The Pelletising Plant of Metinvest's Central Iron Ore Enrichment Works has completed the major overhaul of the OK-324 induration machine.
The process equipment of the Pelletising Plant operates continuously, on a round-the-clock basis, for more than 7,500 hours per annum, so the increased level of attention to its technical condition is extremely important for miners. The specialists upgraded the equipment in 14 days. The repairs were carried out as part of the programme to optimise the pelletising process.
"One of the key areas was the restoration of refractory lining of the induration machine hearth and the repair of six prechambers. This step is crucial for maintaining the thermal insulation of the hearth space of the induration machine and will help avoid the destruction of the brickwork and ensure continuous operation of the plant between the overhauls," Andrii IVANOV, Deputy Head of the Pelletising Plant of Central GOK, said.
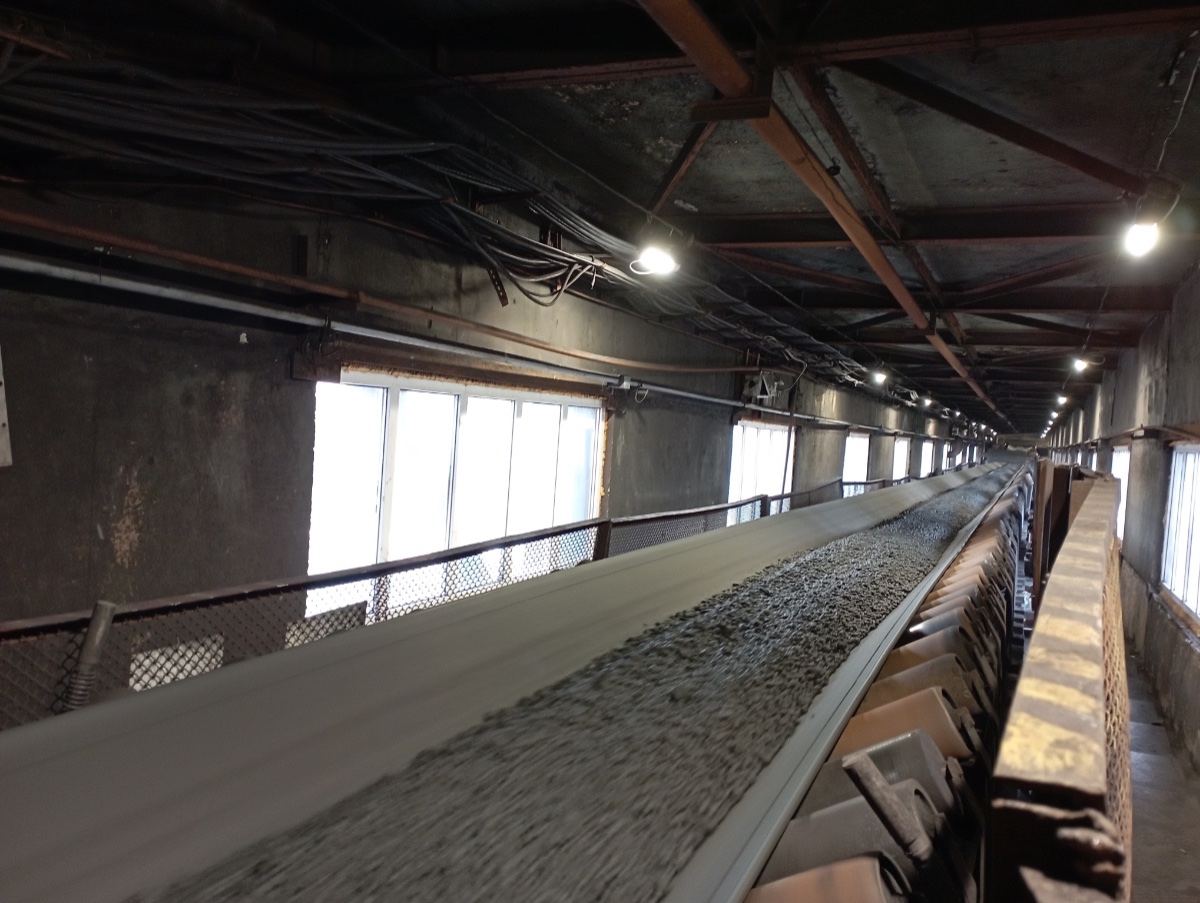
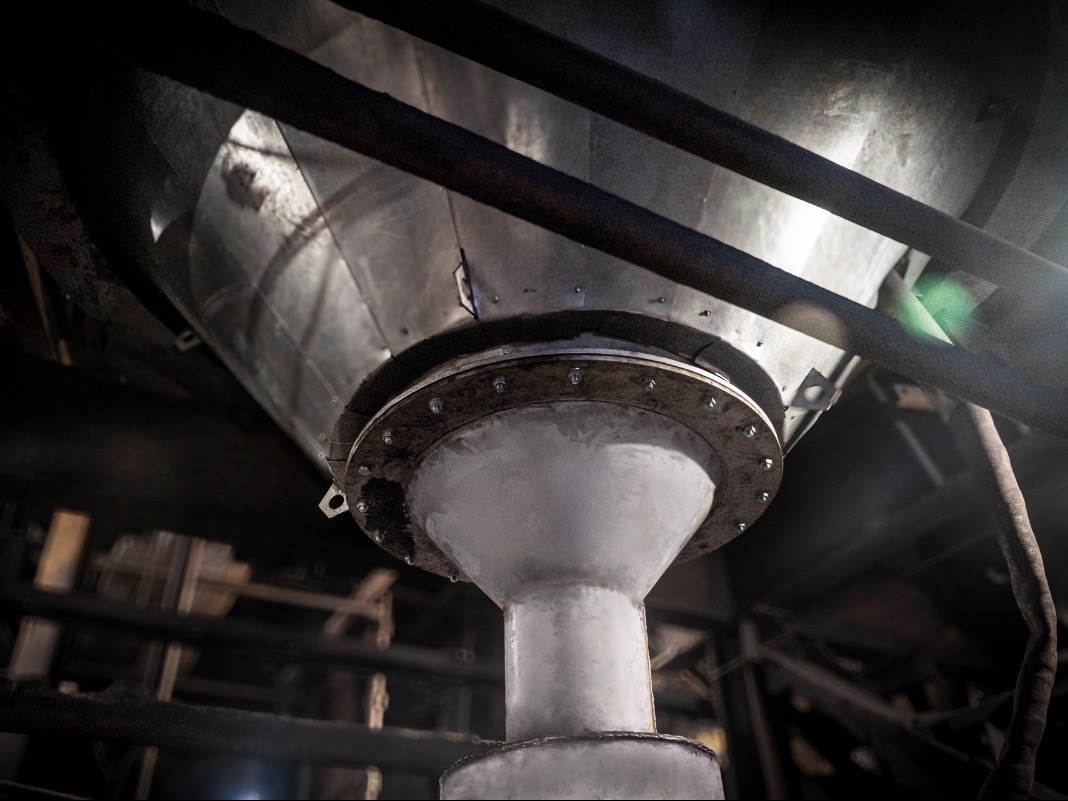
During the repair, an experimental solution was also implemented to apply gunned concrete to the surface of prechambers No. 9 and No. 10. This can significantly increase the durability of refractory insulation by reducing the impact of biofuels. Additionally, the specialists repaired the drip traps of smoke exhausters D2 and D5 and completely replaced three sections of the drip trap No. 2 of smoke exhauster D2. This will help to reduce emissions and improve the gas dynamics of the heat flow. A shaft-turning gear of the D3 smoke exhauster was also installed. This operational improvement will significantly reduce the equipment's operating time when the plant is shut down for scheduled maintenance. The mechanism will help to reduce energy consumption and improve equipment reliability.
As part of the major overhaul, the maintenance of the conveyor transport was also carried out, including the replacement of rollers, seals, and lining of the reloading units.
Following the overhaul and modernisation, all equipment systems were checked and adjusted for optimum performance.