Сучасний світ неможливо собі уявити без сталі. Вона всюди. У мостах і хмарочосах, літаках і кораблях, у комп’ютерах і голках. Усього не перелічити. Цей матеріал дав нам нові можливості – підніматися вище, пересуватися швидше, жити цікавіше й комфортніше. А все тому, що сталь має особливі властивості. Міцна й водночас пластична. А ще її можна переробляти нескінченну кількість разів. Хто знає, сьогодні ви їдете автомобілем, а через декілька років він стане частиною космічного корабля.
Щодня, з ранку до вечора, ми користуємося предметами зі сталі. Давайте проведемо експеримент і порахуємо, скільки сталевих гаджетів нас оточує протягом дня? Подивіться на сторінку праворуч. У кого вийшло більше – у хлопців чи дівчат?
ТАЄМНИЦЯ ПОХОДЖЕННЯ ЗАЛІЗА
Сталь – це сплав заліза з вуглецем. Звідки взявся один із найпоширеніших у земній корі металів, досі загадка. Легенда свідчить: перше залізо впало з неба. На планету приземлилися гігантські метеорити, з яких давні люди навчилися робити вістря стріл і списів, щити й мечі, а також прикраси. Вважається, що першими підкорювачами металу були шумери (населення частини країн Близького Сходу) та єгиптяни в четвертому тисячолітті до нашої ери.
Майже три тисячі років знадобилося, щоб предмети із заліза увійшли в ужиток. На зміну кам’яному, мідному і бронзовому століттям прийшла епоха заліза. Річ у тому, що метеоритне залізо зустрічалося рідко, і вироби з нього цінувалися дорожче за золото. Та й майстри не поспішали ділитися своїми секретами. Прикрасами і зброєю «небесного» походження переважно володіла знать.
Перші згадки про спосіб виготовлення заліза – сиродутний процес – датуються другим тисячоліттям до нашої ери. Залізо, яке отримували з руди і деревного вугілля спочатку в закритих ямах, а потім у глиняних печах, нагадувало тісто. Щоб позбутися від шлаку, його багато разів проковували вручну сильними ударами молота.
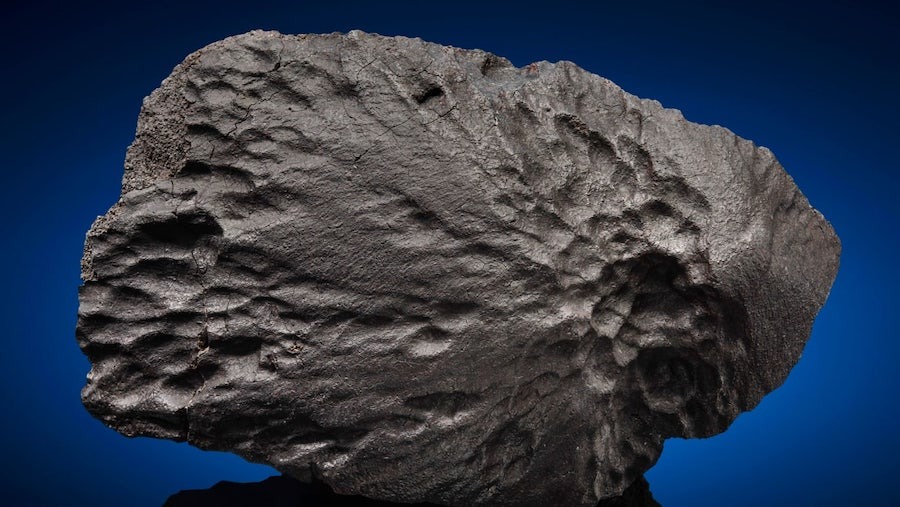
Залізний метеорит
Один із найбільших метеоритів світу впав у Приморському краї в горах Сіхоте-Алінь у лютому 1947 року. Його сліпучий слід спостерігали в Хабаровську та довкола у радіусі 400 км. Залізне тіло вагою 23 тонни розсипалося в атмосфері метеоритним дощем. Уламки утворили на поверхні Землі більше 30 кратерів від 7 до 28 м у діаметрі й до 6 метрів глибиною. Найбільший уламок метеорита Сіхоте-Алінь важить близько 1745 кг. Хімічний аналіз показав, що метеорит на 94% складається із заліза.
Чавун із залізної руди навчилися робити в пізньому середньовіччі, коли винайшли спеціальну піч – домну. Чавун (англ. iron) – це теж сплав заліза з вуглецем, але крихкіший у твердому стані. З нього роблять деталі для машин, пательні та ванни, а ще це напівфабрикат для виробництва сталі. У стародавні ж часи чавун через його ламкість спочатку вважали шкідливим продуктом. Але згодом помітили: якщо чавун ще раз переплавити в печі, він перетворюється на сталь хорошої якості. Цей принцип став популярним на багато століть і дійшов до наших днів.
Залізо швидко стало головним матеріалом у виробництві зброї та землеробських знарядь. Володіння чорним металом визначало результат боїв, хід історії і технічного прогресу. У 1864 році французький інженер П’єр Еміль Мартен винайшов піч, що переплавляла чавун і брухт на сталь. Цей винахід вперше в історії дозволив отримувати якісну рідку сталь. Мартенівський процес був основним способом виробництва сталі до сімдесятих років ХХ століття.
У наші часи мартенівських печей більше не будують, їх витіснили кисневі конвертери й електропечі.
СТАЛЬ У СВІТІ ТА УКРАЇНІ
Світове виробництво сталі стабільно зростає, в 2018 році воно досягнуло майже 1,8 млрд тонн. Майже половина цього обсягу виплавляється в Китаї. Найбільшими країнами-виробниками також є: Японія, Індія, США, Південна Корея, Німеччина, Туреччина, Бразилія, Італія, Тайвань і Україна.
Гірничо-металургійний комплекс України об’єднує підприємства чорної і кольорової металургії, гірничо-збагачувальні комбінати, феросплавні та коксохімічні заводи й підприємства, що випускають вироби з металів. Металургія – це чверть промисловості та валютної виручки країни, десята частина державного бюджету.
В Україні сформувалися три головних регіони чорної металургії: Донецький, Приазовський та Придніпровський. Там зосереджені запаси палива і залізних руд, там же виробляють залізорудну сировину й металопродукцію. До 2021 року Україна входила до ТОП-15 виробників сталі в світі.
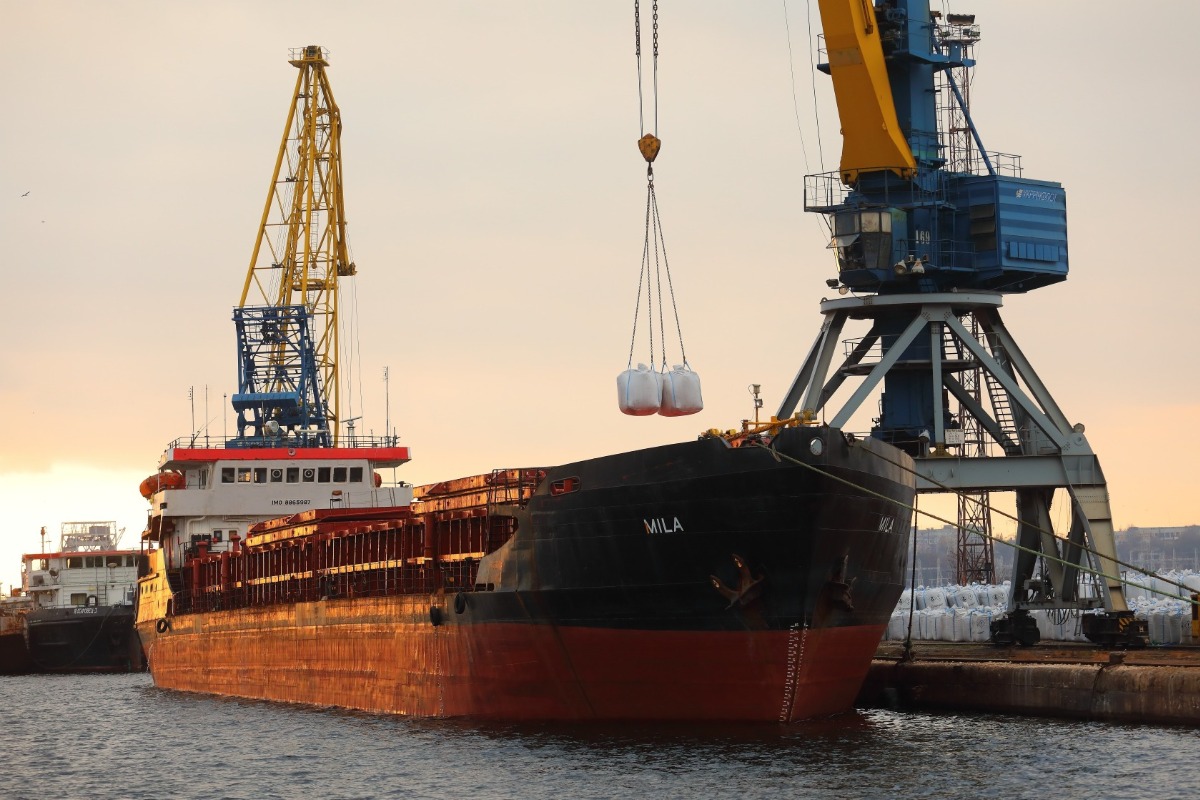
Йде вантаження прокату у річковому порті Запоріжжя
У нашій країні є кілька основних виробників сталі. Найбільший – Група Метінвест. Це вертикально інтегрований холдинг. Простіше кажучи, підприємства компанії випускають усі необхідні для виробництва сталевої продукції складові. На підприємствах в Україні видобувають вугілля, залізну руду, роблять кокс, випускають та роблять готову продукцію. Заводи Групи в Болгарії, Великій Британії та Італії виробляють лише готову продукцію із заготівок. Метінвест продає метал через власну збутову мережу в понад 100 країн світу.
22 млрд тонн сталі перероблено в світі з 1900 р. завдяки можливості 100%-го вторинного використання
Гірники й металурги завжди працюють у парі. Так влаштована гірничо-металургійна кухня. Порівняння із приготуванням їжі тут не випадкове. Адже людина не може обійтися без їжі, так само як світ – без сталі. Щоб розібратися в тонкощах приготування цієї страви, ми обстежимо всі полиці кухні металурга та гірника й розберемо кожен інгредієнт. Ви готові стати шеф-кухарем? Тоді вперед!
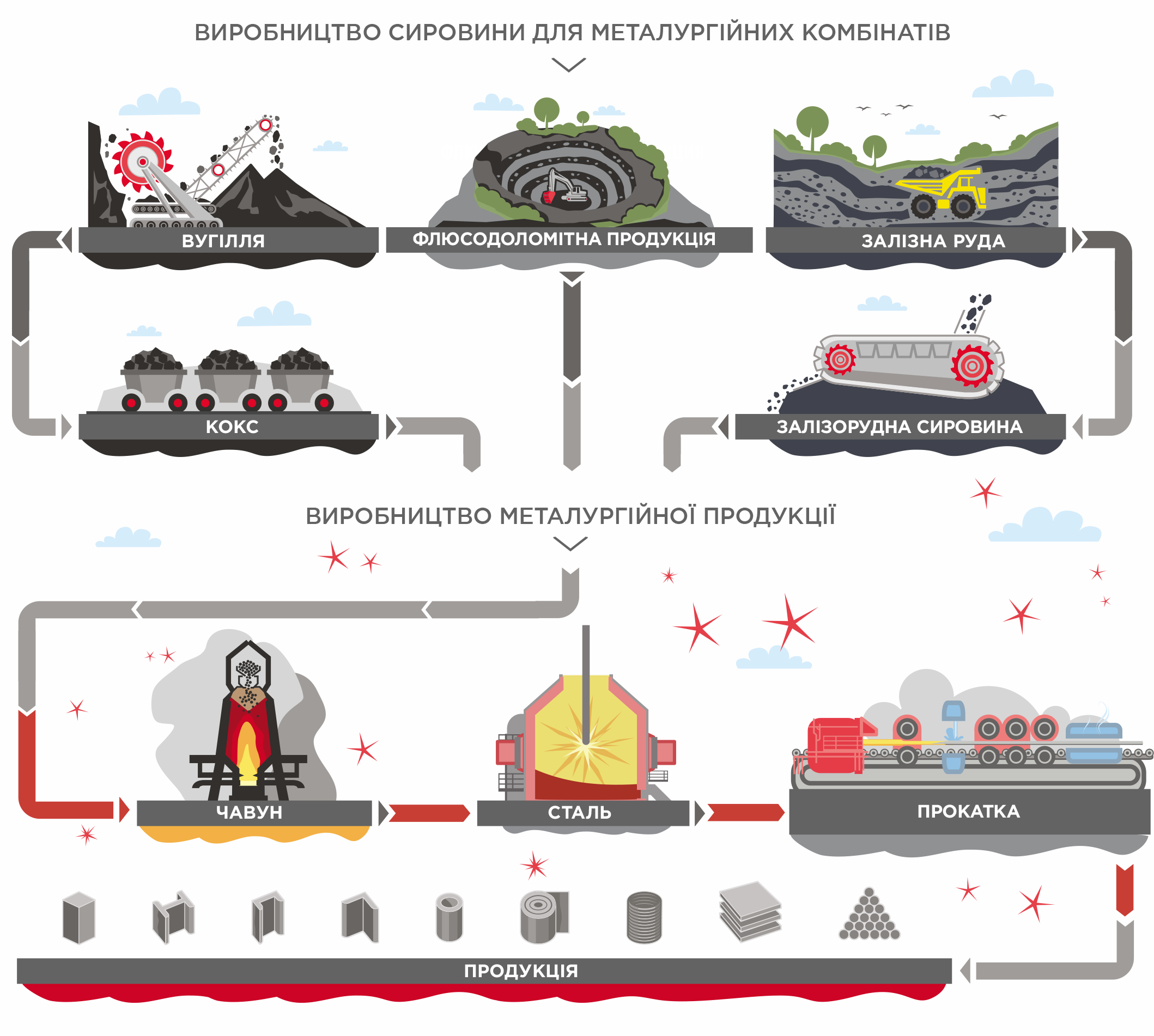
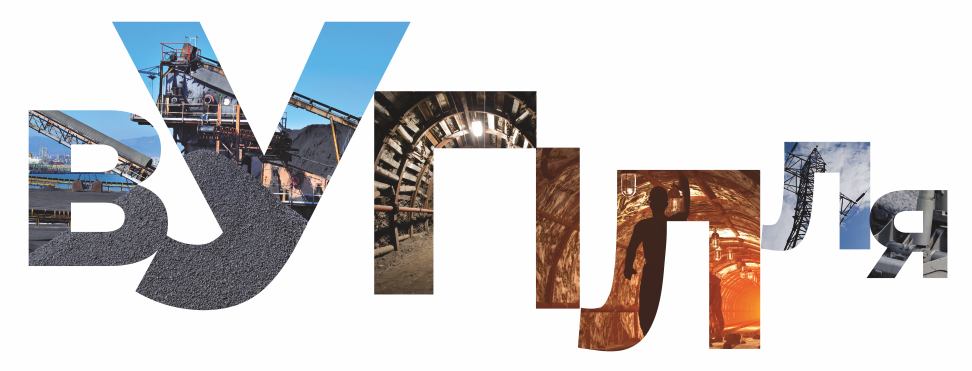
Виробництво металу – технологічно складний і довгий процес. І остаточний результат тут залежить від багатьох чинників. Важливе значення має підготовка сировини. Для приготування смачних страв – чавуну і сталі, як і на звичайній кухні, потрібні продукти екстра-класу. Один із них – коксівне вугілля. Спочатку його добувають, а потім роблять кокс, який стає паливом і хімічним реагентом для виробництва чавуну.
