The life of soldiers on the front line is far from the comfort of Kyiv apartments. Arranging heating, getting hot food, taking a shower or sleeping comfortably can be a difficult logistical task for a unit. This is not just a matter of whim – the health of defenders and their effectiveness in combat depend on their living conditions.
Ukraine declares that the life of a defender is of the highest value. The scale of the war makes it impossible to quickly set up modular kitchens, baths and underground shelters for all military personnel.
Structures on the front line must not only serve their primary purpose but also provide protection against shells. They should also be versatile and suitable for mass production, enabling their deployment along the entire front line, which spans more than 1,000 kilometres.
Ukrainian steelmakers have undertaken the implementation of this project. Metinvest employees, in cooperation with the military, have developed versatile shelters that are now being welded in their hundreds at several classified sites.
The Group’s shelters have become part of the defensive fortifications around Pokrovsk, a strategic city for Ukraine’s steel industry and where the fiercest fighting is currently taking place.
Shelters for any situation
From the outside, Metinvest’s shelter resembles a large metal barrel, but, inside, it is equipped with everything a soldier needs. This includes ventilation, beds for sleeping, a desk, heating, a toilet, water drainage, emergency exits, space for personal belongings and so on. These metal “hideouts” can be customised for any purpose.
They are available across a range, including headquarters dugouts equipped with computers, kitchens or simply living quarters with several sleeping places. One of the new modifications includes a mobile underground hospital featuring all the required medical equipment. It can accommodate 100 wounded per day while doctors can provide urgent care right next to the front line.
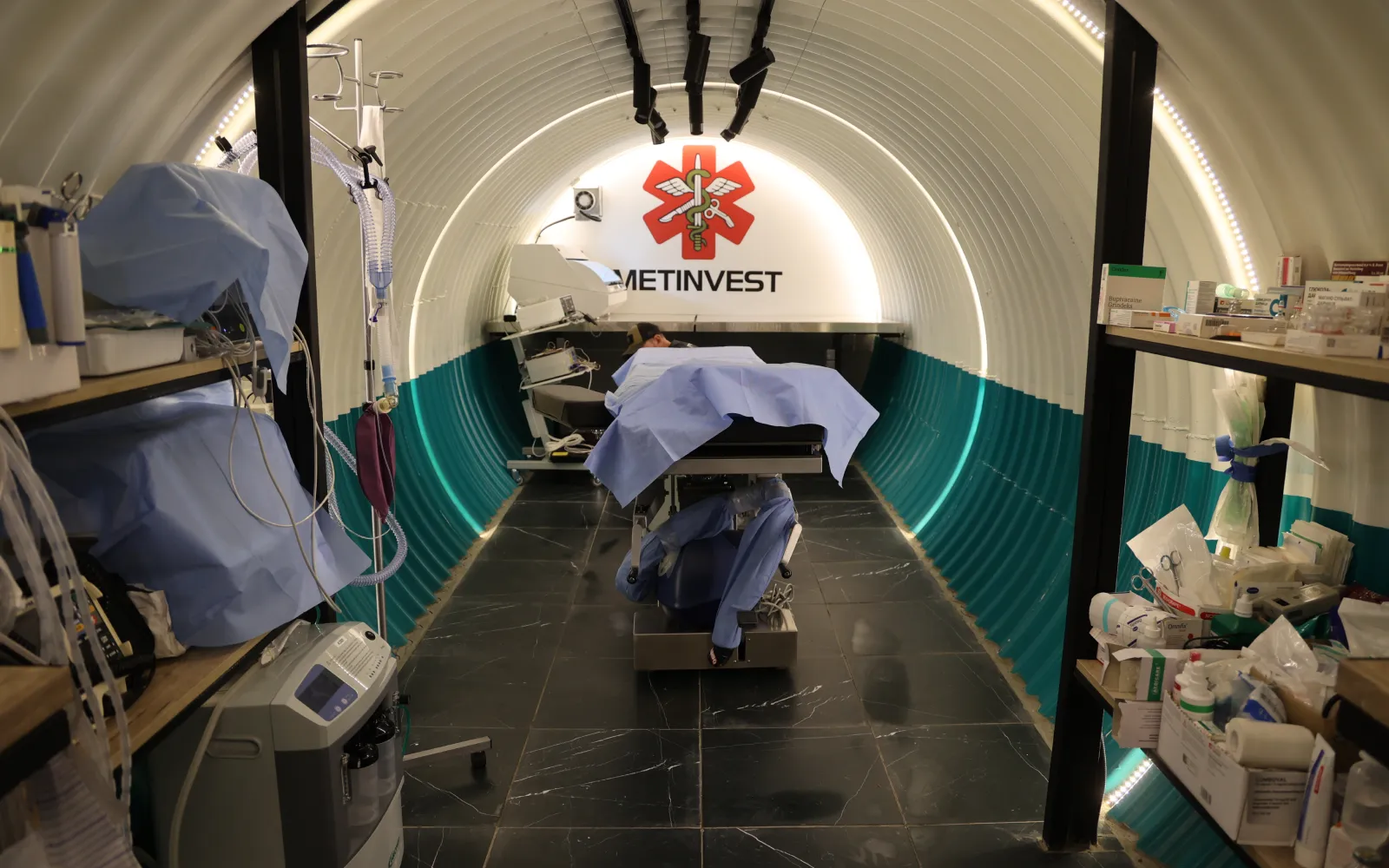
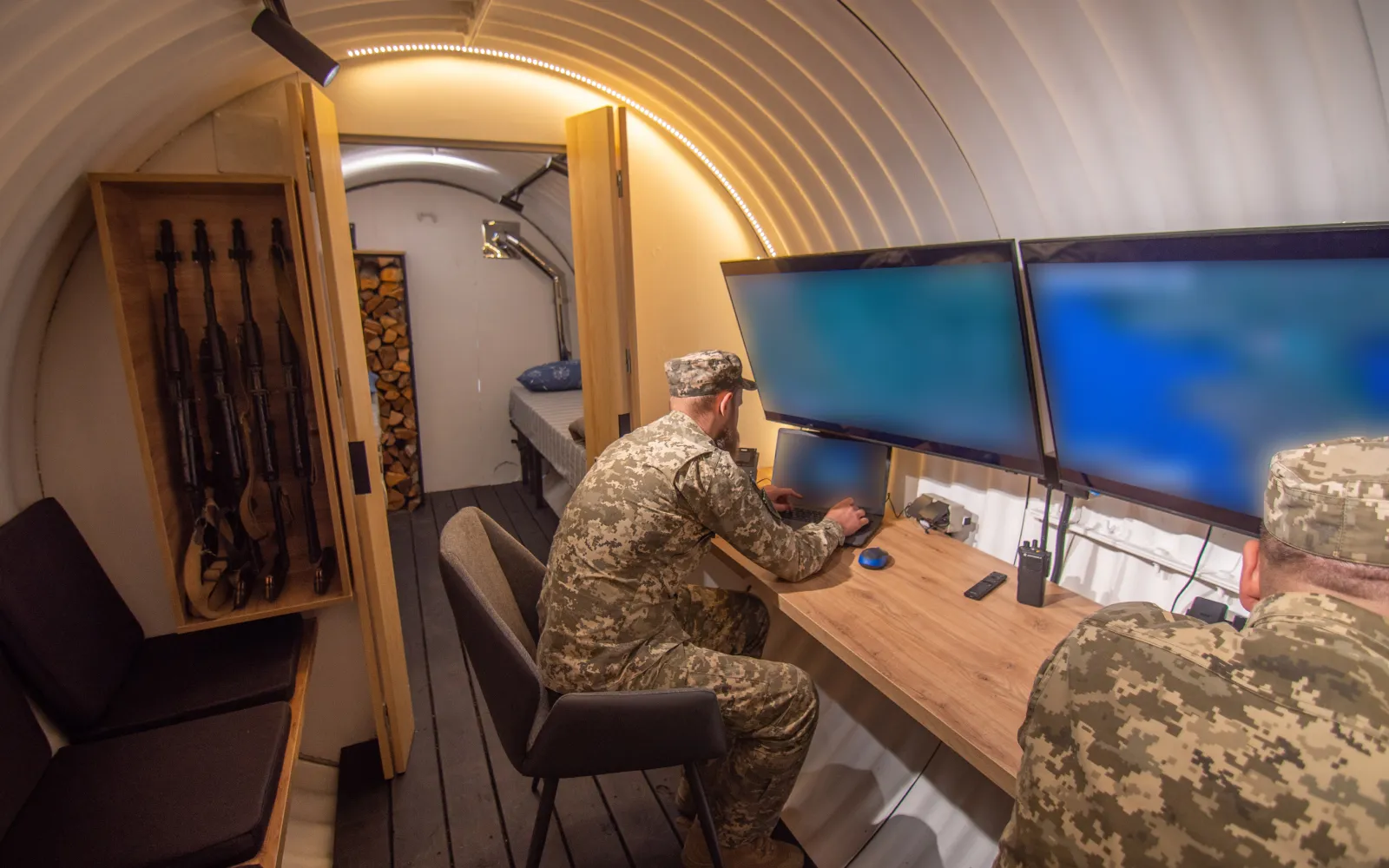
Mobile underground hospital |Headquarters dugout
The basic model is six metres in length and over two metres in width. This barrel can accommodate up to six people in bunks and provides up to 30 soldiers with shelter from shelling at the same time.
The steel is 2-4 millimetres thick. The hideout is buried several metres underground and can withstand a hit from the most common Russian 152 mm shell.
Saturating the front line with such shelters is no easy task. Each barrel weighs more than two tonnes. This means that to produce100 hideouts – enough to cover a small section of the front – the Group must source over 200 tonnes of high-quality sheet steel.
The manager at one of the production sites said: “We reviewed many historical blueprints. We analysed which structures could protect against specific threats. We combined the best ones, optimised them to meet the current needs and requests of the defence forces and ended up with a lightweight yet sufficiently protective structure that is suitable for mass production”
The metal must then be transported to the production site and processed into a special corrugated shape and bent into a rounded radius to enhance the structure’s rigidity. Using cranes, individual parts are assembled into a single unit and coated with camouflage paint to ensure safe transport.
