During a three-week shutdown of the pelletising plant at Central Iron Ore, a series of major overhauls were carried out on the induration machine and the pelletising disc of Haver manufacture. Work included the partial replacement of smoke exhauster fans' droplet separators, the installation of new conveyor belts, and maintenance works on excavators were carried out. The total amount allocated to the fulfilment of works on the pelletising plant was nearly UAH 40,000,000.
From mid-May to the beginning of June, a scheduled repair period was in progress at Central Iron Ore. It lasted one week longer than usual, due to the speciality of the main works. In particular, it concerned the replacement of a set of rails on the induration machine's working branch and a set of longitudinal sealing.
"In order to free the working space for conducting repairs, we had to temporarily remove nearly 80 induration cars. It took quite a long time. Once that stage was completed, we carried out the dismantling of worn rails and sealing, and replaced them with new ones. The last time we performed such works was 8 years ago. We also managed to implement an initiative for installing an additional cleaning mechanism for the grate section on the induration machine, resulting in equipment efficiency improvement for firing pellets and saving natural gas and electricity," said Andrii IVANOV, Deputy Head for Engineering of the Ore Beneficiation Plant.
For the first time since commissioning, the pelletising disc of Haver manufacture was subject to a major overhaul. The key works carried out included the motor repair and replacement of the supporting unit. This critical work at the enterprise was entrusted to workers of the maintenance service shop. The team of specialists successfully completed the task. Currently, the pelletising disc operates at full capacity.
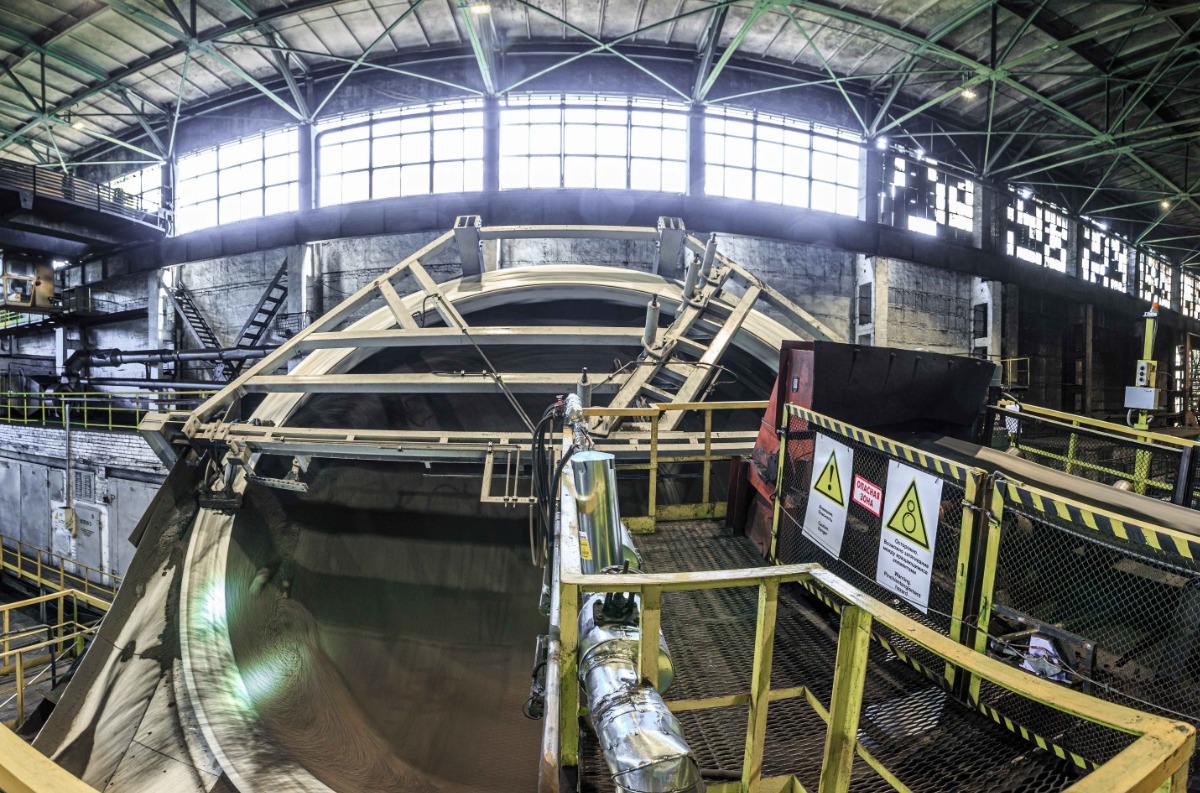
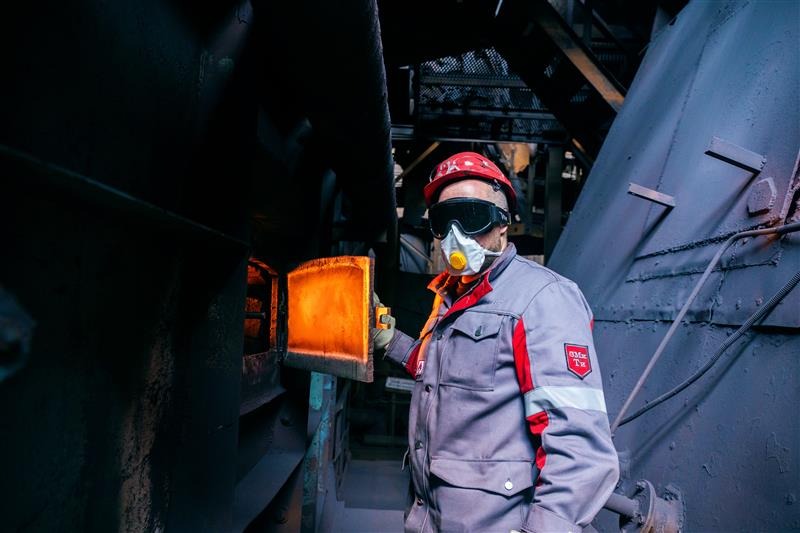
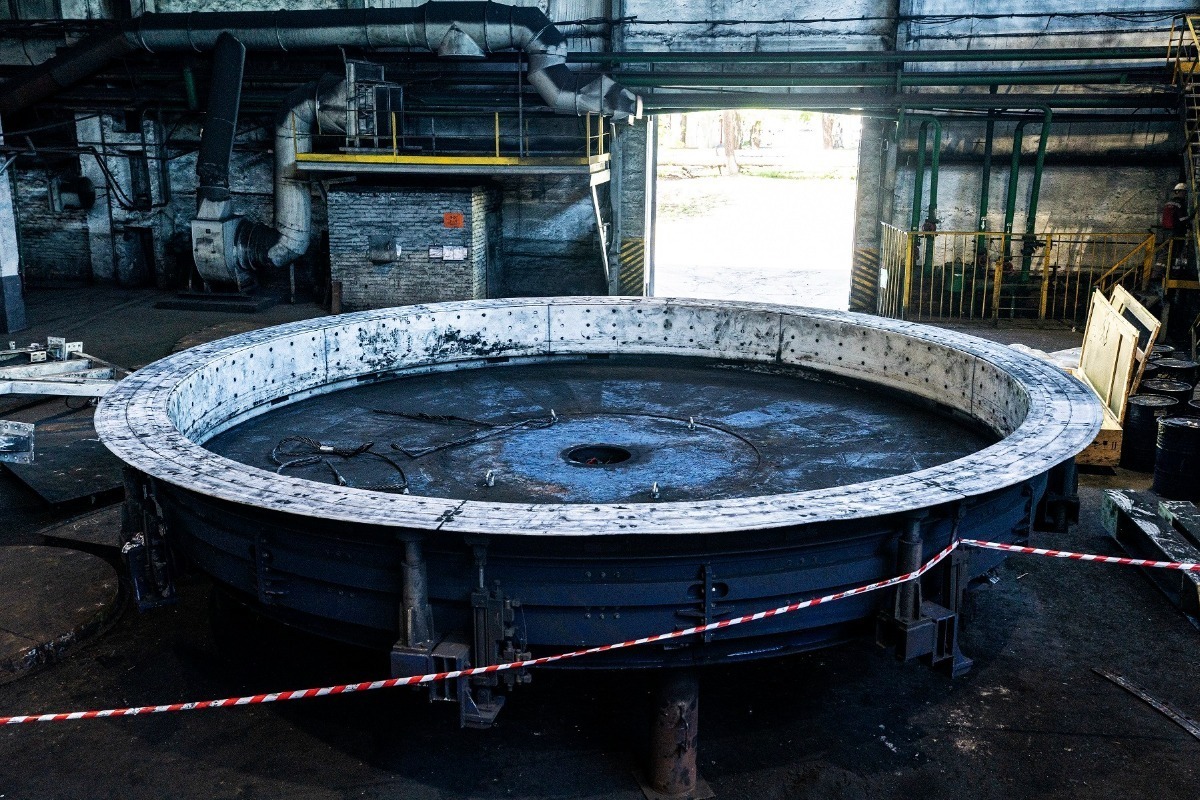
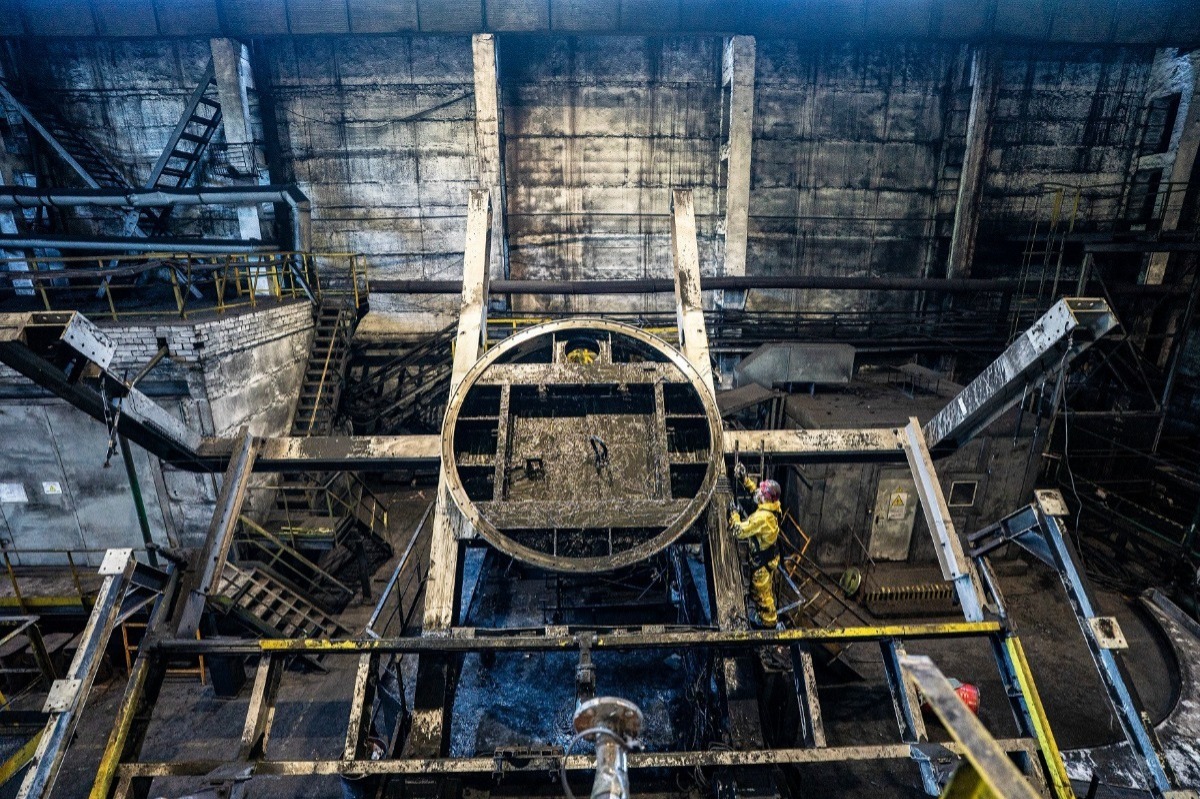
Simultaneously with these works, specialists carried out the partial replacement of two droplet separator sections of smoke exhauster No.2, which is directly responsible for the stable operation of the induration machine. According to Andrii Ivanov, the engineering team has been trying to find the most durable lining for droplet separators for several years. These devices operate under challenging conditions with an acidic medium, high temperature, and abrasive wear. This time, repair workers used ceramic tiles for the droplet separator No.1, which can withstand the aggressive impact of external factors. Specialists are expecting positive results during the operation of the new type of lining.
The conveyor network of the plant also underwent upgrading. Three conveyor belts were replaced during the shutdown. In order to ensure uninterrupted pellet shipment processes, maintenance was conducted on two 5-cubic metre excavators.
"Thanks to the quality repairs, the pelletising plant of Central Iron Ore now operates in normal mode. All subdivision units perform production tasks harmoniously and without interruptions. Currently, the plant production capacity has increased by 3 tonnes per hour due to implemented operational efficiency measures. Metinvest has allocated nearly UAH 40,000,000 for repair work and equipment upgrades," noted Andrii ZHYLKINSKYI, Head of the Pelletising Plant of Metinvest Central Iron Ore.