Існує чимало різновидів (марок) вугілля. Вони відрізняються своїми властивостями і галузями застосування. У металургії використовують кам’яне вугілля коксівних марок Ж (жирні), К (коксові), Г (газові) тощо. Воно відрізняється особливою енергоємністю, здатне ставати пластичним, а в особливих умовах – спікатися. Для опалення житла таке паливо непридатне, але для виробництва доменного коксу підходить ідеально.
до 7хвилин триває спуск шахтарів в українських шахтах
ВИДОБУТОК
Для видобутку вугілля потрібна фізична сила. Хто хоч раз тримав лопату в руках, знає, як нелегко накопати відро картоплі, що вже казати про вугілля. Згодом на допомогу людині прийшли потужні комбайни, проте праця шахтаря, як і раніше, вважається однією з найважчих.
Існує два види видобутку кам’яного вугілля – відкритим і закритим способом. Відкритий застосовується на неглибокому заляганні вугільного пласта – до 100 м. В Україні глибина шахт сягає понад 1 500 м. У таких випадках вдаються до підземного, закритого способу. Розробка ведеться лавами – у довгих підземних тунелях.
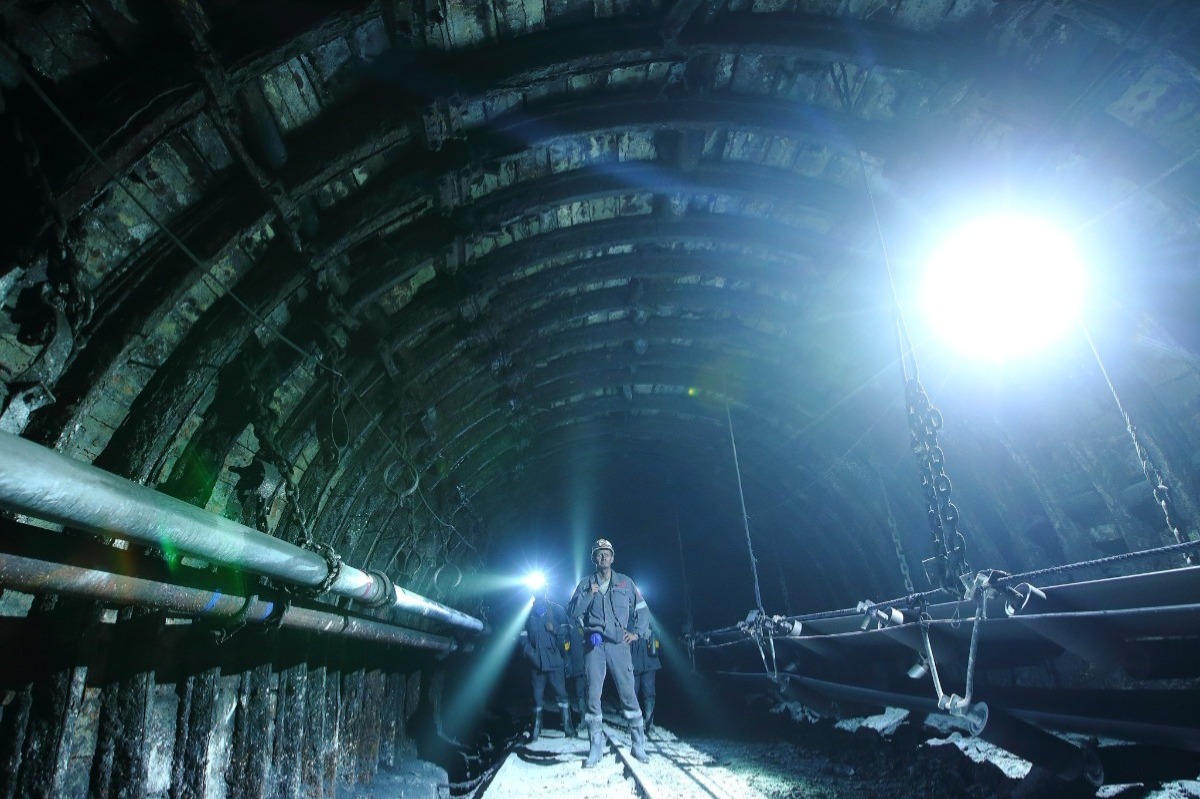
Основні технологічні процеси видобутку – це виймання вугілля в очисному вибої (головному місці робіт), переміщення лавою, навантаження сировини на транспортний засіб. Для безпеки праці вибій провітрюється та очищається від газів, що виділяються з вугільних пластів. Під час робіт уважно стежать за гірничим тиском. Щоб порожнечі, які утворилися після видобутку вугілля, не обвалилися, споруджують кріплення – спеціальні підпори.
1546 м – найглибша вугільна шахта у світі, розташована в Україні
Виймання вугілля складається з відбивання і навантаження корисних копалин. Вугілля рубають за допомогою комбайна, який так і називається – виїмковий. Гірничу масу вантажать на скребковий конвеєр, перевозять шахтою і скіпами (сталевими коробами) піднімають на поверхню.
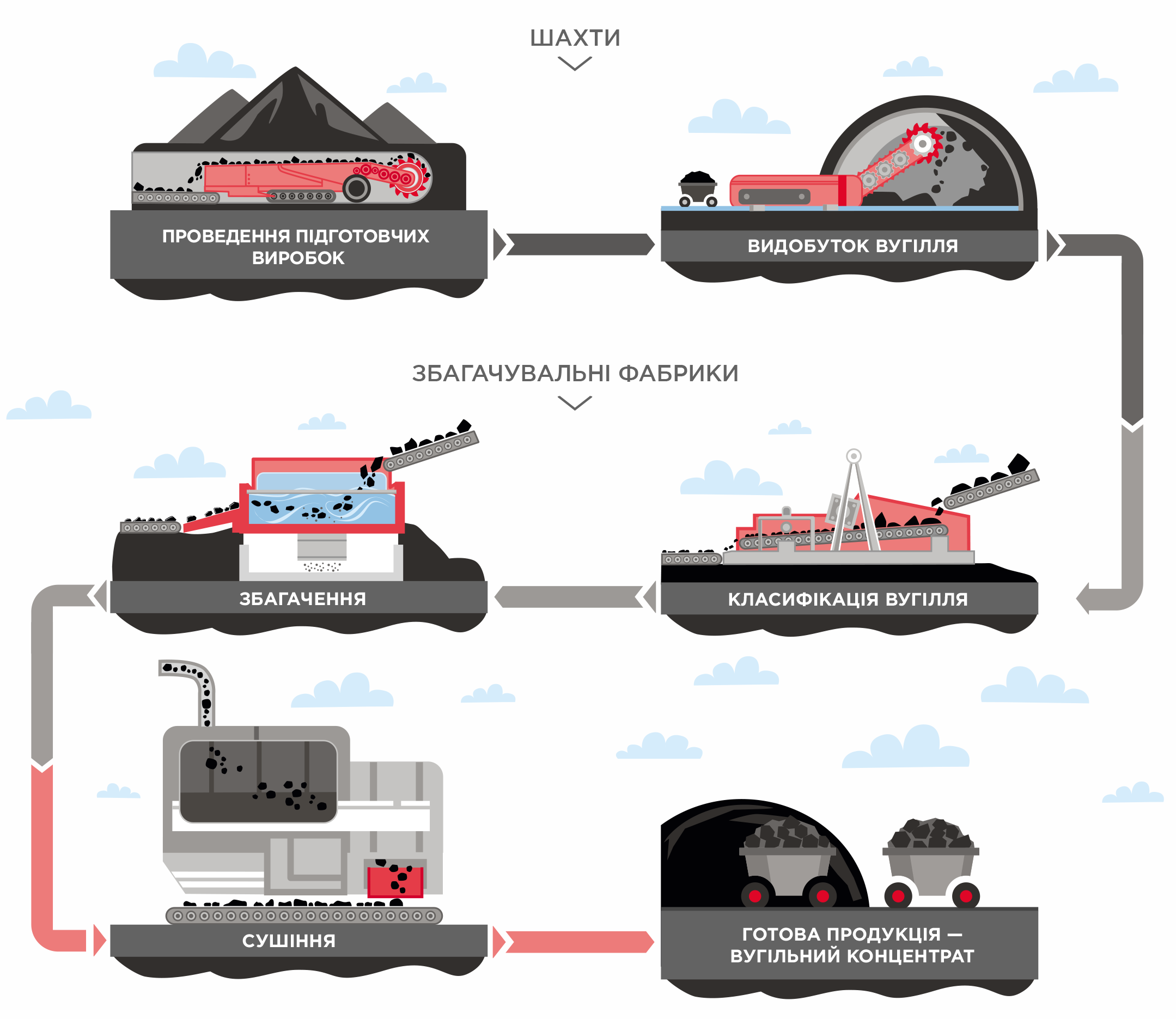
ЗБАГАЧЕННЯ ВУГІЛЛЯ
Видобуте кам’яне вугілля містить чимало домішок. Вони знижують якість сировини і при горінні дають низьку температуру. Щоб позбавити вугілля зайвого, його збагачують – очищають. Під час цього процесу зменшується вміст мінеральних компонентів. Водночас вугілля поділяють на сорти за розмірами зерен.
Перший етап – грохочення або сортування за розмірами. Відбувається воно за допомогою віброгрохота: кам’яне вугілля надходить на сита з різними отворами і ділиться на групи. Сита видають характерний звук, за який агрегат і отримав свою назву.
Другий етап – це збагачення. Найпоширеніший варіант – мокре збагачення (флотація, від французького flotter – плавати). Щільність вугілля і домішок є різною. У водному середовищі вони відокремлюються одне від одного. Відбувається це в агрегатах гравітаційного збагачення – у так званих відсаджувальних машинах. Вугілля подається на сито, через яке поступово піднімається вода. Важка порода спадає донизу, а легке вугілля піднімається догори. Домішки транспортують у відвал, а концентрат, тобто вже збагачене вугілля, відправляють на коксохімічний завод.
До мокрого збагачення також належить пінна флотація. Під час цього процесу вугілля, оброблене реагентом, спливає разом із повітряними частинками на поверхню ємності. Завершує мокре збагачення зневоднення вугільного концентрату. Він проходить через фільтр і висушується.
До речі, раз є мокре, то має бути і сухе збагачення. Для цього використовують циклони, які працюють за рахунок відцентрової сили. При обертанні агрегату з великою швидкістю вугілля збирається у верхній частині циклона, а відходи – в нижній.
Вугільний концентрат – незамінний продукт найвищої якості – вирушає на коксохімічний завод. Отже, ми вже можемо «приготувати» перші страви на нашій металургійній кухні. Хочете шматок пирога? Тільки не простого, а коксового?!
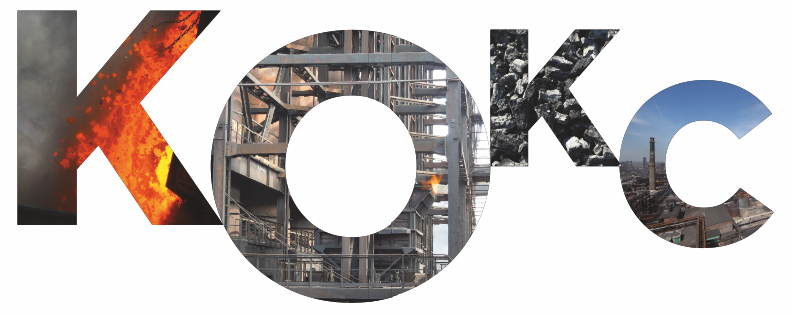
Ми видобули вугілля, збагатили його та отримали концентрат. Тепер піднімаємось із глибин шахти та вирушаємо на коксохімічне виробництво. Тут буде спекотно!
Для приготування доменного коксу нам знадобиться коксівне вугілля і коксова піч. Найчастіше використовують декілька видів вугілля. Спеціально приготовану суміш вугілля називають шихтою.
У металургії кокс (від нім. koks і англ. coke) – твердий пористий продукт сірого кольору. Його отримують під час нагрівання кам’яного вугілля до 1000 °С без доступу повітря. Цей процес називається коксуванням.
Кокс – це високоякісне бездимне паливо для виробництва чавуну в доменній печі. Там його використовують не лише для розплавлення шихти, а й для відновлення заліза з руди.
Застосування коксу дуже різноманітне: у ливарному виробництві, хімічній і феросплавній промисловості та навіть для опалення будинків.
