According to the results of the work done last year, the team of the pelletizing plant at Central Iron Ore was awarded a certificate of honour and a financial incentive from Metinvest Group as one of the best divisions among all Iron Ore plants. The team honourably concluded the year and began 2025 with high productivity and operational improvements.
Particularly, the operational program fulfilment ensured a high assessment of their work. Throughout 2024, the pelletizing plant maintained 100% capacity utilization, with the shop operating at its maximum productivity of up to 298 tons of pellets per hour. In total, the plant produced about 2.2 million tonnes of high-quality products. The pellets were shipped to the European market and internal customers.
During the year, some investment projects at the pelletizing plant were implemented to ensure stable production. Major overhauls of the OK-324 induration machine complex were carried out twice, in March and November.
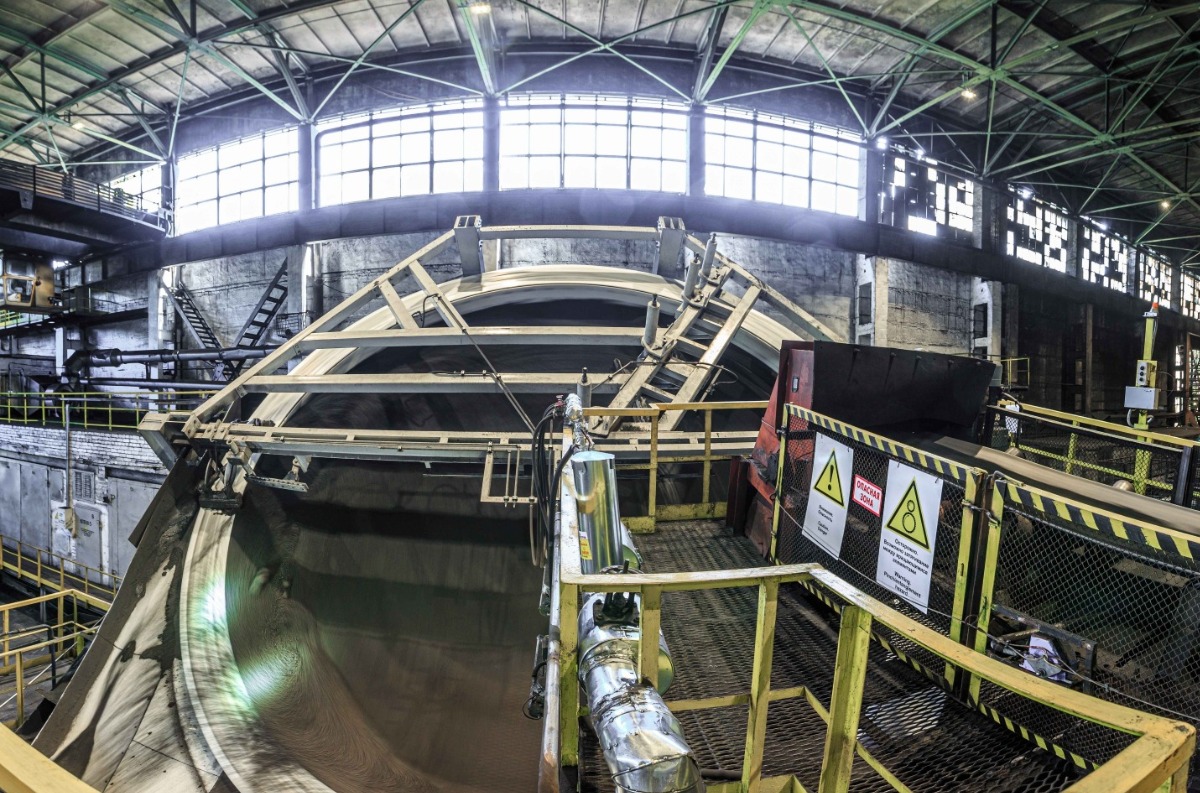
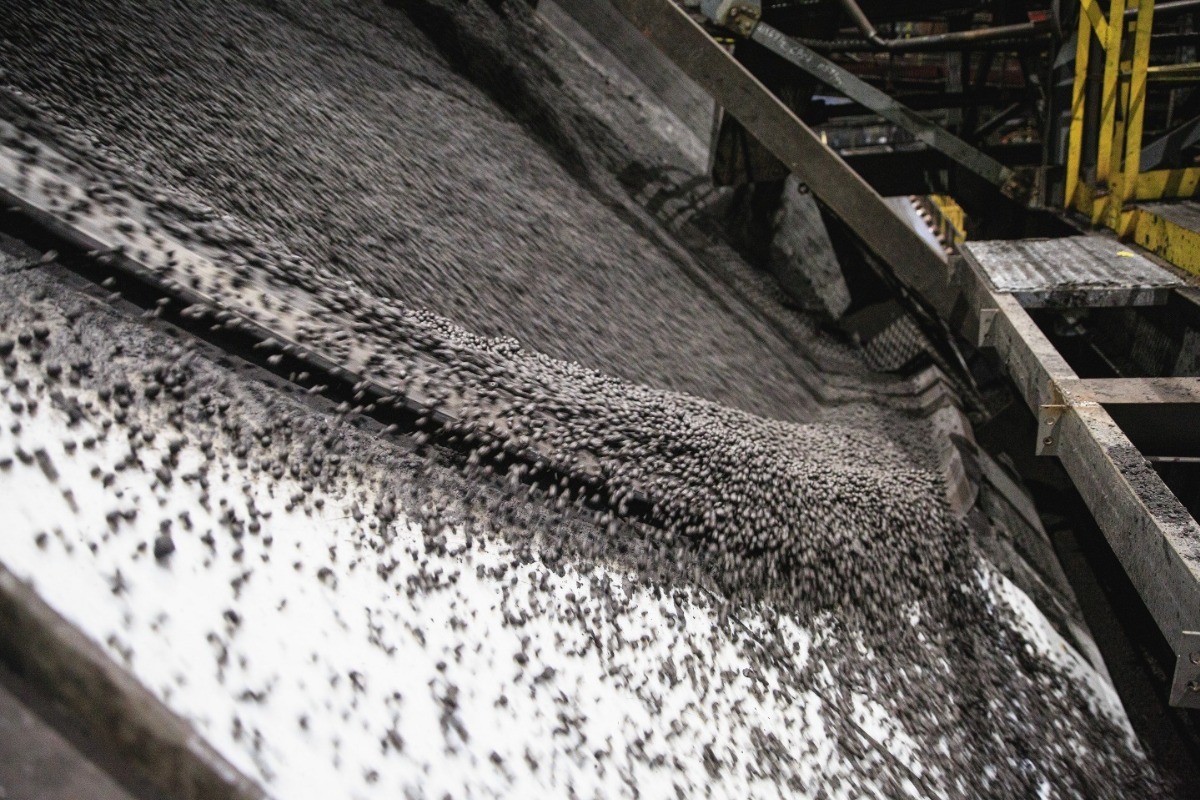
The specialists restored the refractory lining of the induration machine hearth and conducted repairs of six prechambers. A shaft-turning gear for the smoke exhauster was also installed, significantly reducing its operation time during scheduled preventive repairs at the plant. The installation of the mechanism reduced energy consumptions and increased equipment's reliability. To reduce environmental impact and improve energy efficiency, two drift eliminators were partially replaced on two smoke exhausters, and gas duct repairs were conducted on two other smoke exhausters. All of these measures ensure the reliability of the entire equipment complex.
