In the rolling shop of Kamet Steel, team efforts have successfully mastered the in-house production of pipes of a laying head for the 400/200 mill coil line.
This spiral pipe is one of the important elements of the laying head rotor and plays a key role in the process of forming wire rod coils. An important condition is compliance with the configuration of the laying head pipe, the established bending diameter, a deviation from which can lead at least to an inaccurate fitting position of this equipment in the rotor and the formation of coils that will not meet the requirements of consumers.
Until recently,similar foreign-made replaceable equipment was used at the process line 200. Working in wartime conditions, logistical and financial difficulties, including the supply of equipment and materials, systematic efforts to improve production efficiency have set new demands on rolling mills, and the need to manufacture laying head pipes using their own resources has become one of the top priorities.
To solve this unusual task for the unit, the team, that brought together highly professional process engineers led by Igor Stupaiev, head of the 400/200 mill section, and experienced repairmen, had to go through a lot of trials and errors. A positive result was obtained once again by virtue of the synergy of different sections of the rolling shop and the teamwork of roller operators.
In particular, the optimal mode of heating the pipes before bending was achieved in the reheating furnace of the ball-rolling section. Process engineers have built a clear algorithm of their roles and actions on a special machine for bending pipes, according to which, in less than a minute and a half, while the heated metal retains its ductility, they have time to accurately direct the heated pipe to the receiving chute, clamp and obtain an element of the required configuration.
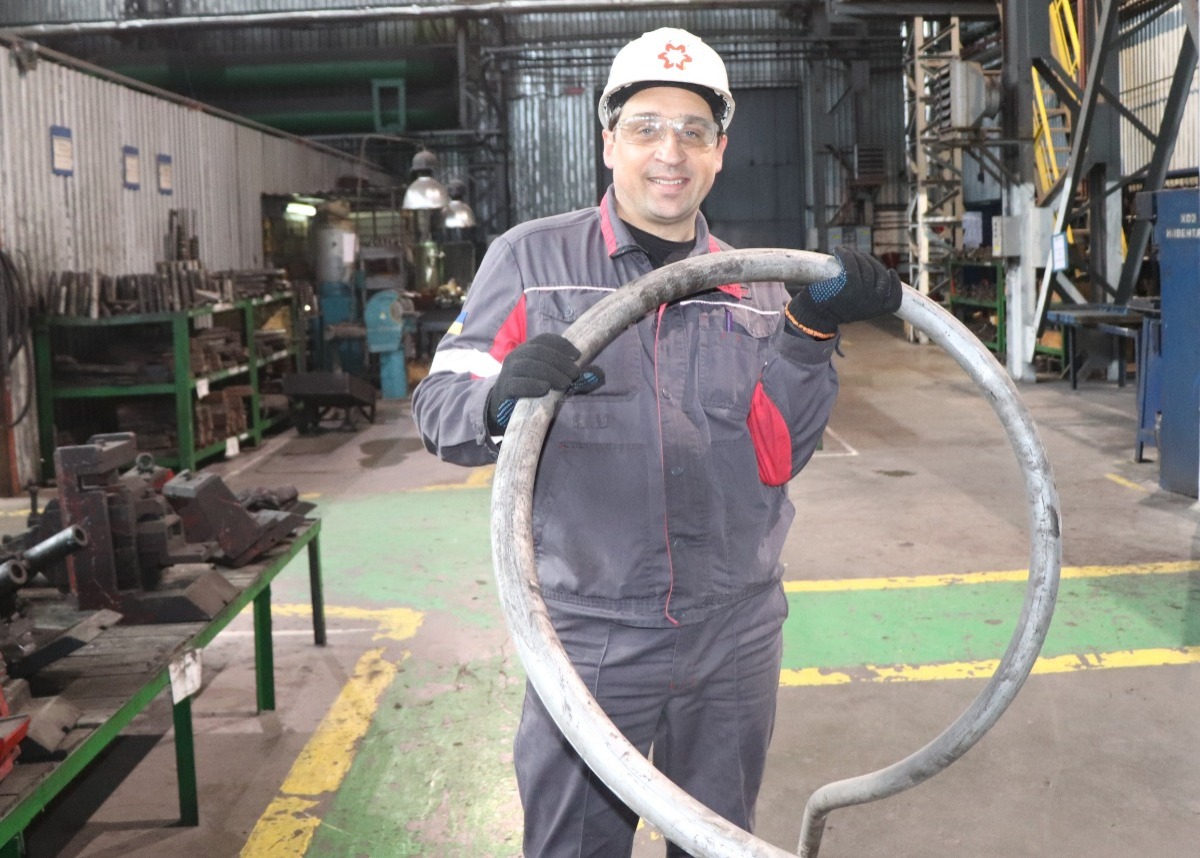
Oleksiy Tymoshenko
Along with this, the process engineers gained skills in using a special pin of the machine for fixing the pipe, thanks to which it was possible to avoid shrinkage of the material during cooling and the loss of geometric parameters of the curved pipe.
"The task of manufacturing our own laying head pipes required a non-standard approach from us. We carefully studied the documentary technical literature and video materials, which recorded the successful experience of such works at similar mills of European enterprises. And, of course, each time they thoroughly analysed their own numerous attempts. Finally, the quantitative factor turned into a qualitative one – they decided on the optimal heating of the pipes, learned how to use all the capabilities of the machine, increased the length of the lower part of the pipe and thereby strengthened its configuration.
This year, the coil line operates using only our alternative pipes. In difficult wartime, we reduced the dependence of production on foreign supplies and logistics, reduced downtime for replacing this equipment. The results of the work proved that our laying head pipes are three times more stable than the ones purchased earlier: earlier, the need to change this equipment arose after rolling 10,000 tonnes of wire rod, and now we can process more than 30,000 tonnes. At the same time, the cost of replaceable equipment made on our own is three times less than the cost of purchased one. Therefore, thanks to our joint team efforts, we are systematically increasing the efficiency of the rolling shop," said Oleksiy TYMOSHENKO, 400/200 mill foreman, one of the initiators of the development.