In the energy business units of Kamet Steel, systematic work is in progress to improve the reliability and energy efficiency of key equipment. In the CHP, a large-scale overhaul of turbo blower # 1, which ensures a stable supply of blast to the blast furnaces of the enterprise, is being performed.
As part of the overhaul, it is planned to restore and replace key equipment along the entire process chain of the turbo blower No.1. In particular, a steam turbine requires significant repair intervention. First of all, the steam rotor blades will be completely replaced at the contractor's repair site. In the flow channel, more than half of the diaphragms and all end and intermediate seals will be replaced, which prevents inefficient steam losses. Also, the key technical components of the compressor will be carefully checked and repaired - rotor, diffusers, seals, etc.
Significant attention is paid to the revision and restoration of the auxiliary equipment of the turbo blower. In particular, two condensate pumps will be replaced with new ones. In the future, power engineers hope for their trouble-free operation, which will reduce the loss of condensate water when it is returned to the boiler shop. Low-pressure heaters, ejectors that provide air removal from water chambers when the condenser is put into operation, shut-off valves, etc., are also being repaired.
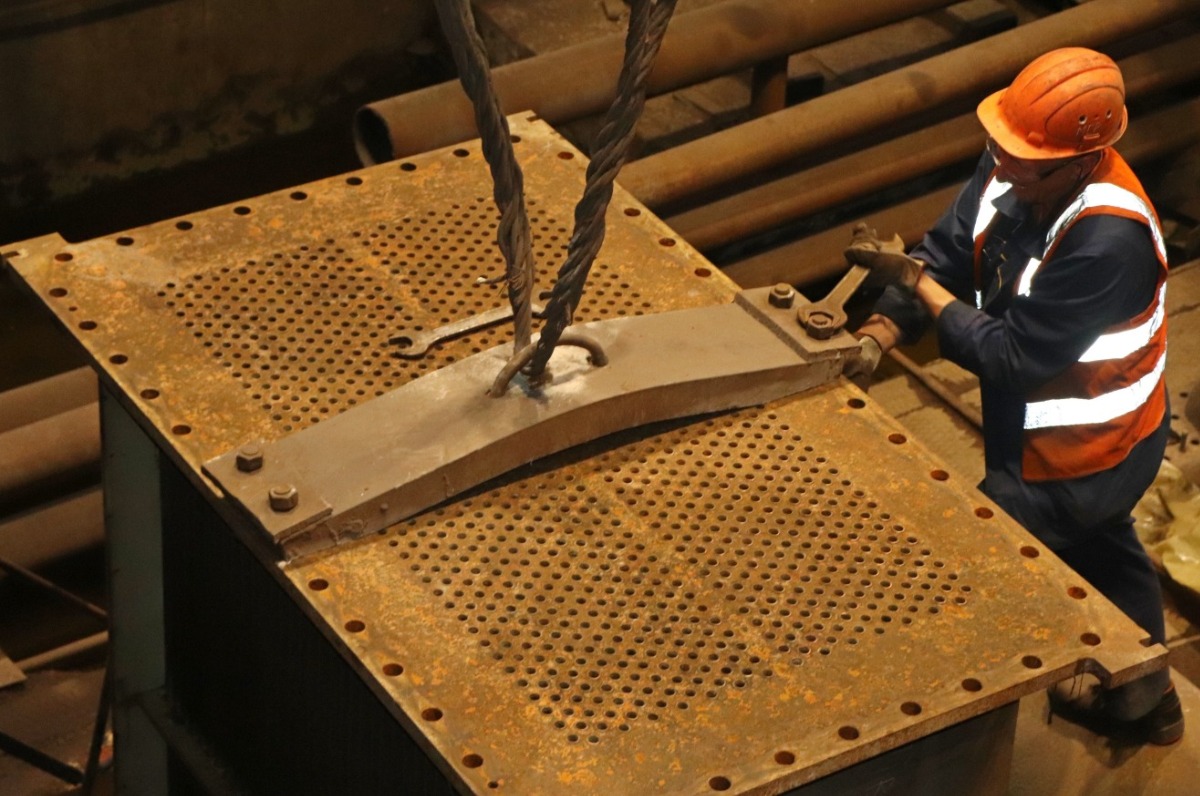
Serhiy PODOLSKYI, Head of the Turbine Shop of the CHP:
"We carry out the main task – to produce blasting of the specified parameters for the blast furnace shop, while reducing the specific steam consumption and ensuring reliable and energy-efficient operation of the unit equipment. As part of the overhaul, we are planning to modernize the control and protection system of turbo blower #1.
Given the new modern electronic equipment and software, we hope to completely switch to automatic adjustment of the blast supply parameters according to the needs of the blast furnace shop and minimize the loss of oxygen-enriched blasting at the blast furnace SNORT."