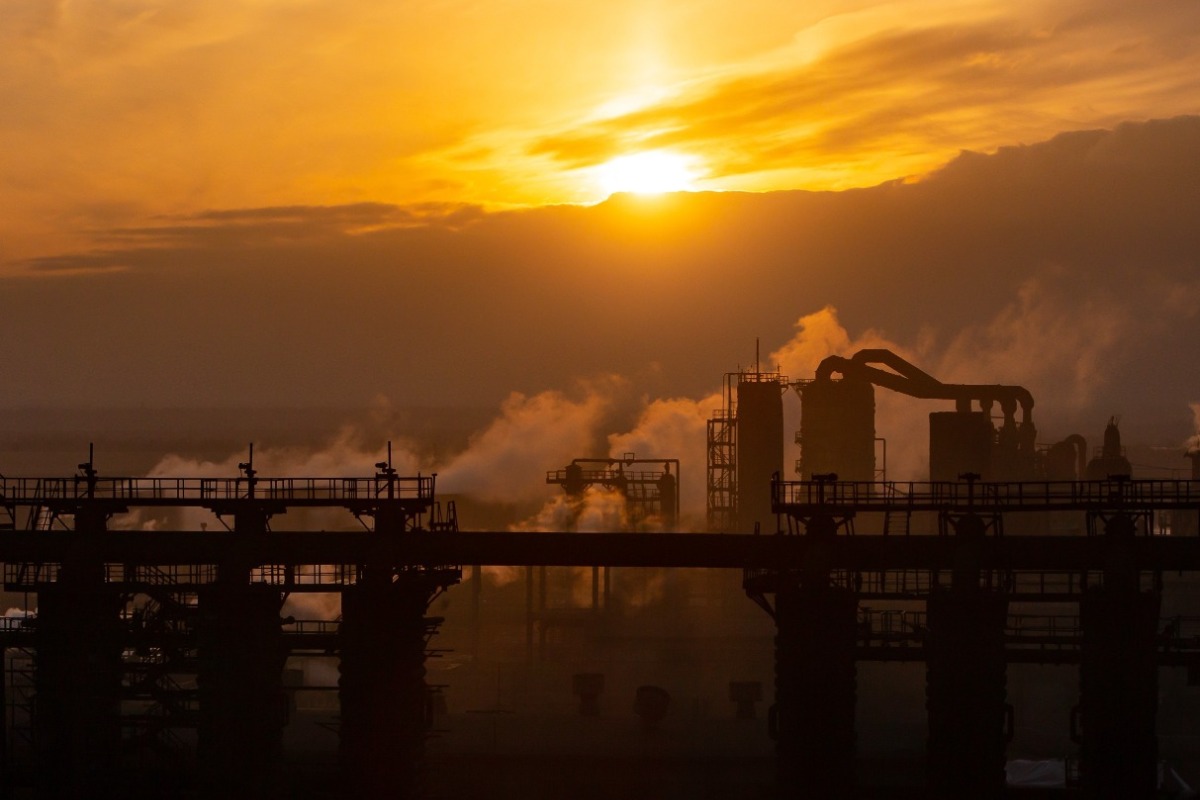
ПІДГОТОВКА
Отже, у нас є необхідні інгредієнти, щоб почати готувати пиріг. Коксовий пиріг – саме так називається продукт, який отримують із коксової печі.
Після видобутку і переробки на концентрат коксівне вугілля прямує на коксохімічні заводи для виробництва коксу. Перший етап приготування нашого пирога – подрібнення вугілля для отримання борошна, а точніше – вуглепідготовка. Борошно має бути вищого ґатунку і дуже дрібного помелу. Кожна крупинка домішок значно знижує якість коксу, порушує його однорідність і сприяє розвитку тріщин, які погіршать перебіг хімічних реакцій при виробництві чавуну.
IVстоліття н. е. – в Китаї уперше описали процес виробництва коксу
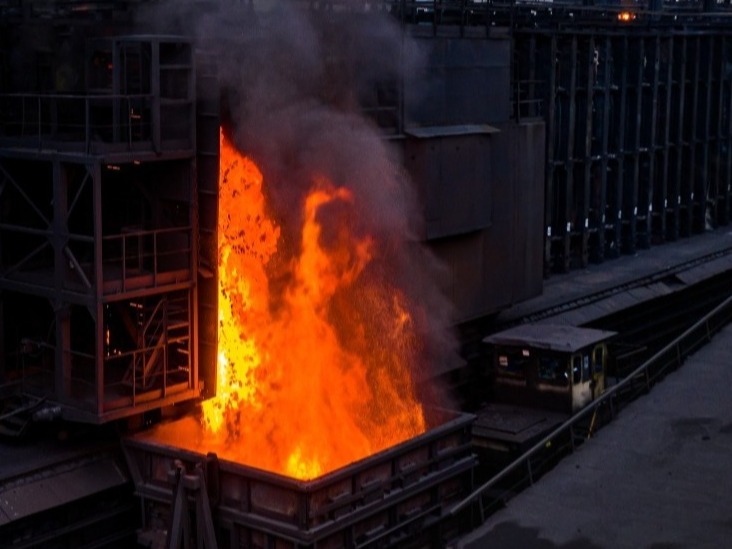
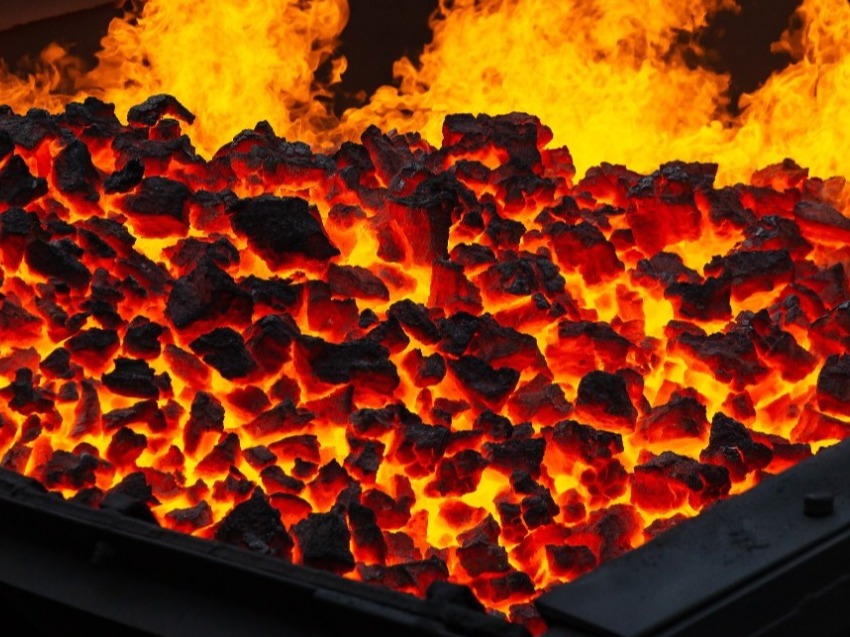
КОКСУВАННЯ
Коксовий пиріг готують у спеціальних духовках – коксових печах, з яких складаються коксові батареї. В одній батареї може бути від 45 до 70 печей.
Усе, як удома на кухні, відмінність лише в розмірах духовок і температурі приготування. Коксова піч являє собою горизонтальні прямокутні камери, що обігріваються через бічні стіни. Вугілля завантажується зверху. Перетворення відбувається без доступу повітря і за температури понад 1000 °С. Зазвичай тісто складається не лише з борошна. Так і кокс здебільшого отримують не з одного виду вугілля, а з шихти. Як і класичний пиріг, коксовий починають готувати із зовнішніх країв до середини. Коксування триває 14–16 годин і поділяється на кілька стадій – залежно від температури нагріву.
Перша – стадія сушіння. Вугілля нагрівається до 200 °С, і з нього випаровується волога. При подальшому нагріванні до 350 °С (друга стадія) вугілля починає «пом’якшуватися». На його зернах утворюється плівка з бітумів – залишкових смолоподібних продуктів переробки вугілля. На третій стадії за температури до 500 °С вугілля стає пластичним. Досягнувши температури 600 °С, пиріг лише починає «запікатися», утворюється напівкокс. А за температури 1050 °С процес утворення твердого коксу завершується.
Кожна стадія випікання коксу супроводжується складними хімічними процесами. При спіканні коксу утворюється цінний побічний продукт – коксовий газ. При його очищенні отримують смолу, аміак, сірчану кислоту, бензол, феноляти та легкі піридинові основи. І якщо формули цих речовин знає далеко не кожен, то з похідними продуктами стикалися всі. З цих речовин роблять добрива, лаки, фарби для холодильників і автомобілів, нафталін, дьоготь для будівництва доріг і багато іншого.
Розжарений коксовий пиріг стає розсипчастим. Його видають за допомогою дверезнімальної машини і коксовиштовхувача у спеціальний вагон. Щоби кокс не горів поза піччю, його гасять. Є два методи охолодження: мокрий спосіб, при якому кокс зрошується водою, і сухий, коли температура знижується за допомогою обдування циркуляційним газом.
Потім кокс просівають і сортують за розмірами шматочків. Найбільший називається доменним коксом, середній – коксовим горішком, а решта – коксовим дрібняком. Великий прямує в доменну піч на виплавку чавуну, середній використовується як паливо у феросплавній промисловості, а дрібний відправляють на виробництво агломерату.
Кокс – готовий продукт для виплавки чавуну. Ще один необхідний інгредієнт – це руда. А за нею ми вирушаємо до кар’єру.
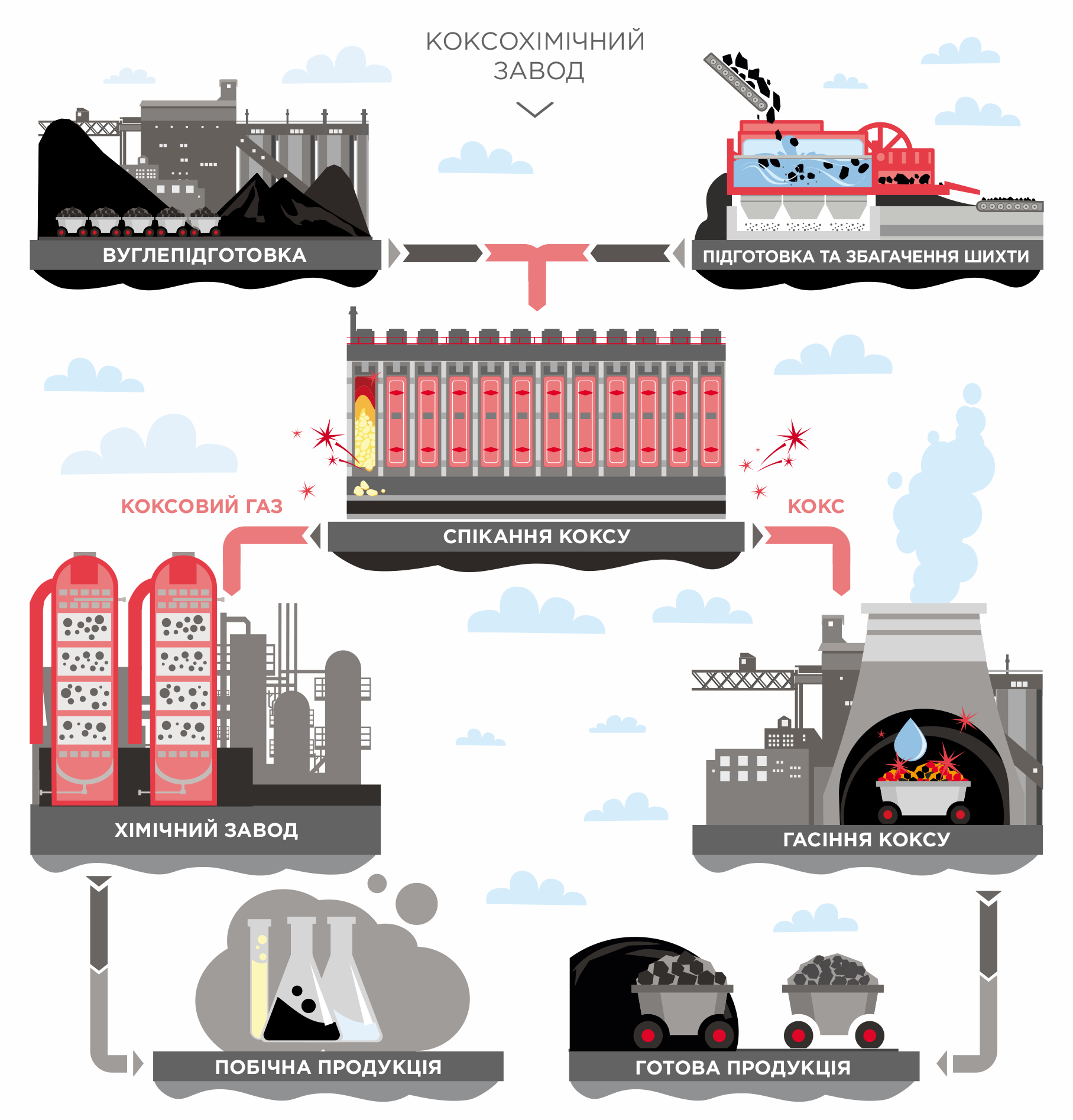
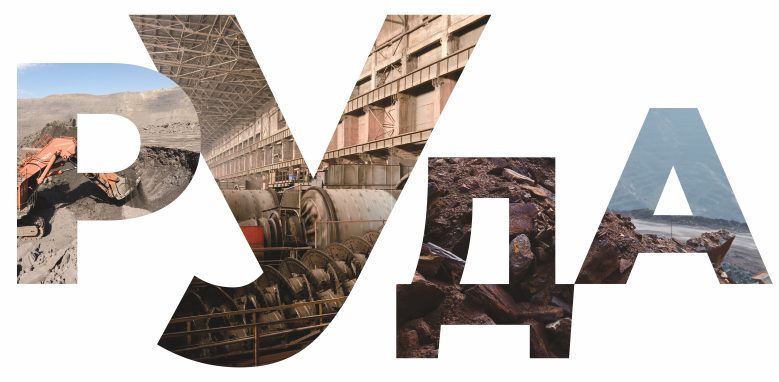
Уявіть собі, що ви стоїте на краю залізорудного кар’єру. Його масштаб і глибина вражають. Величезні самоскиди, які рухаються серпантином доріг, здаються іграшковими. Важко повірити, що все це зроблено руками людини.
Кар’єри нагадують гігантські кратери з барвистими відвалами-горами і глибокими вирвами. Найбільший у світі рудник – Бінгем Каньйон у США, глибиною 1,2 км і діаметром понад 4 км, займає площу 7,7 км2. На цій території цілком могло би розташуватися місто або навіть невелика держава.
В Україні найбільше залізних рудників зосереджено у Кривому Розі.
