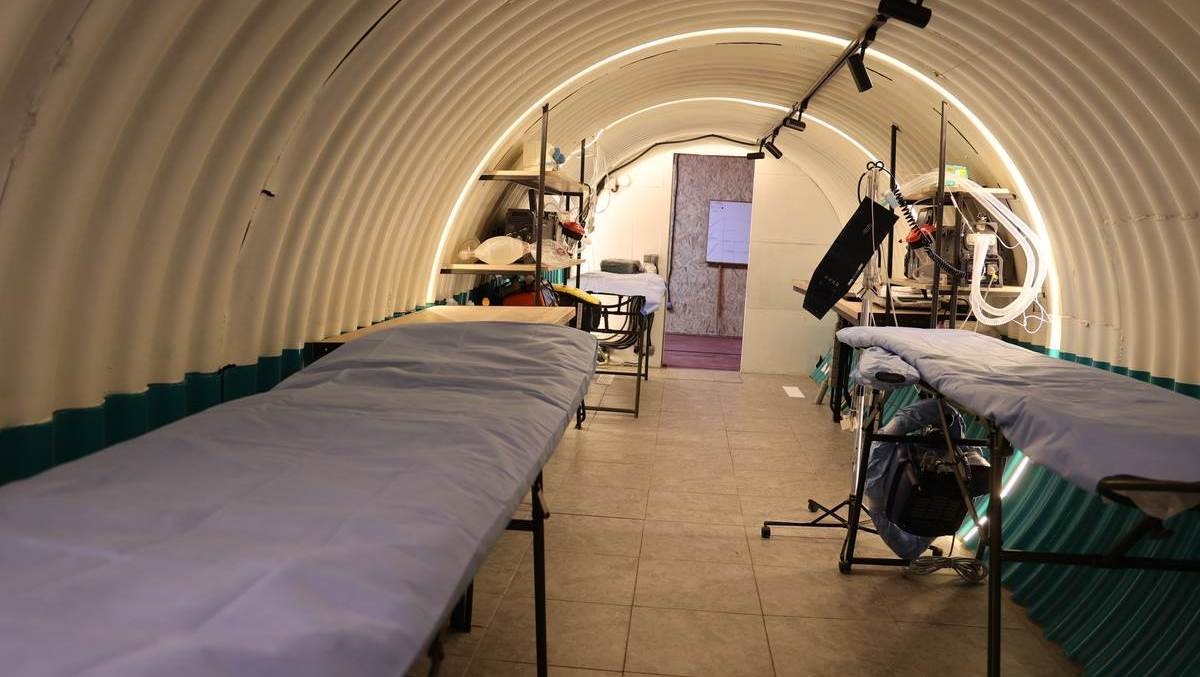
The hospital was developed in cooperation with military medics, whose suggestions and comments were incorporated during the design stage. It took four months from the project idea to its implementation. According to Oleksandr Myronenko, during this time, the Group’s specialists remained in constant contact with the medics to refine the project, if necessary, based on operational adjustments. For example, at the final stage, a restroom and a recreation room were added to the hospital for soldiers who are feeling better and waiting for evacuation.
Metinvest’s chief operating officer noted: “Roman Kuziv, the acting commander of the ‘East’ medical forces, approached us with the idea of creating an underground hospital, and we began implementing it. At later stages, we involved specialists from the Ministry of Defence and the Medical Forces Command.”
The unique feature of the underground hospital lies in the fact that it is a full-fledged medical facility with the necessary equipment, two operating rooms where medics can perform surgeries of any complexity, as well as stabilisation and intensive care units. Its capacity is up to 100 wounded per day.
