An investment project to modernize the electrical equipment of Continuous Casting Machine No. 2 (CCM-2) has been successfully completed in the BOF shop of Kamet Steel.
The reconstruction was carried out in two stages. Last year, new frequency converters were installed on the first, second, and third strands of the machine. Recently, specialists completed the second stage by upgrading the equipment of the fourth, fifth, and sixth strands. In parallel, the automation system of CCM-2 was also replaced.
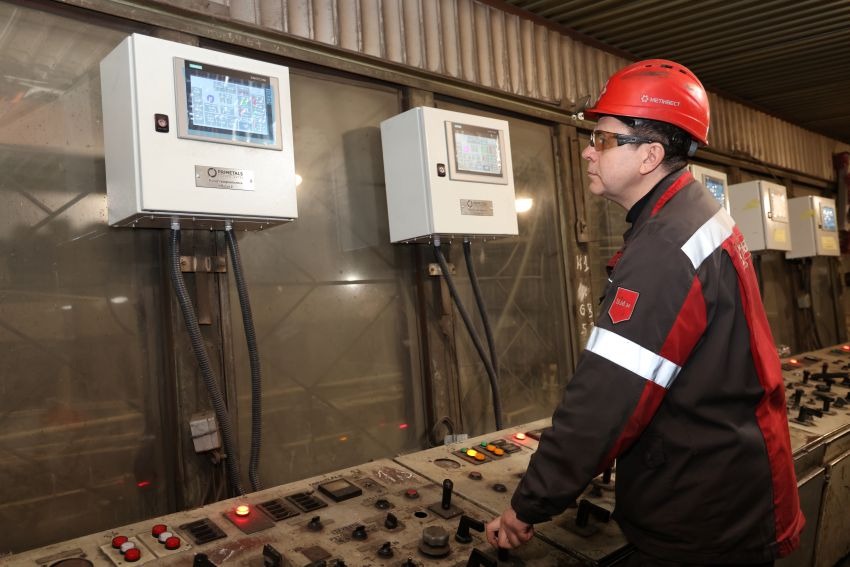
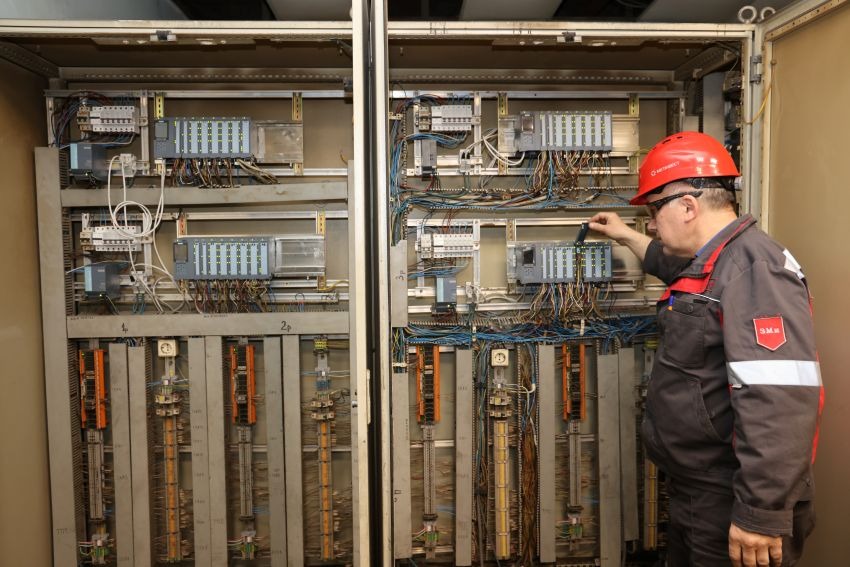
The key objective of the project was to ensure the reliable operation of the electrical equipment and the automated process control system of CCM-2. Another important goal was to stabilize the casting speed, which helps achieve more precise cutting of billets and reduce metal waste.