У світі – близько 170 млрд тонн розвіданих запасів залізної руди. Україна входить до десятки країн, що мають найбільші поклади заліза у світі. Наші родовища містять 6,5 млрд тонн руди.
Залізна руда – основна сировина у виробництві сталі. Гірничу масу збагачують і отримують залізорудну сировину – концентрат, з якого роблять окатиші та агломерат. Без них неможливо виплавити чавун. Залізорудна сировина – це основна частина повноцінного і збалансованого «харчування» для доменної печі. Руда, як і кокс, входить до складу шихти, яка згодом перетворюється на чистий, «дієтичний» метал.
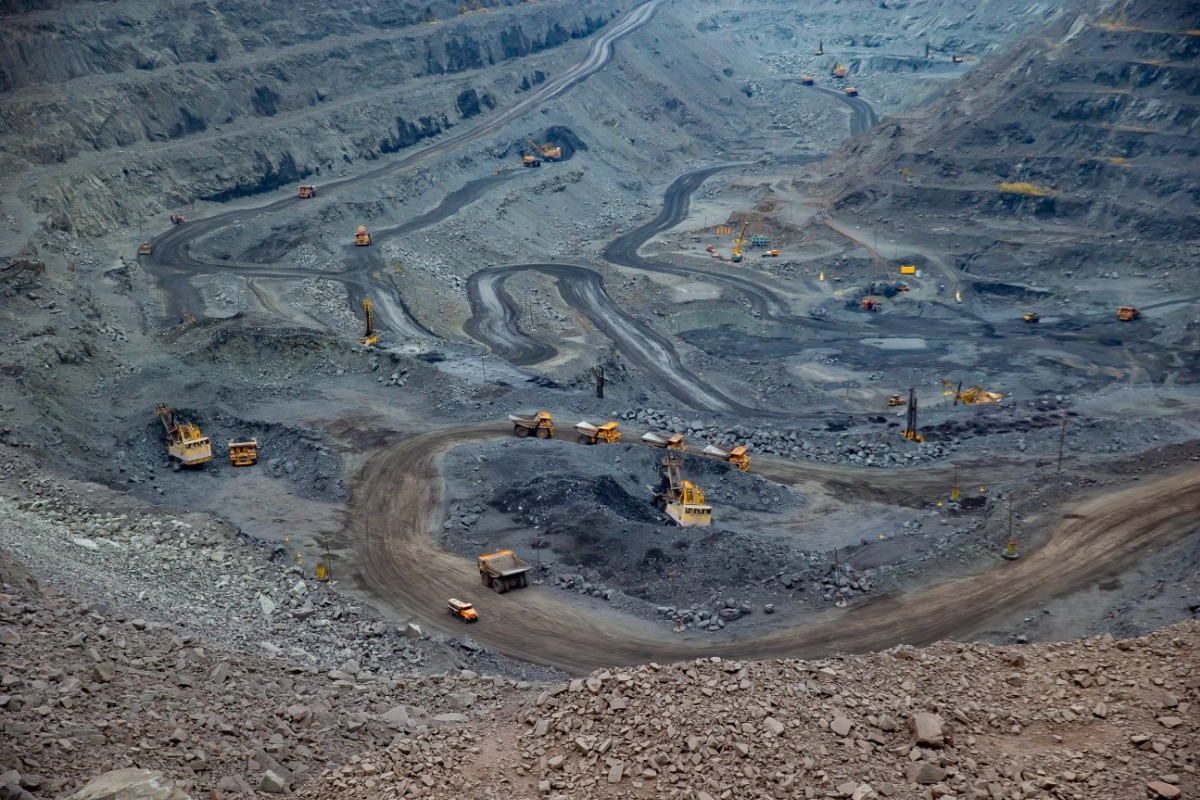
Інгулецький кар’єр на Криворіжжі
ВИДОБУТОК І ПІДГОТОВКА РУДИ
Залізну руду, як і вугілля, можна добувати закритим і відкритим способом. Якщо руда залягає близько до поверхні, а пласт товстий, застосовують відкритий спосіб видобутку – в кар’єрах. При глибокому заляганні та малій товщині пласта використовують закритий спосіб – у шахтах. Закритий спосіб подібний до видобутку вугілля.
Відкритий спосіб можна розділити на два етапи. Перший – це розкривні роботи. Щоб дістатися до корисних копалин, землю, пісок і камінь знімають та вивозять у відвал (насип порожніх гірських порід). Другий – власне видобуток. Щоб роздробити тверді рудні пласти, їх підривають. Для цього застосовують декілька сотень тонн вибухівки. До речі, на гірничо-збагачувальних комбінатах Метінвесту використовують екологічно безпечну безтротилову вибухівку: так у повітря здіймається мінімум пилу і газів. Потім настає черга спецтехніки – бульдозерів, екскаваторів і самоскидів.
Розколота вибухами гірнича маса неоднорідна за формою і складом. Від розмірів шматків породи залежить спосіб її подальшої переробки. Залізна руда проходить дроблення та подрібнення, а також сортування – грохочення і класифікацію.
Чим дрібніша руда, тим краще вона відділятиметься від порожньої породи і різних домішок. Тоді очищена від усього зайвого руда перетвориться на залізорудний концентрат, придатний для подальшої переробки та виплавки чавуну.
За вмістом заліза руда поділяється на багату (не менше 57%) і бідну (мінімум 26%). Щоб збільшити концентрацію заліза, руду збагачують. Це додає ефективності роботі доменної печі, зменшує вихід шлаку і знижує витрати коксу під час виплавки чавуну. Щоб збагатити руду, використовують магнітну сепарацію і флотацію.
ЗБАГАЧЕННЯ
У промисловості найчастіше застосовують перший метод: подрібнену руду пропускають через магнітне поле. Пам’ятаєте свої досліди з магнітами в дитинстві: як магнітна підкова притягувала усілякі залізяки? Так працює і цей метод. Магнітний сепаратор складається з постійного магніту і барабана. Руда з водою подається на зовнішню поверхню барабана, який обертається. Частинки заліза притягуються до поверхні барабана, їх можуть змити лише поза магнітним полем. Так виготовляється концентрат.
При флотації подрібнену руду обробляють у флотаційній машині: продувають повітря через пульпу (суміш руди й рідини) за присутності крохмалю, соди, соснового масла й інших флотаційних реагентів. Частинки заліза залишаються у камері флотаційної машини, а порожня порода збирається в піні.
Волога робить процес подальшого металургійного виробництва більш енергоємним, тому після збагачення концентрат зневоднюють. Для цього застосовують вакуум-фільтри. Мокрий концентрат фільтрують за допомогою дисків, обтягнутих із двох сторін спеціальною тканиною, осад висушують під дією вакууму, а рідину видаляють. Після зневоднення отримують готовий до відвантаження споживачеві залізорудний концентрат, який нагадує чорний і трохи вологий пісок.
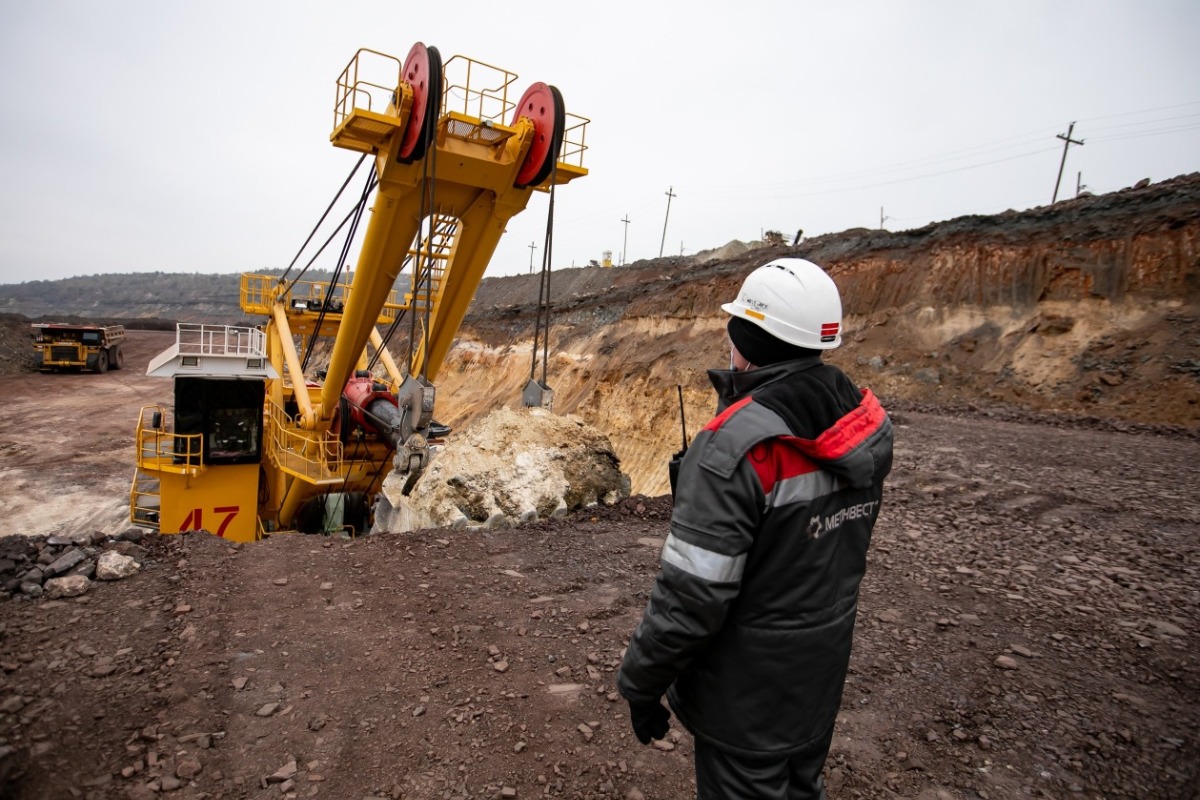
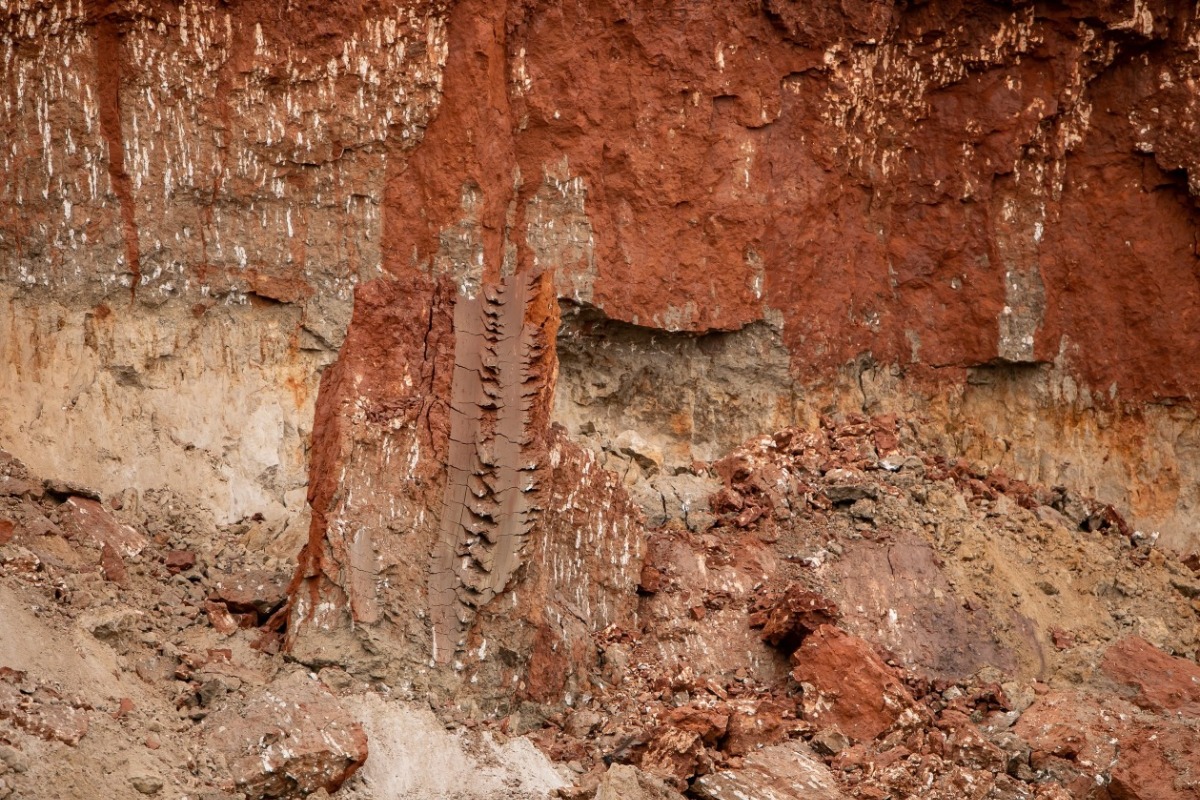
ОКАТИШІ
Залізорудний концентрат використовується для виробництва агломерату та окатишів, необхідних для виплавки чавуну в доменній печі. Про агломерат мова піде в наступній главі. Окатиші – це міцні кулясті гранули діаметром 7−28 мм. Вміст заліза в них досягає 67,5% – набагато більше, ніж у руді.
Для виробництва окатишів потрібно приготувати шихту. Це суміш із концентрату і добавок – флюсу і бентонітової глини. Усі складники треба ретельно перемішати до однорідності, зволожити і скачати у гранули в обертових чашах чи барабанах-огрудкувачах (грануляторах).
