In the gas shop of Kamet Steel, in cooperation with YASNO Energy Efficiency, a new single-stage supercharger was installed, the operation of which reduces energy consumption and reduces the operating costs of the plant in the process of injection of blast furnace gas at the gas booster station No. 6. Given this energy-efficient project, since the beginning of the year, electricity consumption during blast furnace gas injection has decreased by 60%.
The new gas blower, which plays a key role in the technological process of transporting blast furnace gas of required performance parameters and pressure for the needs of roller operators, has an average electricity consumption, taking into account the efficiency of the electric motor and control system, of 200 kWh. Performance and pressure control is ensured by the installed guide apparatus and a frequency converter with a voltage of 0.4 kV. Automation process control systems are designed individually based on the Siemens controller to operate in automatic mode in the specified performance range.
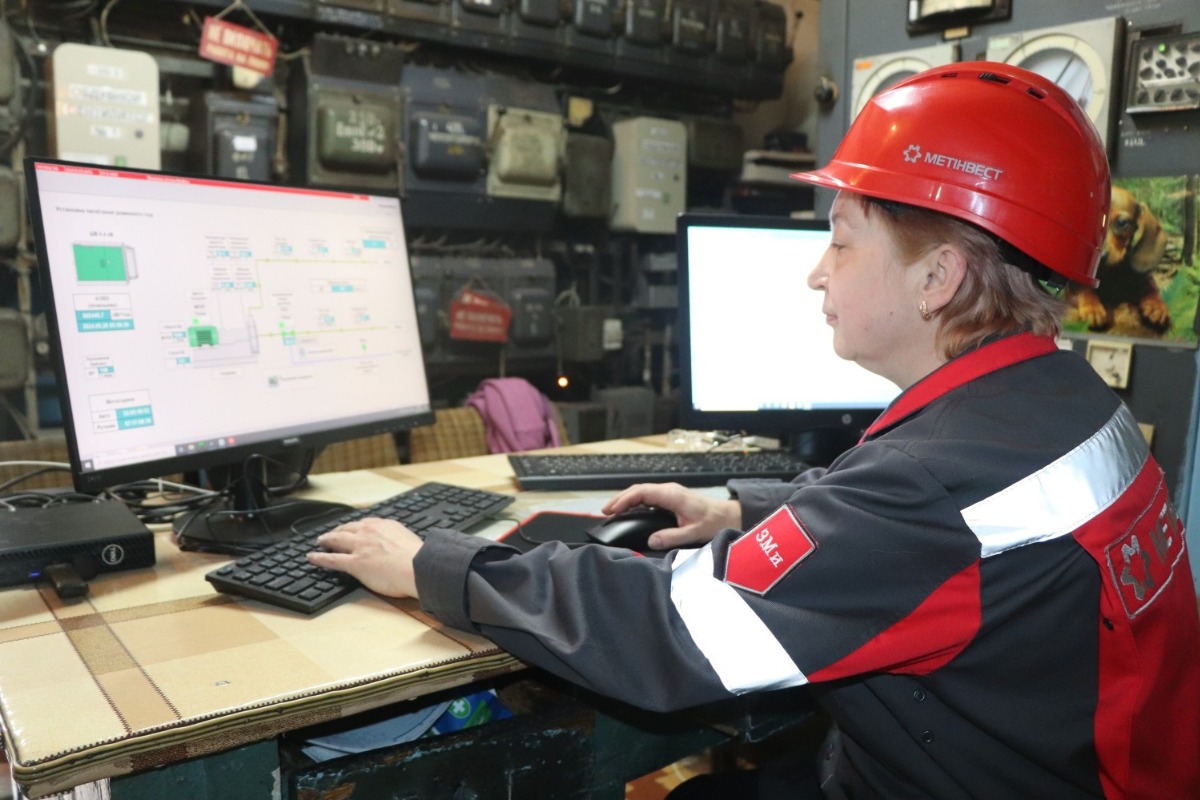
The hourly power consumption of the previous equipment averaged 650 kWh. With a nominal power of 850 kWh, it required manual adjustment of the required parameters, which also reduced the stability of maintaining the required performance parameters and pressure of blast furnace gas in the existing pipelines through which it is transported to the reheating furnaces of the tube billet mill.