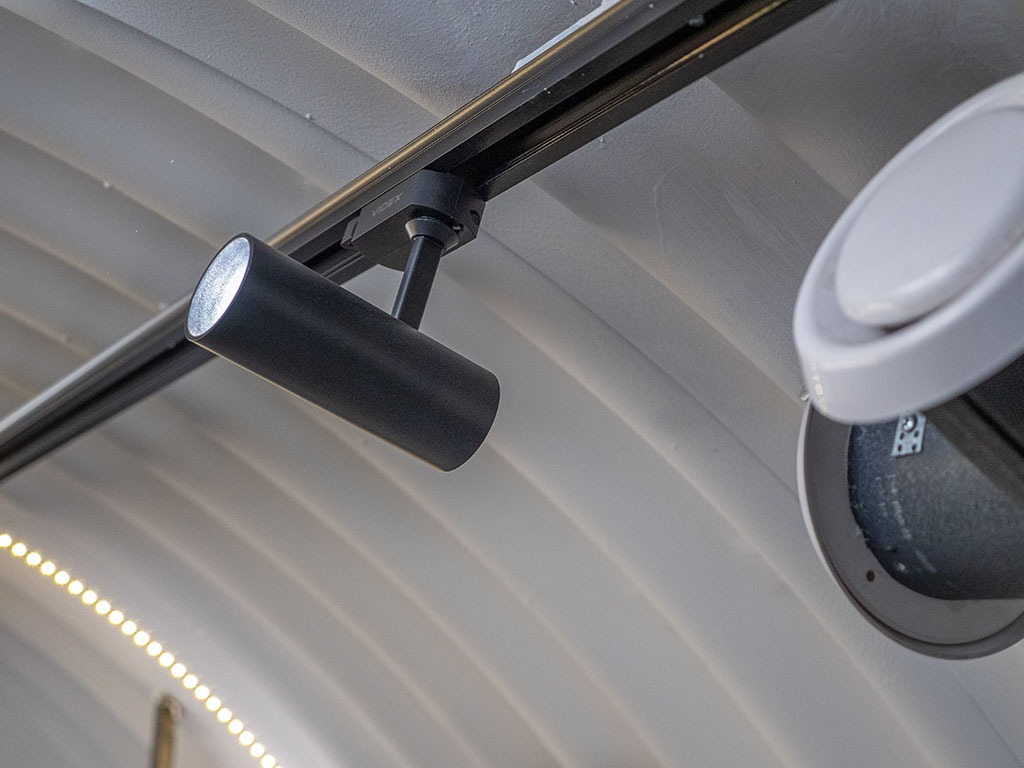
The underground facility is equipped with modern medical equipment, some of which was supplied by the Ministry of Defence and military medics. The equipped surgical rooms include everything from medical aspirators to blood pumping systems. In addition, military medics provided the hospital with specialised equipment for the emergency treatment of wounded soldiers. Metinvest Group supplemented the medical equipment by purchasing cardiac monitors, oxygen concentrators and ventilators.
The hospital is energy-independent. This is ensured by two generators housed in separate underground facilities nearby. The generators can supply electricity to the hospital in case of power outages in the mains. Water is sourced to the hospital from an underground well, the sewerage system is well-designed, and the underground hospital is supplied with air through a supply and exhaust ventilation system.
The process of installing an underground hospital is somewhat more complex than that of a “hideout” or command post. It is currently installed several kilometres from the “zero” line at a depth of six metres. It is covered with three to four layers of protection made of wooden logs, sandbags and soil. The installation of this facility involved drilling rigs, excavators and cranes.
Strong need for underground hospitals on the front line
The cost of an underground stabilisation centre set up by Metinvest is UAH20 million. Of this, UAH13 million covers the cost of metal “hideouts”, their arrangement and installation, while the medical equipment is valued at UAH7 million. While this is the first example of such underground hospitals, the need for them is strong.
The development by Ukraine’s specialists has virtually no analogues in the world. Similar modular hospitals exist and offer a similar range of services. However, these are ground-based modular hospitals that are easy to detect and destroy.
I am convinced that Ukraine’s experience of resisting large-scale aggression from a state with a powerful military potential will be a valuable asset for our Western partners. The war with Russia, which possesses modern weaponry, has forced us to seek effective methods of defence, such as relocating vital facilities underground. In contrast, Western armies have traditionally prepared for local conflicts with a less equipped enemy, resulting in a different approach to military construction.
Production has been put on stream
Since 2022, when Metinvest started producing the metal bunkers that serve as the basis for “hideouts”, command posts and hospitals, the process of their production has been streamlined, becoming systematic and significantly faster.
Oleksandr Myronenko noted: “Currently, the approach to our steel production has changed. The site is simultaneously working on a series of shelters, rather than individual orders, as was the case in the past. The workload across the sites is fully aligned with their capabilities and capacities. Since the launch of steel shelter production, we have continuously received requests for their supply. This demonstrates genuine feedback on the quality, reliability and necessity of our developments on the front line.”