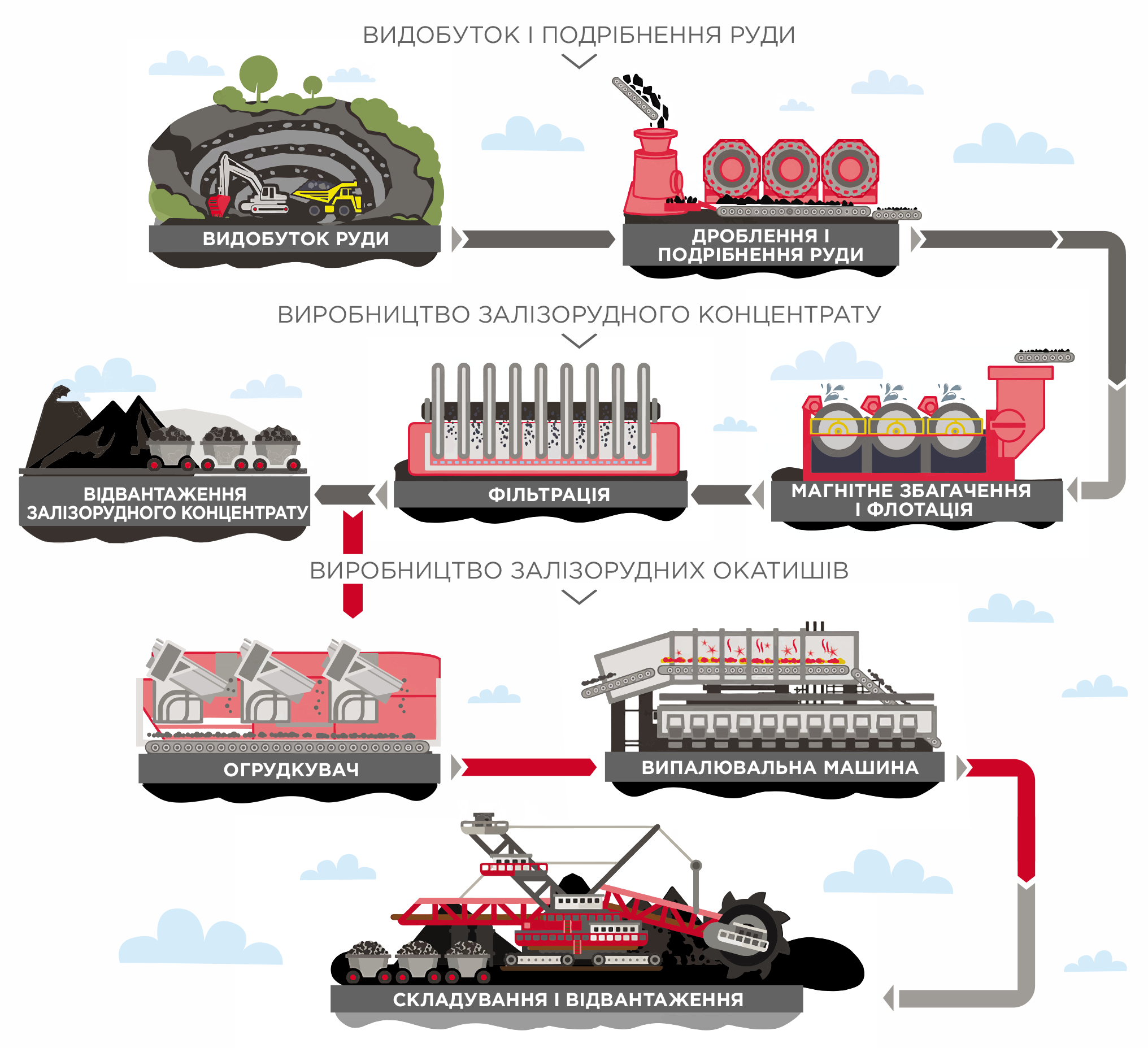
Тепер сирі окатиші слід зміцнити: підсушити за температури 300–600 °C, нагріти, обпалити (1200–1300 °C) та охолодити. Окатиші стали стійкими до тривалого транспортування і можуть довго зберігатися. Ці властивості є важливими для металургійних підприємств, що розташовані далеко від гірничо-збагачувальних комбінатів.
У цьому розділі ми добули руду, збагатили її, перетворили на залізорудний концентрат і навіть наліпили окатишів. Ще кілька важливих інгредієнтів – і ми на порозі металургійної кухні.
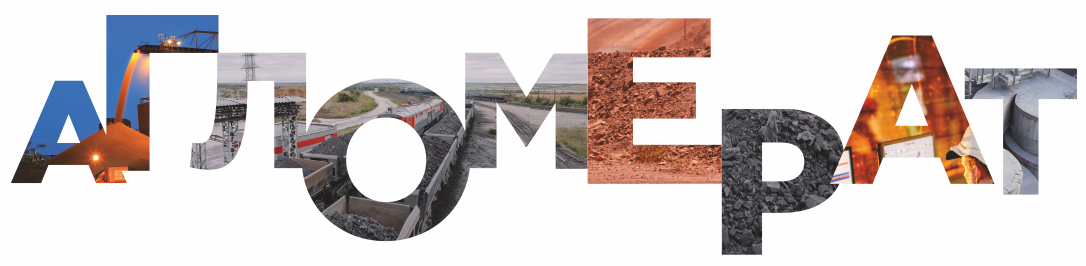
На порозі кухні металургів нас зустрічає агломераційна фабрика. Тут завершується підготовка залізорудної сировини до виробництва чавуну – виготовлення агломерату. На фабриці є місце для зберігання усіх інгредієнтів, техніка для подрібнення і приготування: цехи з приймання сировини, її обробки та відвантаження готової продукції.
Агломерат (від латинського слова agglomerаtus – приєднаний, доданий) – це спечена в пористі грудки дрібна руда. Після збагачення залізна руда перетворюється на концентрат – пил, що може розлетітися від потоків повітря. Завантажувати його в такому вигляді у доменну піч не можна. Тому з концентрату роблять окатиші або спікають у грудки на агломераційних фабриках. Засипають у величезні чаші, перемішують із різними добавками спеціальним міксером, сильно нагрівають і гарячим повітрям підтримують необхідну для спікання температуру. Цей процес і називається агломерацією: так залізорудну сировину перетворюють на напівфабрикат, необхідний для виробництва чавуну. Причому від якості агломерату залежить якість металу. Для приготування нам знадобляться такі продукти: аглоруда (залізорудний дрібняк), залізорудний концентрат, флюсовий вапняк, коксовий дрібняк або енергетичне вугілля. І новий для нас інгредієнт – повернення. Це дрібний агломерат і шихта, що не спеклася. Їх отримують, просіюючи готовий агломерат. Повернення покращує процес спікання. Також додають відходи металургійного виробництва: окалину, шлами, колошниковий пил.
Руда в цьому процесі – центральний компонент. До неї додають і спікають інші елементи шихти. Інгредієнти надходять до приймальних бункерів на рудному дворі, куди залізницею чи на самоскидах привозять сировину. З бункерів матеріали в певному співвідношенні подають до барабанів-змішувачів, які нагадують блендер. Шихту перемішують і зволожують у спеціальних агрегатах. Поступово вона скочується в грудочки, стає зернистою і пухкою, що підвищує її газопроникність. Тобто газ легше з’єднується з частинками палива, дозволяючи масі рівномірно спікатися.
У кулінарії, щоб тісто не пригорало, його кладуть на пергамент. Так відбувається і з агломератом: для шихти простеляють постіль із повернення або великих грудок шихти, що залишилася від попередньої партії агломерату.
Роль духовки тут відіграє спеціальна піч – агломашина. Вона, як і звичайна піч, має колосники – решітки, на які вкладають аглоруду та паливо. На металургійних заводах переважно працюють агломераційні машини стрічкового типу – це безперервний ланцюг спікальних візків із дном з колосникових решіток.
Процес спікання розпочинається в горні агломашини – там запалюють суміш природного газу і повітря. Температура в горні сягає 1400 ˚С. Лише уявіть: приблизно таку температуру має мантія Землі чи розпечена вулканічна лава. Під впливом високої температури вогонь переходить на верхній шар шихти.
Зона горіння поступово просувається зверху вниз. Увесь процес триває 10–20 хвилин. «Корж», що добре пропікся, треба остудити у спеціальному місці – зоні охолодження. Гарячий агломерат охолоджують до 400–600 °С у вакуумному режимі.
Готовий продукт скидають у кінці машини з візків, дроблять, просівають на грохотах, охолоджують повітрям або водою і відправляють у доменний цех. Дрібні грудочки агломерату повертають у змішувач для підготовки шихти – їх використають при виготовленні іншої порції агломерату.
Залишився ще один інгредієнт – і матимемо все необхідне для виплавки чавуну.
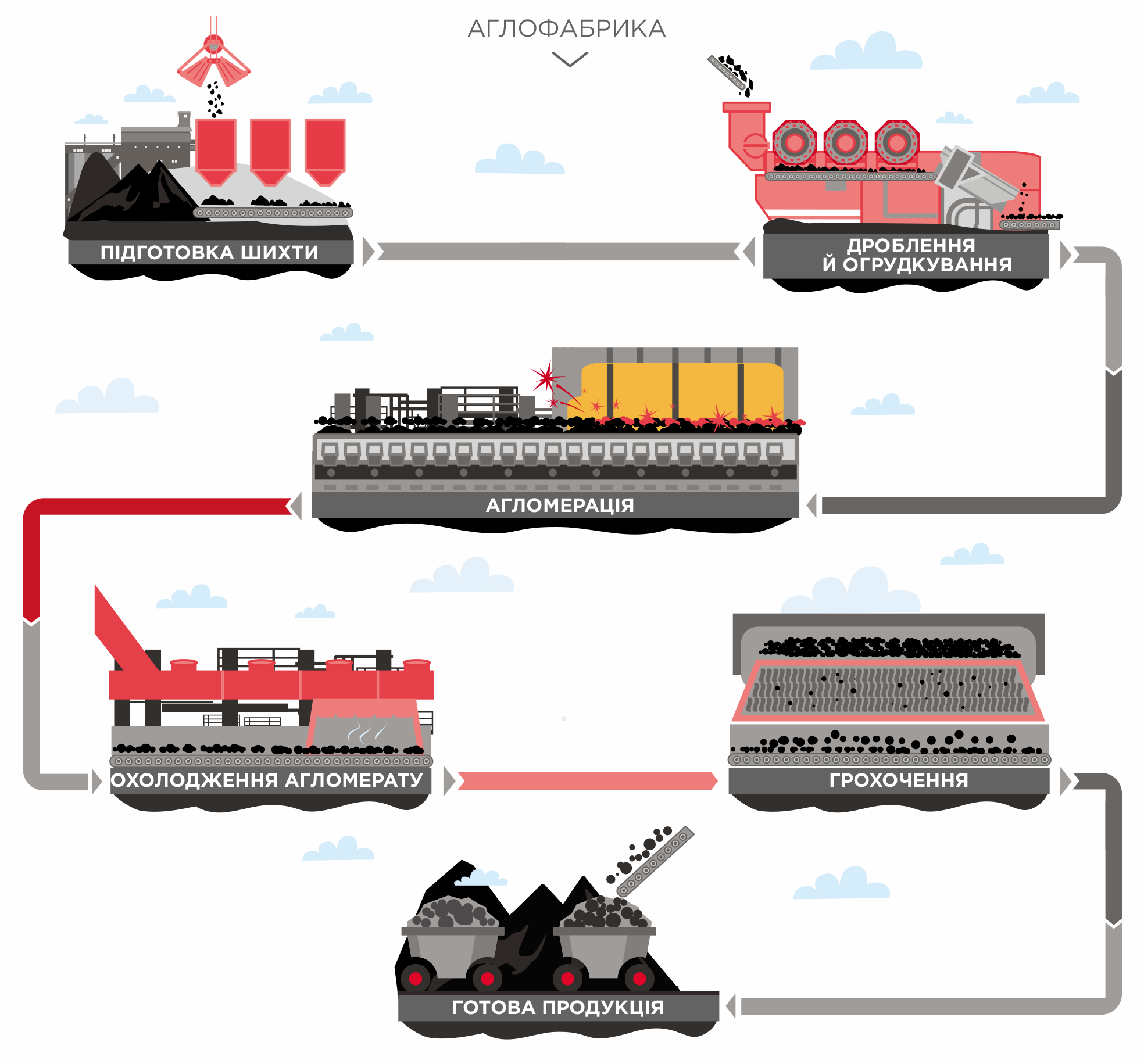
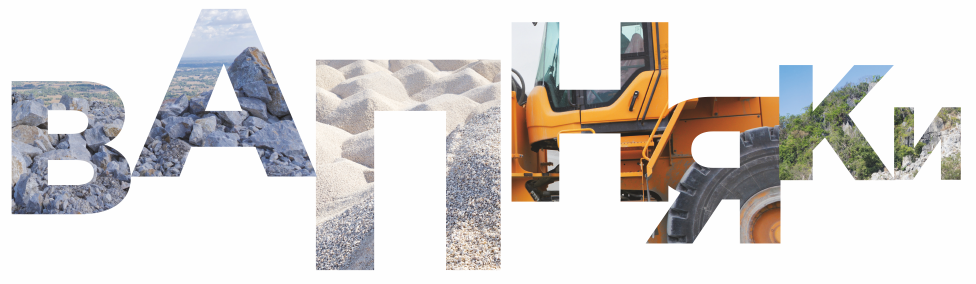
Укулінарії перетворити буденну страву на гастрономічний шедевр допомагають спеції. На кухні металургів теж є своя чарівна приправа – флюсові вапняки.
Кожна людина хоч раз у житті мала справу з вапняками. Ви писали у школі крейдою? Помічали, як навесні вапном білять дерева і бордюри? Знаєте, що буде, якщо карбід змішати з водою? І крейда, і вапно, і карбід виготовляються із вапняків. Наприклад, вапно – це випалений вапняк.
Вапняк – це м’яка гірська порода, сформована на дні моря з решток істот, що жили у воді. В Україні родовища вапняків розташовані на сході, півдні та заході країни. Крім металургії, матеріал використовують у харчовій, хімічній, скляній промисловості, будівництві та сільському господарстві.
Єгипетські піраміди будували переважно з вапняку, який часто добували просто біля них
Флюси – це «корисні бактерії», які додають під час виплавки чавуну і сталі. Вапняки сполучають порожню породу, золу й інші небажані домішки та у вигляді рідких шлаків виносять з печі. Саме від флюсів залежить успішний перебіг плавлення й отримання металу необхідної якості.
Як флюси найчастіше застосовуються вапняк, вапно, боксит, плавиковий шпат, шамотний бій. Основні флюси для металургів – це вапняк і продукт його випалу – вапно. Витрата цього матеріалу при виплавці чавуну і сталі величезна. На 1 т чавуну припадає від 400 до 800 кг, на 1 т конвертерної сталі — до 80 кг.
4600 тонн гірничої маси самосвал може перевезти за зміну, що відповідає вазі 2500 легкових автомобілів
Видобувають вапняк відкритим способом у кар’єрах. Проводять розкривні роботи, піднімають із кар’єру екскаваторами і відправляють на переробку.