Several different sites have been launched simultaneously in classified locations, performing their part of the work or duplicating each other for increased mass production.
The entire process involves rolling mill operators, boilermakers, crane operators, gas cutters, metal structure assemblers, painters and many other specialists. Each shelter takes up to 165 man-hours to produce.
Installing such metal capsules on a front line position is no trivial task. The design must allow for transport and installation in the shortest possible time. To integrate them into the fortification system in the southern part of the country, Metinvest deployed dozens of its own excavators and engaged 100 people working directly in the war zone.
Metinvest increases production of defence products
As of September, the Group has supplied over 600 hideouts to the military, producing 40-50 of them per month. The cost of one item is approximately UAH450 thousand. Production costs vary depending on the shelter modification and the complexity of its equipment. Metinvest supplies the hideouts to the front line free of charge, but this initiative has already cost the Group at least more than UAH300 million.
Since 2022, Metinvest Group has allocated around UAH7.7 billion for the needs of the Armed Forces of Ukraine and civilians. Of this amount, approximately UAH4.4 billion was directed specifically to meet the needs of the Ukrainian army, 60% of which consists of products manufactured at the Group’s enterprises. These include mobile shelters, mine trawls, protective screens for armoured vehicles, anti-tank hedgehogs and more.
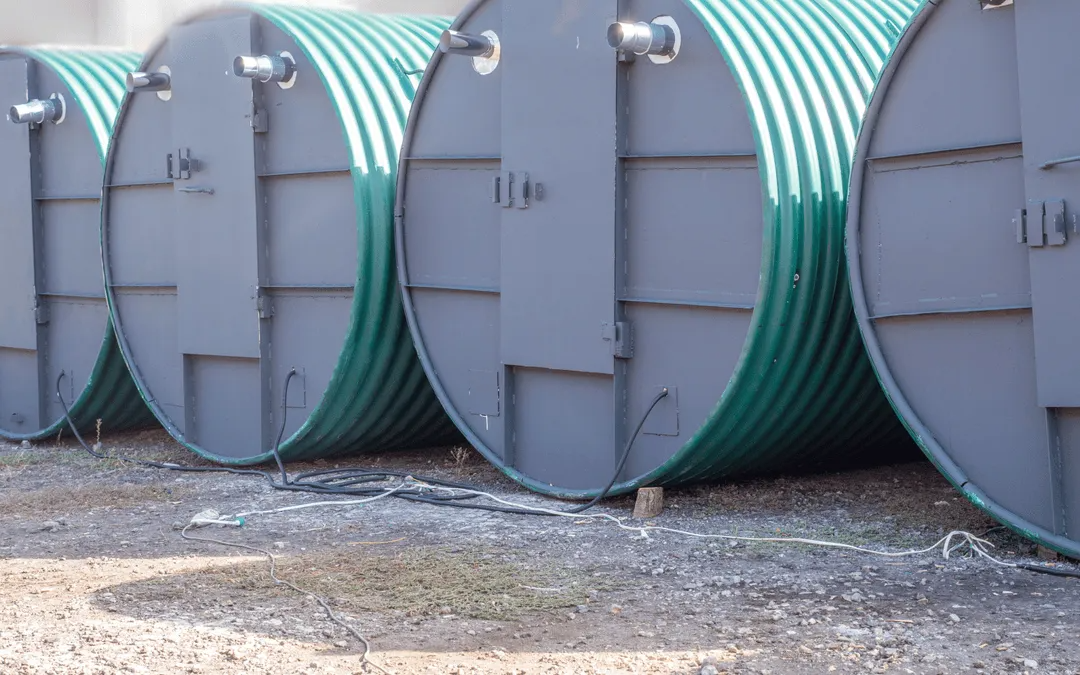
The universality of the structure allows for mass production of shelters
According to Oleksandr Myronenko, Metinvest’s Chief Operating Officer, the Group is capable of significantly increasing the production of underground shelters, but this would require direct contracts with the Ministry of Defence. As the products have already proven their effectiveness in combat, negotiations are currently underway for the first government order.
To make this possible, the structures are already undergoing an official certification process, which paves the way for the first contracts.
The manager at one of the production facilities said: “We develop design documentation, manufacture a few products and contact the Ministry of Defence. A specialised military unit tests our shelters using artillery shells, which are typical enemy weapons. If the tests are successful, we receive a quality certificate, present it to the state customer and offer them the ability to purchase our product.”
Government contracts will allow the Group to defer workers involved in the production of structures, create new jobs and obtain funding for the further development of the technology.
It is more cost-effective for the army to purchase modular shelters in Ukraine. Myronenko said that similar products from foreign manufacturers can be almost twice as expensive. This is because Metinvest has a vertically integrated production chain, shorter logistics to the front line and significantly lower labour costs in Ukraine.
While government departments are still preparing for official procurement, the Group is focused on supplying steel hideouts to the front line right now and free of charge.
One of the production managers said: “Many of our employees are currently serving in the south of the country. If even one of these structures protects their lives and they return home, I believe the Group will have fulfilled its mission.