The main focus areas of the plant's operation are specific consumption rates for gas and electricity, as well as consumables such as biofuel, bentonite, etc. The working groups' participants meet regularly to discuss promising efficiency ideas, and also communicate with their colleagues from Northern Iron Ore to share valuable and useful developments.
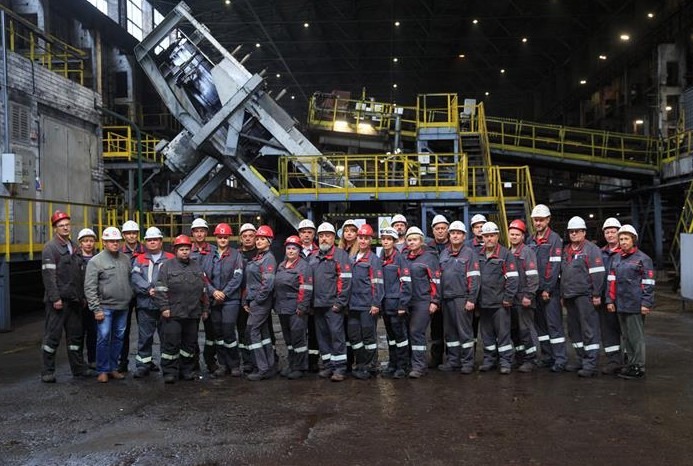
As a result of the systematic work, the plant implemented a number of operational measures last year. Thus, the installation of the shaft-turning gear of the D3 smoke exhauster and the automation of closing the D-6 smoke exhauster guides contributed to electricity saving. In addition, the replacement percentage of natural gas with biofuel increased from 50% to 53% during the year, contributing to further saving. The specialists also implemented other energy-efficient projects.
"Timely repairs along with equipment modernisation and automation of certain processes allow us to maintain a stable production rhythm, meet all quality requirements for iron ore raw materials and fulfil the established customer order volumes," notes Andrii ZHYLKINSKYI, head of the pelletizing plant at Metinvest's Central Iron Ore. "On the other hand, current times require us to examine all processes even more carefully and focus on developing measures to reduce our key costs, contributing to the plant's sustainability. That is why the plant team continues to develop and implement innovative solutions and practical ideas for the optimal use of resources in production process and enhancing production efficiency."