Процес розкриву такий самий, як і під час видобутку руди. Спочатку за допомогою бульдозера або навантажувача знімають верхній родючий шар ґрунту – чорнозем. Його зберігають для подальшої рекультивації земель, порушених гірничими роботами.
Далі черга глинистого шару товщиною близько 20 метрів – його виймають екскаваторами. Потім вибирають неякісний вапняк, що залягає одразу під шаром глини.
Ківш екскаватора не завжди може впоратися з міцністю гірської породи. Тому часто видобутку передують буровибухові роботи.
Це дуже відповідальна частина усього процесу. Твердий шар вапняку бурять, закладають вибухові матеріали і підривають. Середня глибина однієї свердловини – 15 м, а інколи може сягати і 32 м. Діаметр – 25 см. Найчастіше роблять декілька свердловин. Буріння однієї триває близько години. Вибухи відбуваються по черзі, із затримкою у декілька сотих часток секунди.
Гірську породу вантажать в автомобілі та перевозять на дробильно-збагачувальні фабрики. Вапняки проходять щокову і конусну дробарки, які діють за принципом роздавлювання, стирання і розлому. Потім грудки відправляють на віброгрохоти для класифікації. Готовий продукт перевантажують у вагони, а дрібні некондиційні грудочки – відсів – їдуть назад у кар’єр. Там на вже відпрацьованій території роблять відвали, які потім рекультивують. Родючий шар ґрунту, який раніше зняли для видобутку вапняку, повертається на місце. Висаджують дерева. У такий спосіб зменшується вплив на довкілля.
Наша мета зовсім близько. Вже в наступному розділі ви відчуєте жар від доменних печей і на власні очі побачите салют металу.
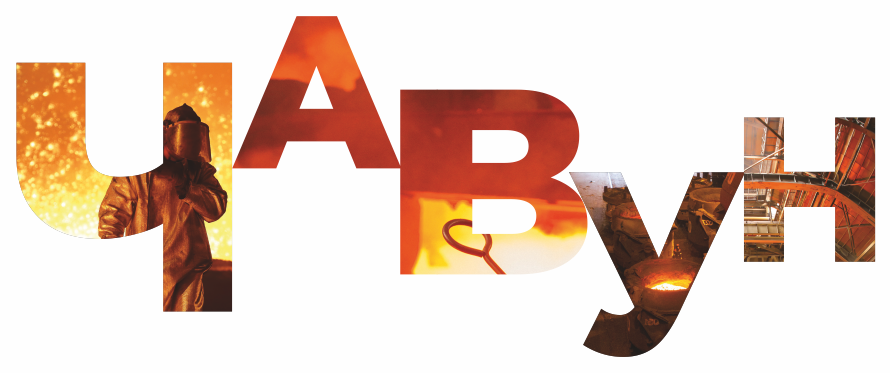
Нарешті ми дісталися справжніх видовищ. Випуск чавуну з доменної печі нагадує виверження вулкана або салют. Байдужим залишитися неможливо.
Усі продукти для основної страви металургійного комбінату готові. Ми добували вугілля і переробляли його на кокс, діставали з надр землі руду і виготовляли з неї агломерат. Дізналися, що таке флюси і де використовують вапняк. Тепер усі ці інгредієнти ми опустимо у величезну посудину – доменну піч і почнемо варити чавун.
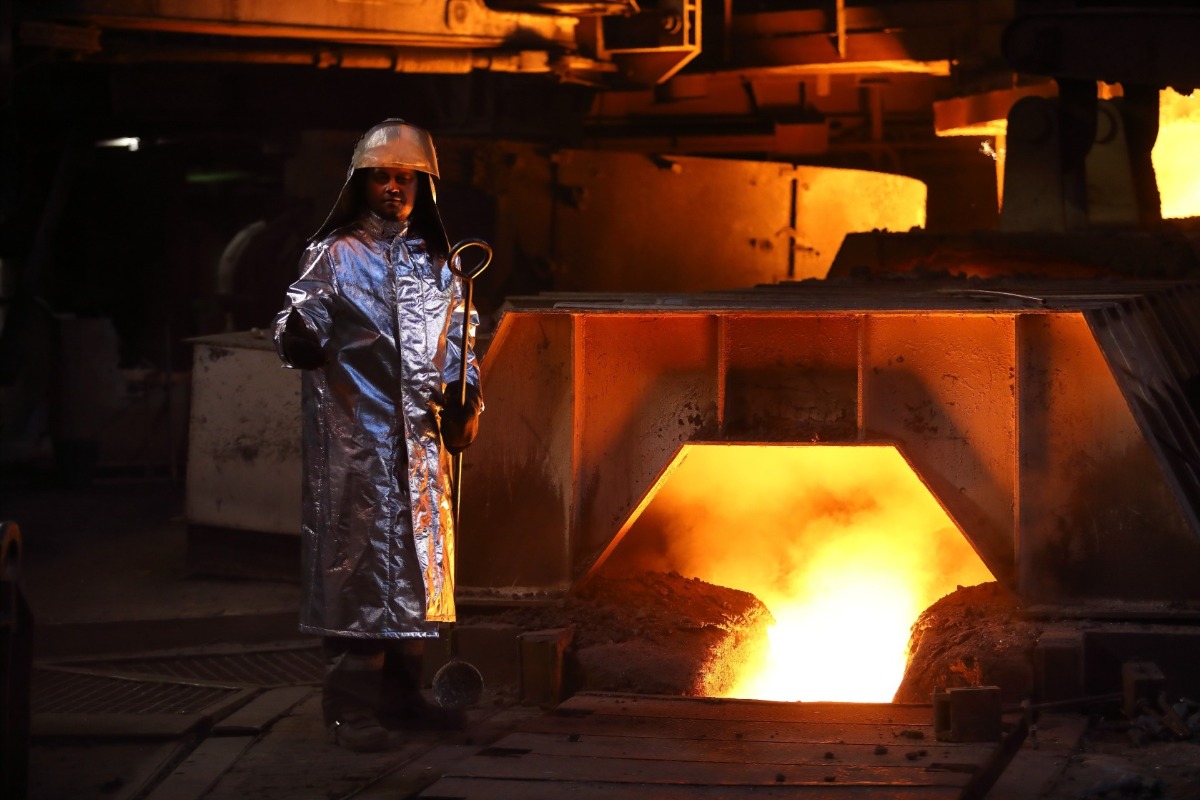
Горновий під час випуску чавуну з доменної печі
Чавун і сталь – це сплави заліза з вуглецем і домішками інших хімічних елементів. Спільне в них – залізо. А відмінність у тому, що вуглецю в чавуні більше, ніж у сталі. Із чавуну роблять безліч речей: від каналізаційних люків до батарей і сковорідок. А ще його переробляють на сталь: додають сталевий брухт, легувальні елементи та знижують концентрацію вуглецю і шкідливих домішок – фосфору та сірки, які роблять сталь крихкою і ламкою.
Як правило, на кухні господині носять фартухи і ховають волосся. У нас так само – металурги обов’язково надягають захисні костюми, каски й окуляри.
КОНСТРУКЦІЯ ДОМЕННОЇ ПЕЧІ
Головне на кухні – це піч. На металургійних комбінатах теж є піч –доменна. Якщо порівняти з кухонною технікою, вона подібна до мультиварки. Два в одному – і піч, і каструля.
Доменна піч, або домна, за формою нагадує велику круглу вежу. Вона сягає 35 м у висоту і має 1000–5,500 м3 корисного об’єму. Головна особливість печі – з моменту запуску вона має постійно працювати, адже процес плавлення чавуну зупиняти не можна.
2250°C – максимальна температура в домні. Це лише вдвічі нижче, ніж на поверхні Сонця
Температура у домні – до 2 000 °C. Зсередини вона викладена вогнетривким матеріалом, а зовні одягнена у сталевий кожух. Верхня частина доменної печі називається колошником. Його ширина – близько 8 м. Сюди завантажується шихта: залізовмісні компоненти (агломерат, окатиші), кокс і флюси. Розмір, якість і кількість кожного окремого інгредієнта впливає на остаточний продукт. Якщо шматки більшого розміру, ніж потрібно, їх пропускають через грохоти. Потім порціями подають у доменну піч.
Щоб підняти інгредієнти на висоту 35 м, використовують скіповий підйомник або конвеєри. Інгредієнти надходять постійно і засипаються шарами. Для герметичності подачі та рівномірного розподілу шихти використовується засипний апарат. Тривалість процесу від завантаження продуктів до отримання готової «страви» – близько шести годин.
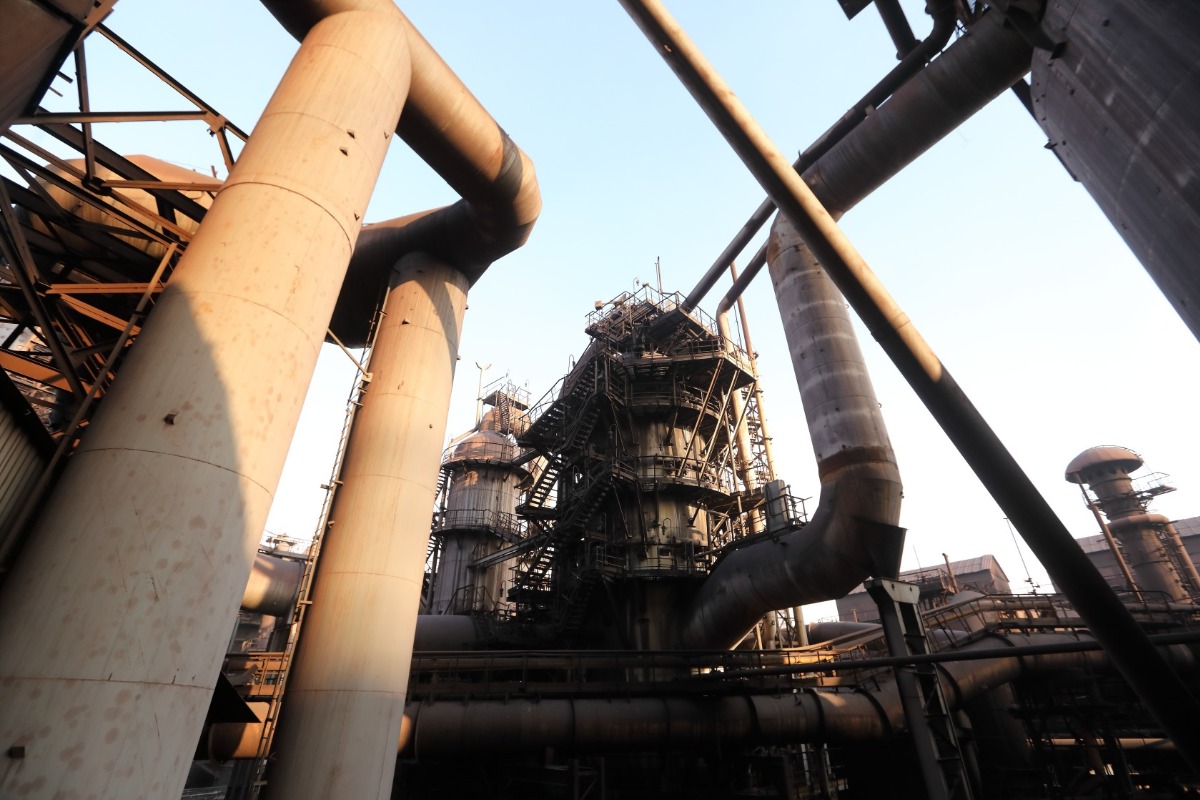
Найширша частина домни – це розпар. Він має форму циліндра і розташований посередині агрегату. З колошника інгредієнти опускаються в шахту, що розміщується між колошником і розпаром.
Найнижча частина доменної печі – горно. Це серце домни. Саме тут збираються чавун і шлак. Дно домни називається подом. Піч стоїть на залізобетонному фундаменті.
ВИПЛАВКА ЧАВУНУ
Щоб домна «готувала», потрібна дуже висока температура. Основне паливо – кокс. Його розпалюють підігрітим повітрям. Як багаття у лісі: щоб дрова розгорілися, на них треба подути. Цей процес так і називається — гаряче дуття.
Щоб полум’я розгоралося швидше, до повітря додають кисень – таке дуття називають комбінованим. У верхній частині горна є спеціальні пристосування для вдування повітря – фурми. Від них відходять труби з подвійними стінками. Між стінками труб циркулює вода для охолодження фурм. Трубами подається нагріте до 1050—1300 ˚С повітря. Процес нагрівання відбувається у каупері – повітронагрівачі.
За розмірами нагрівач лише трохи поступається доменній печі. Це вертикальний циліндричний сталевий кожух із внутрішньою «шаховою» насадкою з вогнетривкої цегли. Очищений газ із доменної печі підводиться до каупера і спалюється у камері горіння. Продукти горіння піднімаються вгору і нагрівають цегельну насадку. Коли досягають необхідної температури, нагрівання припиняють, каупер переводять у режим дуття для подачі тепла до фурм.
У кожної домни зазвичай три-чотири каупери. Два нагріваються, а решта подає гаряче дуття. Потоки перемикаються так, що потрібна температура підтримується безперервно. Від гарячого повітря біля фурм кокс починає горіти. Відпрацьовані гази піднімаються вгору і нагрівають шихту. Під впливом температури вона розм’якшується і опускається вниз. Унаслідок хімічної реакції залізо відновлюється і збагачується вуглецем. Воно розплавляється і краплями стікає в горно, утворюючи чавун.
У сучасних доменних печах на 1 тонну чавуну виділяється 1250–1800 м3 газу. Його використовують як паливо в інших процесах на металургійній кухні.
Як промивають і очищають від сміття крупу перед приготуванням, так і доменний газ треба звільнити від пилу.
2 500 000 000 сковорідок можна виготовити з чавуну Метінвесту за рік
Його кількість залежить від якості підготовки сировини до плавки, міцності коксу та роботи печі. У поганих умовах кількість пилу може сягати 100 г/куб. м. У хороших умовах – 30–35 г/куб. м. Для нормальної роботи пальників доменний газ очищають, щоб вміст пилу не перевищував 5 мг/куб. м.
