The BOF shop is continuing to implement an investment project for the revamping of electrical equipment of continuous casting machine No 2. The first stage to equip three strands of the machine with modern frequency converters has been completed.
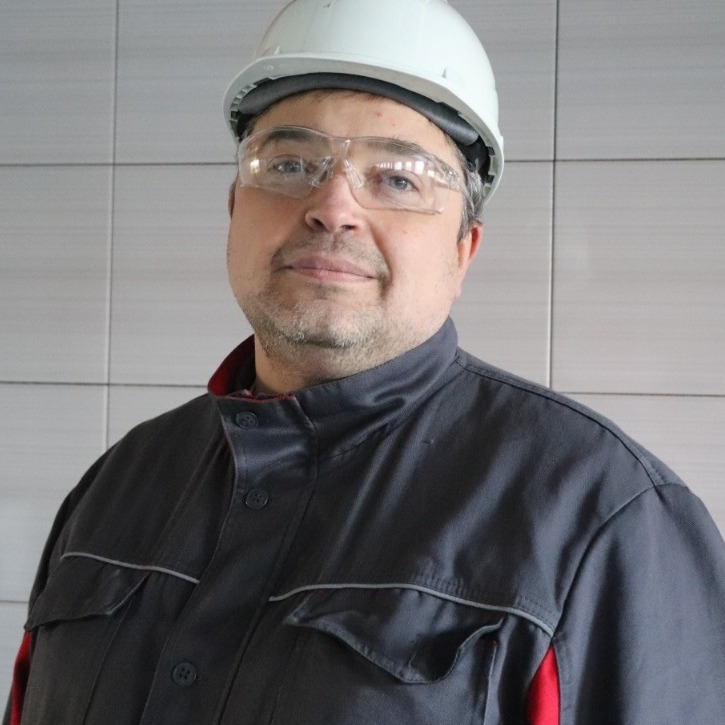
Олександр Дегтяренко
The revamp aims to increase the operational reliability of CCM No 2, primarily by reducing the unscheduled downtime of electrical equipment and avoiding emergency outages.
To this end, the electrical system undergoes a phased replacement of analog converters with modern DC and frequency converters designed to regulate the operation of electric motors of all machine mechanisms.
The first to third strands and the so-called common mechanisms have been fitted with new frequency converters during the first stage. Previously, one group of motors was fed from one converter.
Now each of upper and lower stand mechanisms have been equipped with individual converters, enabling to improve their performance, response time and quality of control. Mechanical loads on the stands have also been reduced through the use of individual drives.
Oleksandr DEHTIARENKO, lead engineer for the revamping of the BOF shop,
"Results of the first stage of the revamp confirm the stabilisation of the casting speed of the strands, enabling to achieve a higher billet cutting precision and hence to reduce cutting losses. It is also now possible to use the reduction mode, which allows us to improve the macrostructure of the steel to a certain extent and more accurately maintain the geometric parameters of the continuously cast billet. The new equipment is equipped with automatic monitoring systems that provide the site's electrical personnel with up-to-date information on the technical condition of the equipment. Modern software makes it possible to implement a self-diagnostic system for the drives, which provides instant feedback to the specialists and hence reduces the troubleshooting time."