Step by step towards upgrading the main steelmaking equipment. The BOF shop has completed the first stage of reconstructing the continuous casting machine No.1 ‒ upgrading key electrical equipment and the APCS.
CCM No.1 is the leading machine at the enterprise, which is used for producing merchant steel billets, including high-quality billets. Here, casting using stopper mechanisms has been mastered, and the specialist team systematically expands the product mix of CC billets in accordance with the requirements of demanding customers in both domestic and European markets.
To increase the operation reliability of the key equipment, a step-by-step reconstruction of CCM No.1 was launched this year. The first stage was completed in June, during which an investment project for replacing key electric equipment and automated process control systems was implemented.
In particular, seven new frequency converters were installed on each of the seven machine strands, ET-stations were replaced with modern ones, new S7-150 controllers were installed, and the upper level of the APCS, software, and control panels were updated. This enables the staff responsible for the casting process to obtain full information about the manufacturing process online and in real time.
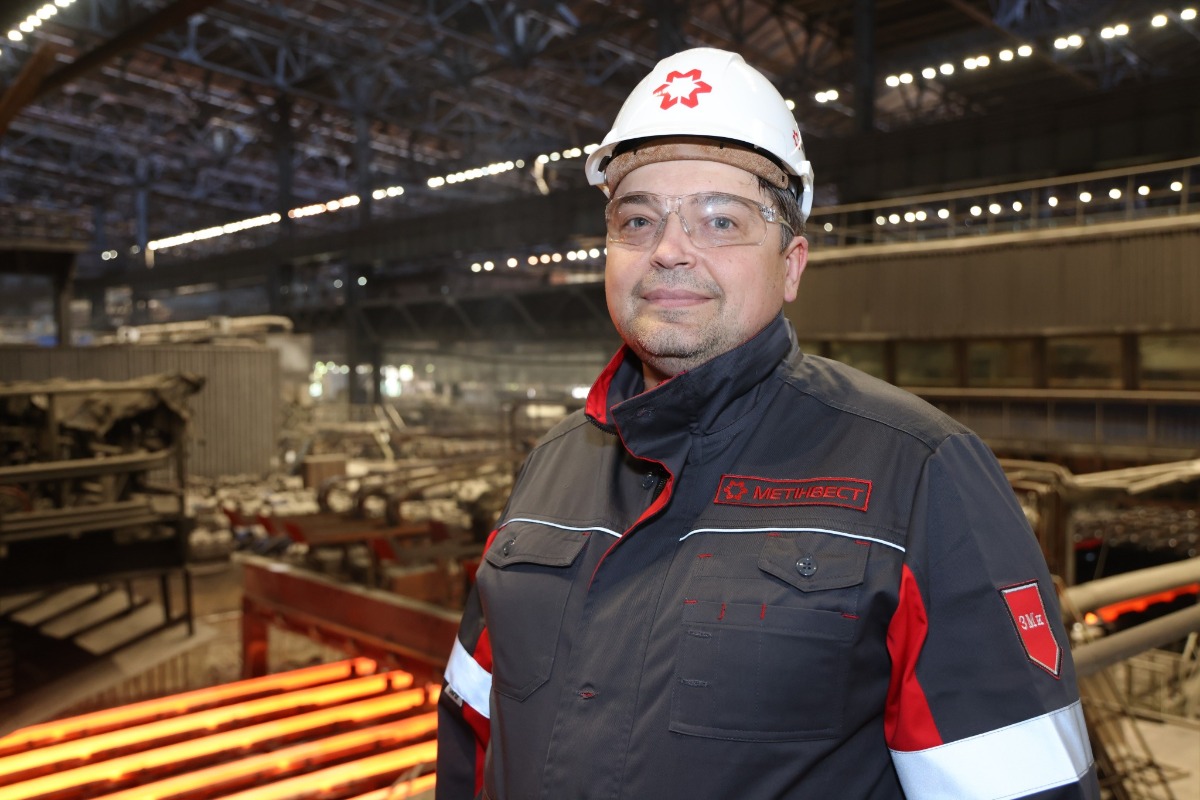
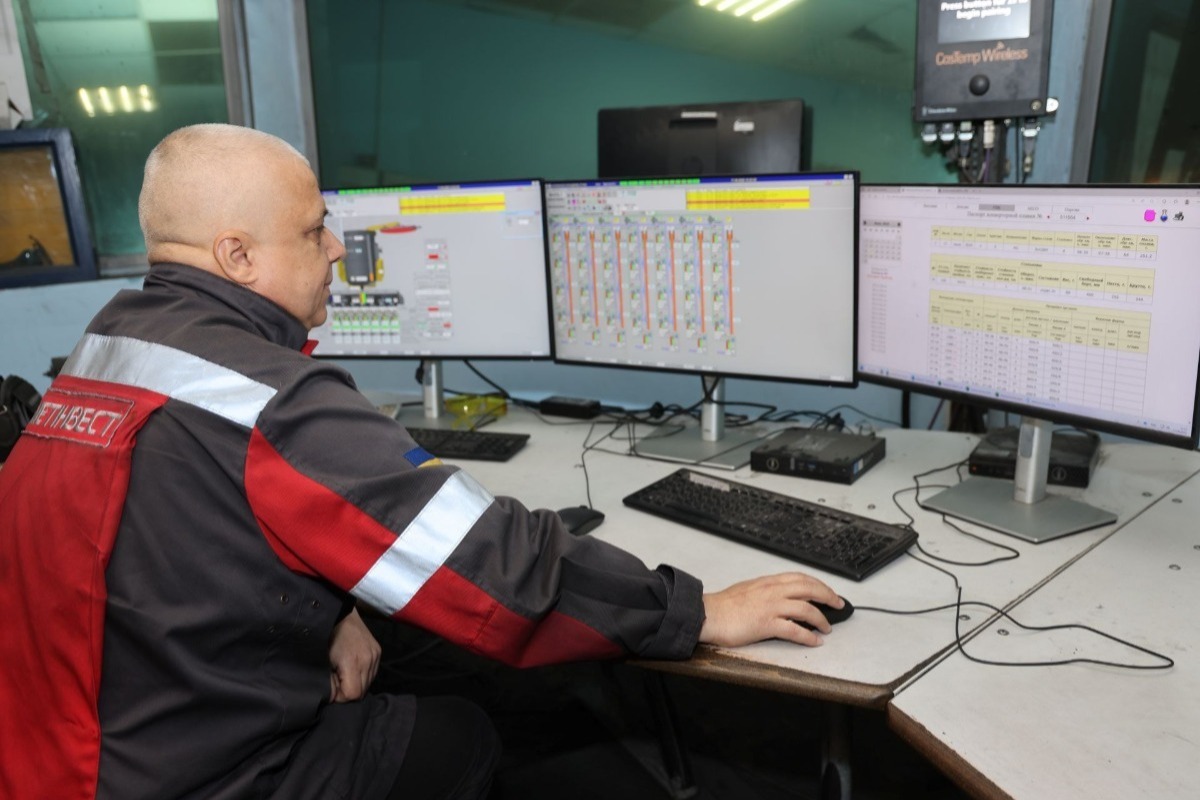
According to the production requirements, the investment project implementation was carried out gradually. The first two strands were "pilot," and subsequent works were performed taking into account the experience obtained, shutting down two to three strands at a time, which allowed for process optimisation.
Hot testing of CCM No.1 taking into account new equipment operation has already been completed. However, work under the supervision of Primetals Technologies, the partner company in implementing the investment project, is ongoing. All suggestions from the process staff focused on software improvement are being addressed in working mode. At the same time, the company is providing training for specialists in the electric service and APCS for effective operation of modern equipment.
Oleksandr DEHTIARENKO, Lead Reconstruction Engineer of the BOF Shop, said:
"We have the goal of upgrading the equipment of CCM No.1 in accordance with modern standards. However, working during wartime does not allow us to implement all our ambitious plans at once. With support from Metinvest Group, we are performing the step-by-step reconstruction of the first machine. Thanks to well-coordinated work by all subdivisions, the BOF shop's services, and specialists from the Capital Construction and Investment Directorate, we have successfully completed the objectives of the first stage.
Our efforts are directed, first and foremost, towards minimising downtimes related to malfunctions of outdated electric equipment. Modern software, with the capability to provide process information online, improves the capabilities of electric maintenance personnel through expanding the diagnostic scope, and partially enables enhanced CC billet cutting accuracy. This is one of the main tasks that we will perform at each stage of the CCM No.1 reconstruction".