Для кожної доменної печі споруджують індивідуальну систему газоочищення з кількох послідовно встановлених апаратів. Пил класифікують як грубий, напівтонкий і тонкий. Доменний газ можна очистити сухим і мокрим способом. Спочатку проводиться грубе очищення сухим способом. Потім — напівтонке. Газ рясно зволожують, змочені частинки пилу видаляються у вигляді шламу. Остання стадія — тонке очищення наелектризуванням частинок.
Остаточні продукти доменної плавки – це чавун і шлак. Для випускання продуктів плавки з домни є отвори – льотки. Їх кількість може бути від однієї в малих печах до трьох-чотирьох у великих. Наприклад, на комбінатах Метінвесту переважно працюють середні доменні печі з двома льотками. До речі, щільність шлаку менша, ніж у чавуну, тож вони ніколи не змішуються.
Чавун і шлак випускають циклічно через певний проміжок часу. Отвір для випуску продуктів плавки не може постійно бути відтулений, тому його затуляють вогнетривкою масою. Забивання маси, а також буріння отвору для випуску роблять спеціальні машини. Чавун і шлак виливають у ковші. Для транспортування чавуну використовують чавуновози з відкритим грушоподібним ковшем або ковші міксерного типу.
ВИДИ ЧАВУНУ
От і все – чавун готовий! Але він буває різним. Залежно від призначення чавуни поділяють на види: переробний (для подальшої переробки на сталь), ливарний (для відливання виробів), доменні феросплави (використовуються у сталеплавильному виробництві).
Товарний чавун, що призначений для продажу, подається на стрічковий конвеєр розливної машини із двох паралельних нескінченних ланцюгів. До них прикріплені чавунні виливниці – мульди. Це спеціальні форми, в які розплавлений чавун виливають з ковша. Майбутні зливки (чушки) обливають водою для охолодження. Ланцюги безперервно рухаються. Зливки застигають, перекидаються і жолобом потрапляють на залізничну платформу або у вагонетку. Маса однієї чушки – від 12 до 18 кг.
Шлак, що вийшов із доменної печі, не пропадає! Його використовують у будівництві залізобетонних споруд і доріг. Рідкий переробний чавун прямує далі. Як із нього роблять сталь, ви дізнаєтеся з наступної глави.
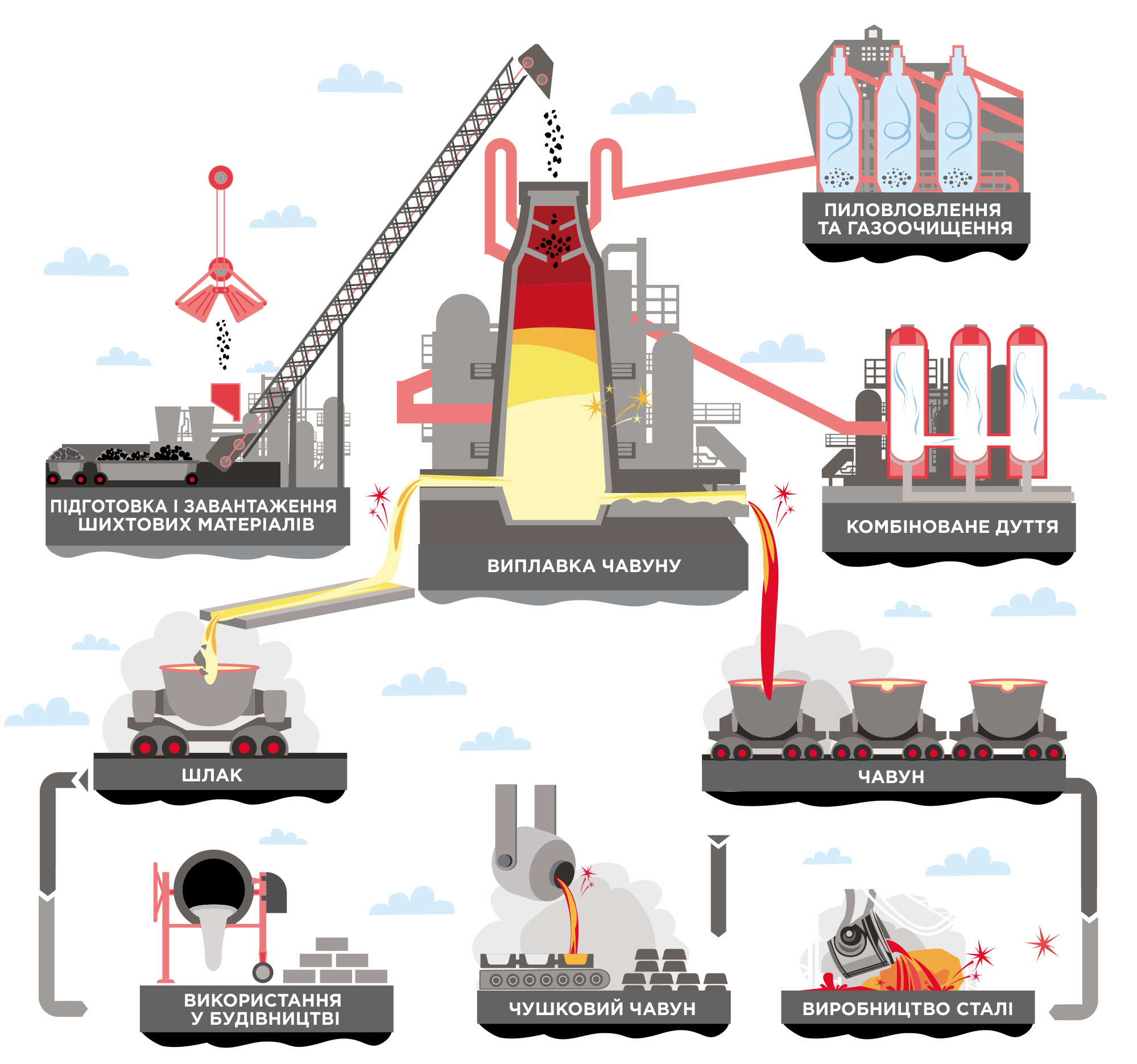
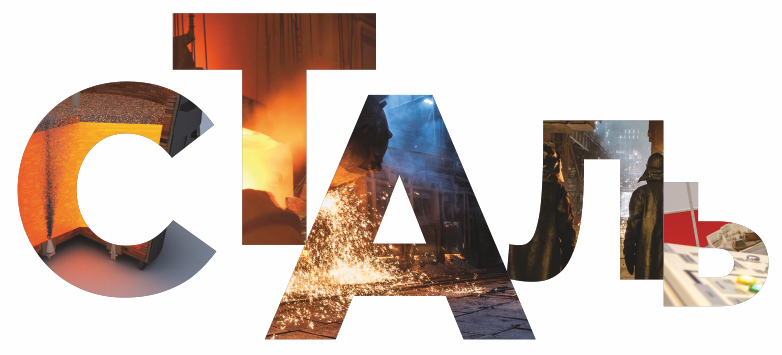
Коронна страва металургійної кухні – сталь. Існує величезна кількість видів сталі: її класифікують за призначенням, хімічним складом, якістю, структурою. А от способів виробництва не так багато. Основні – конвертерний, мартенівський і електродуговий. Назви походять від агрегатів, у яких готують сталь, – конвертерів, мартенівських і електричних печей. Найпопулярніший спосіб – конвертерний. Так виплавляють понад двох третин усієї сталі у світі.
КОНВЕРТЕРНЕ ВИРОБНИЦТВО
Щоб отримати конвертерну сталь, нам потрібні переробний чавун і сталевий або чавунний лом. Приправимо флюсами: вапном, вапняком, плавиковим шпатом або бокситом. А для пікантності додамо кисень – він запускає процес окиснення.
У чавуні є надлишковий вуглець, кремній, марганець, а також шкідливі домішки – сірка та фосфор, які роблять сталь крихкою. Такий матеріал не можна кувати або прокатувати. Потрібно зменшити вміст шкідливих домішок. Це й відбувається під час окиснення металу.
Сталь готується у спеціальній каструлі – конвертері (від латинського convertere – змінювати, перетворювати). Це сталева посудина грушоподібної форми, зсередини викладена вогнетривкою цеглою. Її місткість — від 50 до 400 тонн.
Конвертер – досить рухлива посудина. Вона може повертатися навколо горизонтальної осі на 360 градусів. Для завантаження інгредієнтів конвертер нахиляють, через горловину засипають металобрухт і заливають гарячий (1250–1400 ˚С) чавун. Потім конвертер повертають у вертикальний стан, вводять водоохолоджувальну фурму і через неї подають кисень.
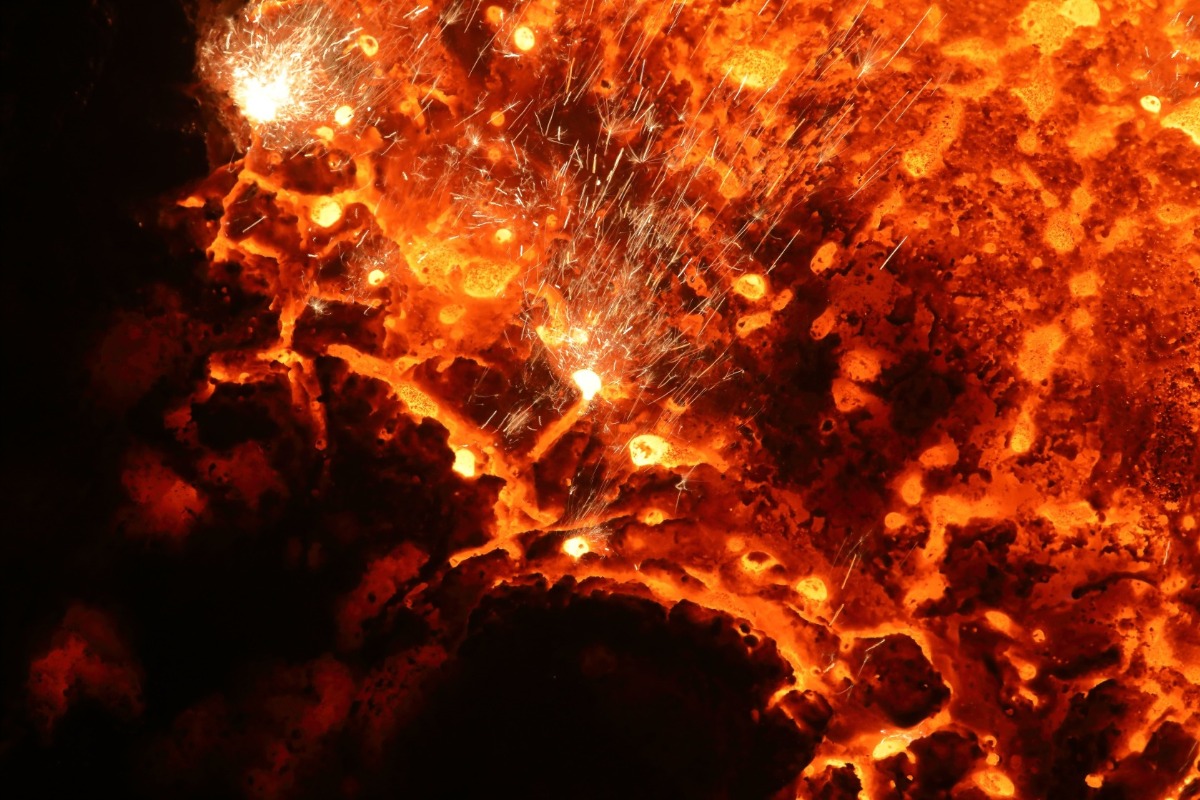
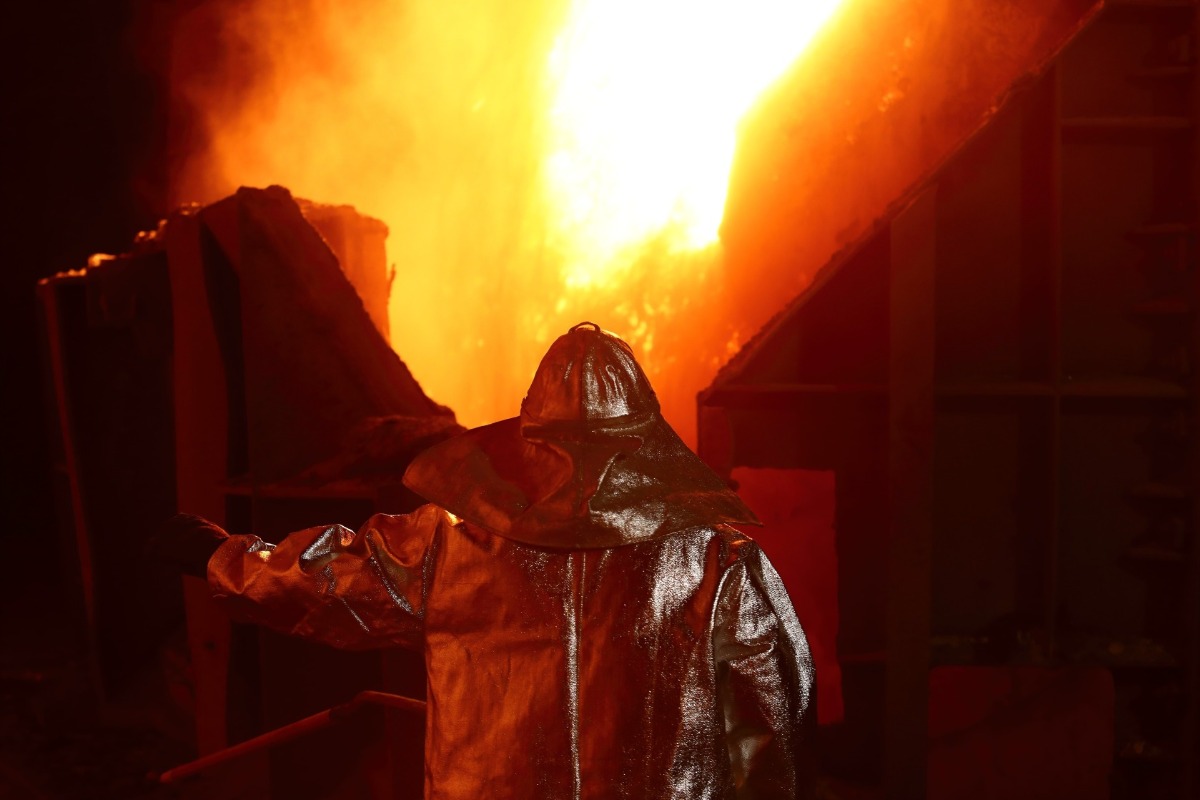
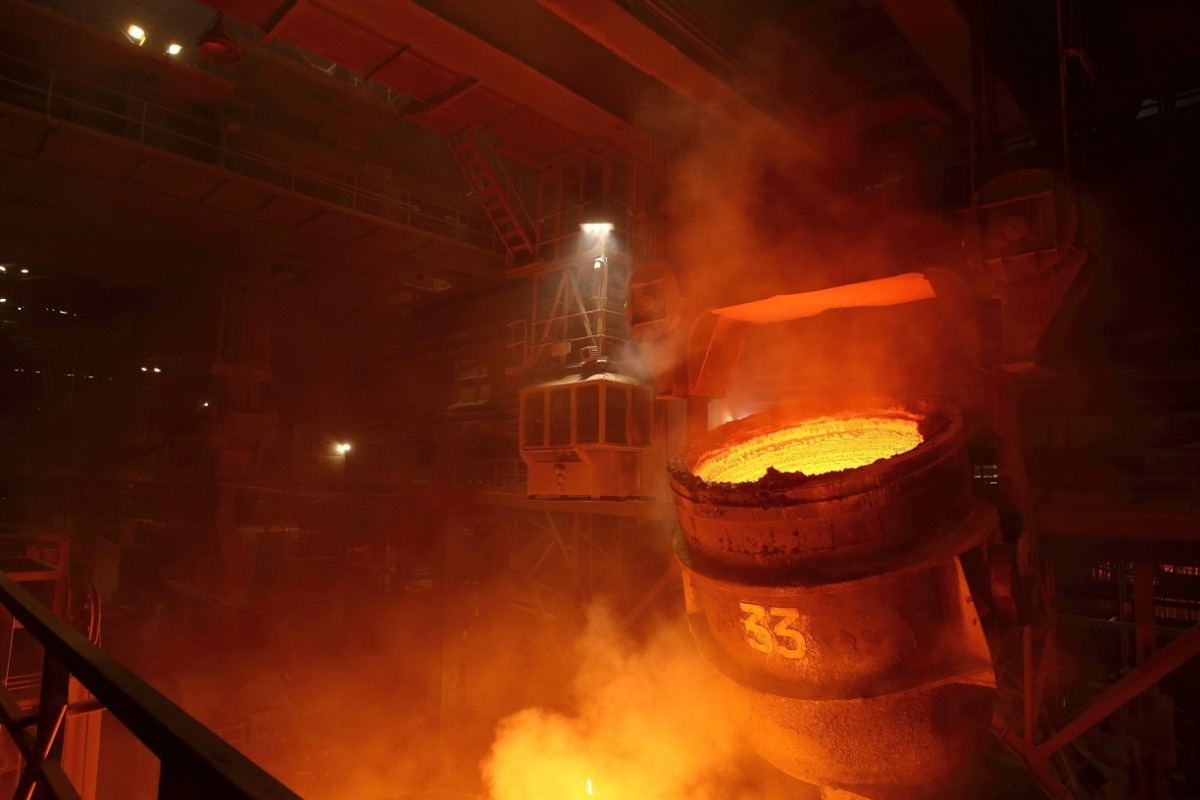
Струмінь кисню перемішує та окиснює рідкий метал. Під час хімічної реакції виділяється тепло, що підігріває вміст конвертера до потрібної температури. Паливо для нагрівання не використовується. Домішки кремнію і марганцю сполучаються з киснем і згоряють. Коли температура підвищується, згоряє і зайвий вуглець. Залізо інтенсивно окиснюється. Оксид заліза розчиняється у шлаку і металі, збагачуючи метал киснем.