A modern European-made supercharger is installed at an existing production site. Thanks to the optimal solutions implemented by the power engineers of the enterprise, the maximum amount of available process equipment was used. Along with the dismantling of the previous equipment, the contractors relocated existing communications, reconstructed electrical premises, and a new cable line was laid from the substation to the gas booster station No.6 (GBS-6) premises.
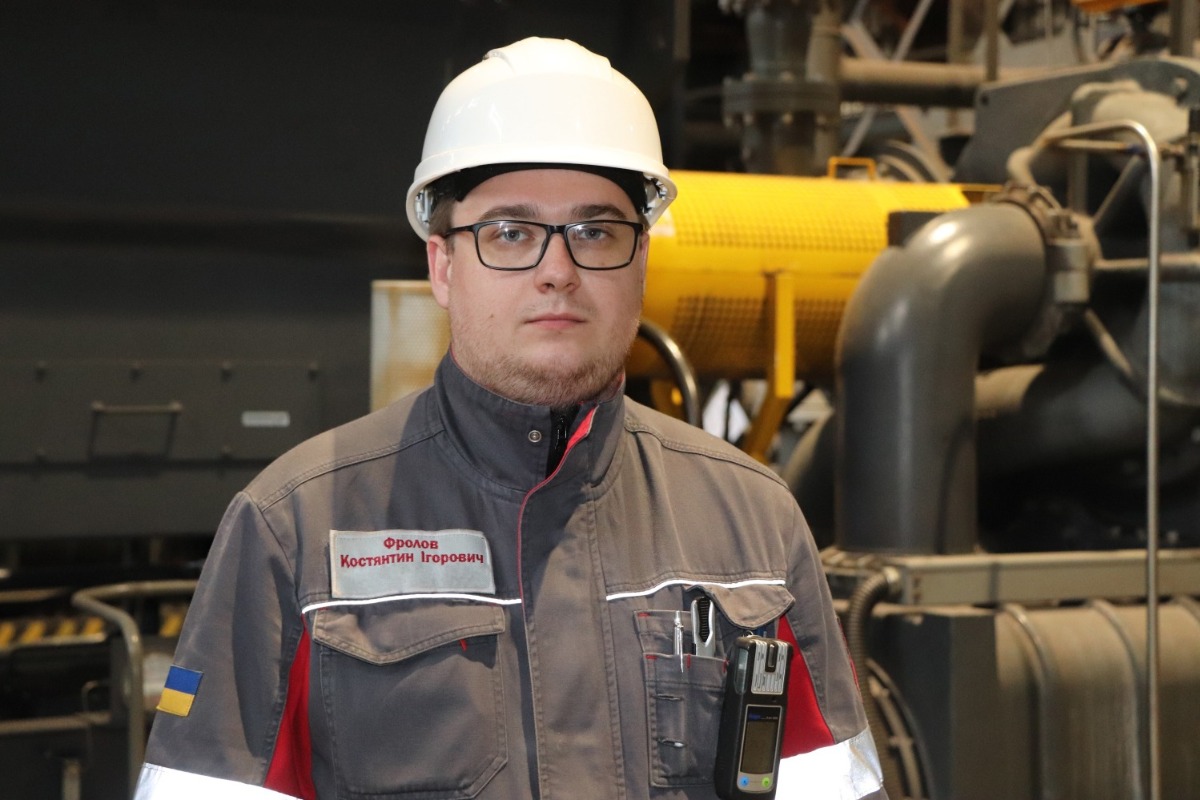
Konstiantyn Frolov
"This project was quite difficult to implement, as we were dealing with potential hazards associated with the use of blast furnace gas, which means that all specialists involved in the process had to pay increased attention to occupational health and safety issues. But thanks to the professionalism of our partners and colleagues from Kamet Steel, with whom we have already implemented more than one project, this time we have successfully achieved our goals and received significant savings indicators," said Yevhen TARASIUK, Director of YASNO Energy Efficiency.
"For four months of operation, the new equipment has confirmed its energy efficiency, namely, a reduction in specific electricity consumption for the transportation of blast furnace gas from 26 kWh/ths m3 up to 10 kWh/ths m3. Electricity consumption in the process of blast furnace gas injection at GBS-6 was reduced by 60%. We have also improved the reliability and stability of the blast furnace gas transportation process for the needs of rolling production. Modern process solutions in the energy saving system, which Kamet Steel systematically implements in cooperation with our reliable partners, are an integral part of the effective operation of the enterprise," said Konstiantyn FROLOV, Chief Power Engineer of Kamet Steel.