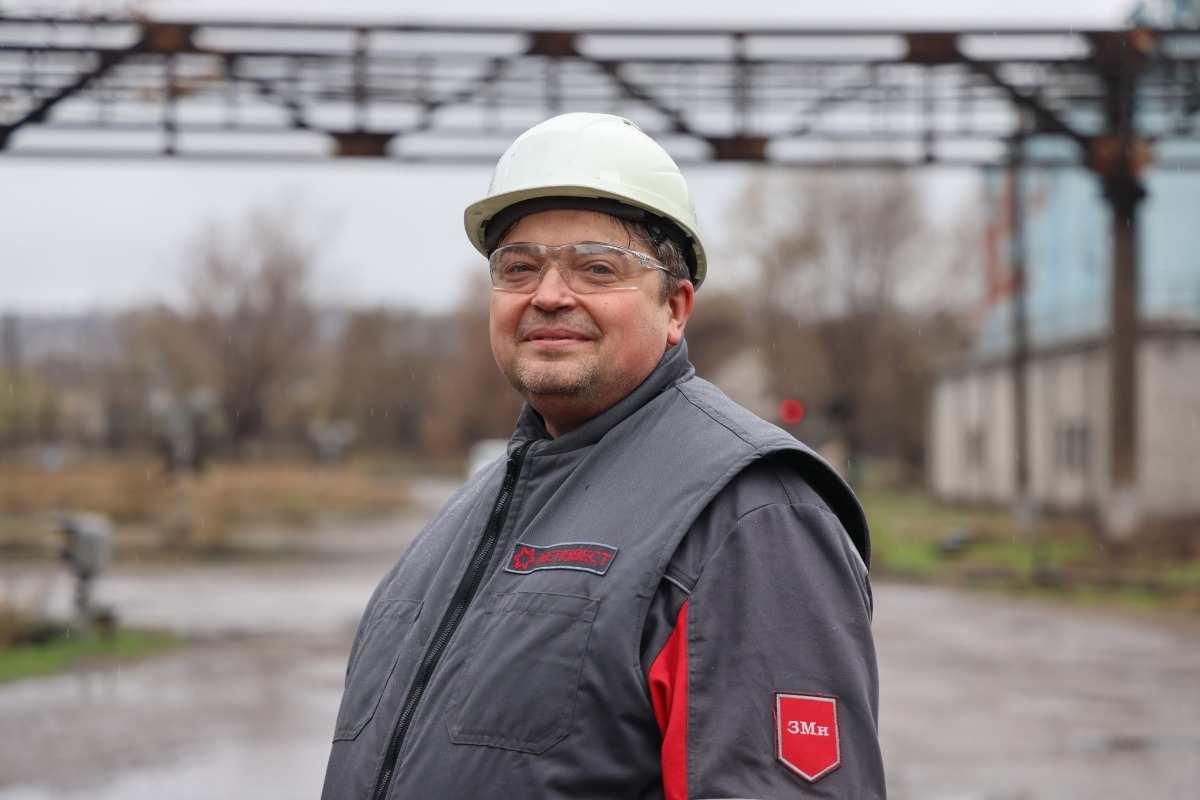
Specialists also introduced a visualization and monitoring system for the steel casting process. With new control panels installed on the machine, steel casters can now track casting parameters in real time and analyze data to improve the quality of the final product. Additionally, the implementation of a compression algorithm will enable smoother bloom surfaces.
Oleksandr DEHTIARENKO, lead reconstruction engineer of the BOF shop, commented:
“During the reconstruction, DC converters were replaced with modern Siemens drives designed to control the motors of all machine mechanisms. Encoders were installed on the motors to ensure the most stable casting speed, and control systems for the secondary cooling zones were also upgraded.
Now, CCM-2 is equipped with additional panels that display the casting speed of each strand and transmit key signals required by operating personnel during the casting process. The implementation of modern automation and control systems will allow for more accurate process control, ultimately improving the quality of finished products.”