Плавлення триває півгодини-годину. Щойно вміст вуглецю доходить до потрібного рівня, продування завершують. Конвертер знову нахиляють і через льотку випускають сталь у ківш. Потім нахиляють в інший бік — і через горловину зливають шлак у спеціальну чашу, встановлену в шлаковозі під конвертером.
Тепер сплав треба довести до ладу: збалансувати за температурою і хімічним складом, видалити шкідливі домішки, додати легувальні елементи. Усі ці операції називають позапічною обробкою сталі. Вони виконуються у сталерозливному ковші із застосуванням додаткового обладнання. У кисневих конвертерах переважно виплавляють вуглецеві (із вмістом вуглецю від 0,02% до 2%), низьколеговані та леговані (із додаванням хрому, нікелю, молібдену) сталі.
Останній етап – розливання сталі в заготівки, які потім переробляють на металопродукцію (лист, рулон, рейки, арматуру, катанку й інші вироби). Сталь можуть розливати декількома способами. Наприклад, із ковша – у виливниці, чавунні форми для виготовлення зливків. У них сталь твердне, а зливки потім прокочують на обтискному стані. Так з’являються заготівки, з яких роблять металопродукцію. Від форми виливниці залежить, яким буде кінцевий продукт: із зливків з квадратним перетином роблять сортовий прокат, з прямокутним – листи, з круглим – труби. Такий спосіб особливо підходить для високолегованих сталей.
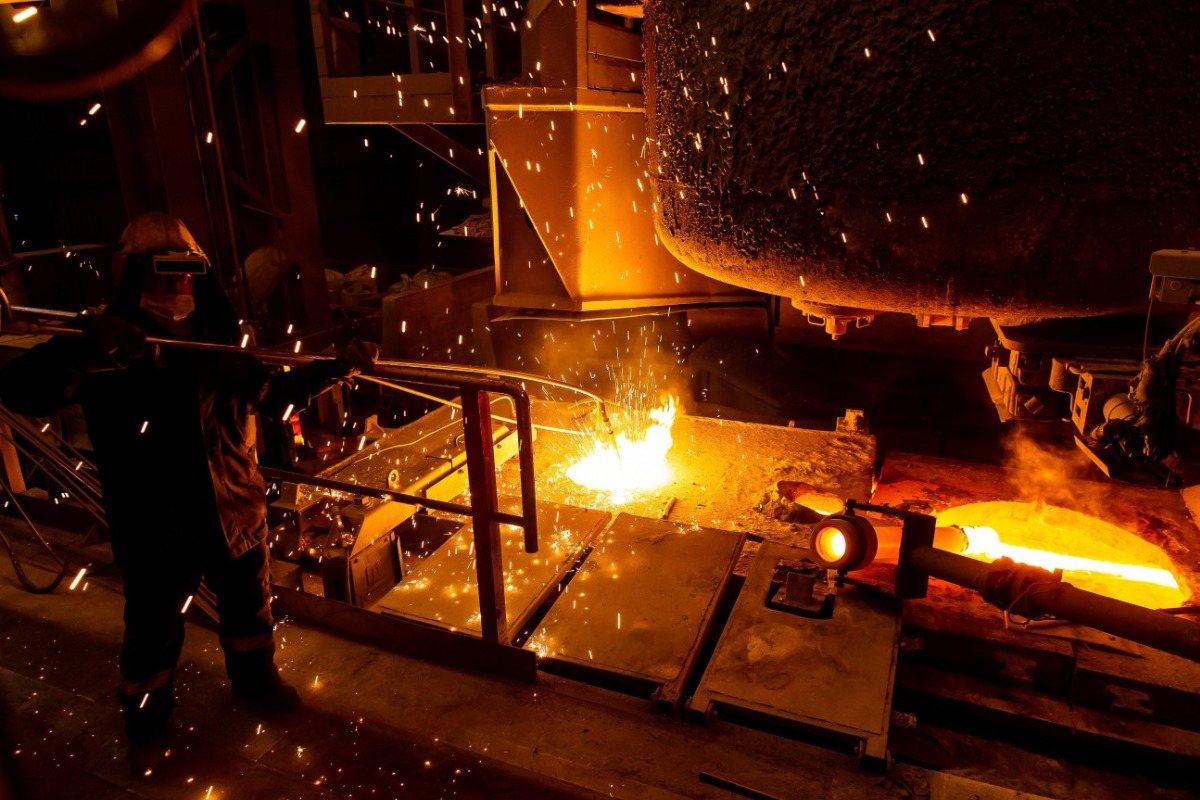
МБЛЗ на ММКІ
Також сталь розливають безперервно за допомогою машини безперервного лиття заготівок (МБЛЗ). Вона одразу дає заготівку потрібної форми. При такому способі сталь із ковша потрапляє у проміжну ємність (промковш). Нижче розміщується кристалізатор, що охолоджується водою. Це виливниця, тільки без дна. Перед заливанням металу в кристалізатор вводять затравку — сталеву штангу зі змінною голівкою. Затравка замінює дно у виливниці, після розливання її знімають із заготівки. Зливок виходить рідкий усередині, із застиглою скоринкою. Щоб заготівка остаточно затверділа, її охолоджують водою. Готовий напівфабрикат ріжуть на частини. Так з’являються сляби, блюми і сортова заготівка.
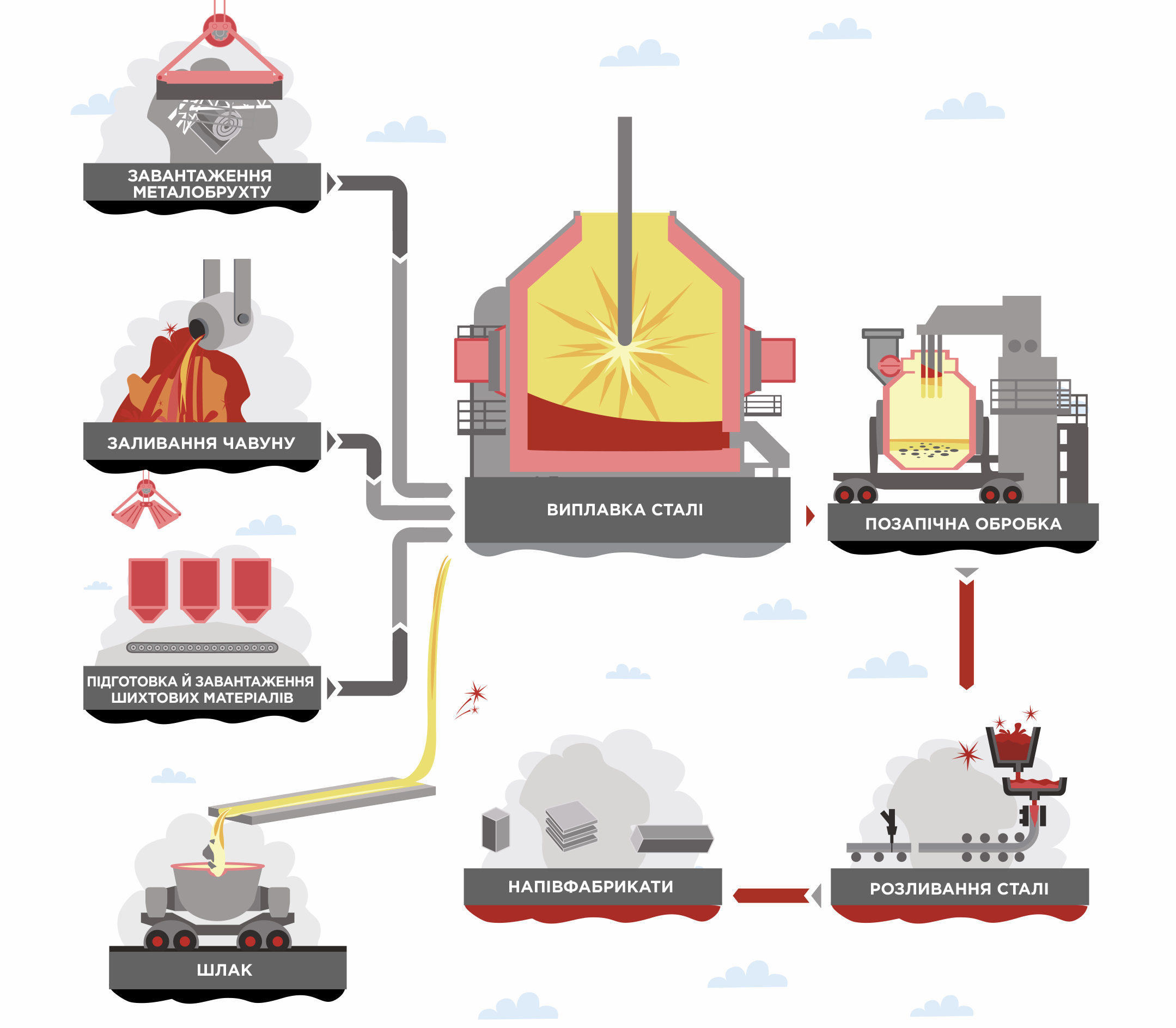
МАРТЕНІВСЬКЕ ВИРОБНИЦТВО
Ця технологія починає свою історію із середини XIX століття. Назва процесу походить від прізвища французького інженера і металурга П’єра Еміля Мартена, який створив плавильну піч такого зразка у 1864 році. До сімдесятих років ХХ століття мартен був основним способом виробництва сталі. У наші дні його витіснили киснево-конвертерний і електросталеплавильний способи.
Інгредієнти для приготування залишилися такі самі – чавун, сталевий брухт, залізна руда, флюси і легувальні добавки. Головна відмінність від конвертерного виробництва полягає в тому, що виплавити сталь у мартені неможливо без палива – природного газу.
Мартенівська піч схожа на величезну ванну, зсередини викладену вогнетривкою цеглою. Над ванною – склепінчаста стеля. Знизу – подина. У передній стінці печі є вікна для завантаження інгредієнтів. У задній стінці розміщені отвори для випуску металу і шлаку. Щоб сталь не витекла завчасно, випускні отвори забивають корком із вогнетривкої глини.
Мартени бувають різних розмірів. У них можна виплавити від декількох тонн до декількох сотень тонн сталі. Тривалість плавки залежить від маси розплаву і частки металобрухту в шихті. Весь процес триває 6–8 годин.
Плавка складається з декількох етапів. Спочатку в спеціальні короби – мульди – завантажують брухт, руду і вапно. Завалювальна машина доставляє шихту до вікон і завантажує сировину, а потім їх закривають товстими сталевими засувами.
Скрап нагрівають розпеченою сумішшю природного газу і повітря до температури 1300–1400 °С. Тим часом у ковші підвозять гарячий рідкий чавун і через жолоб заливають у піч.
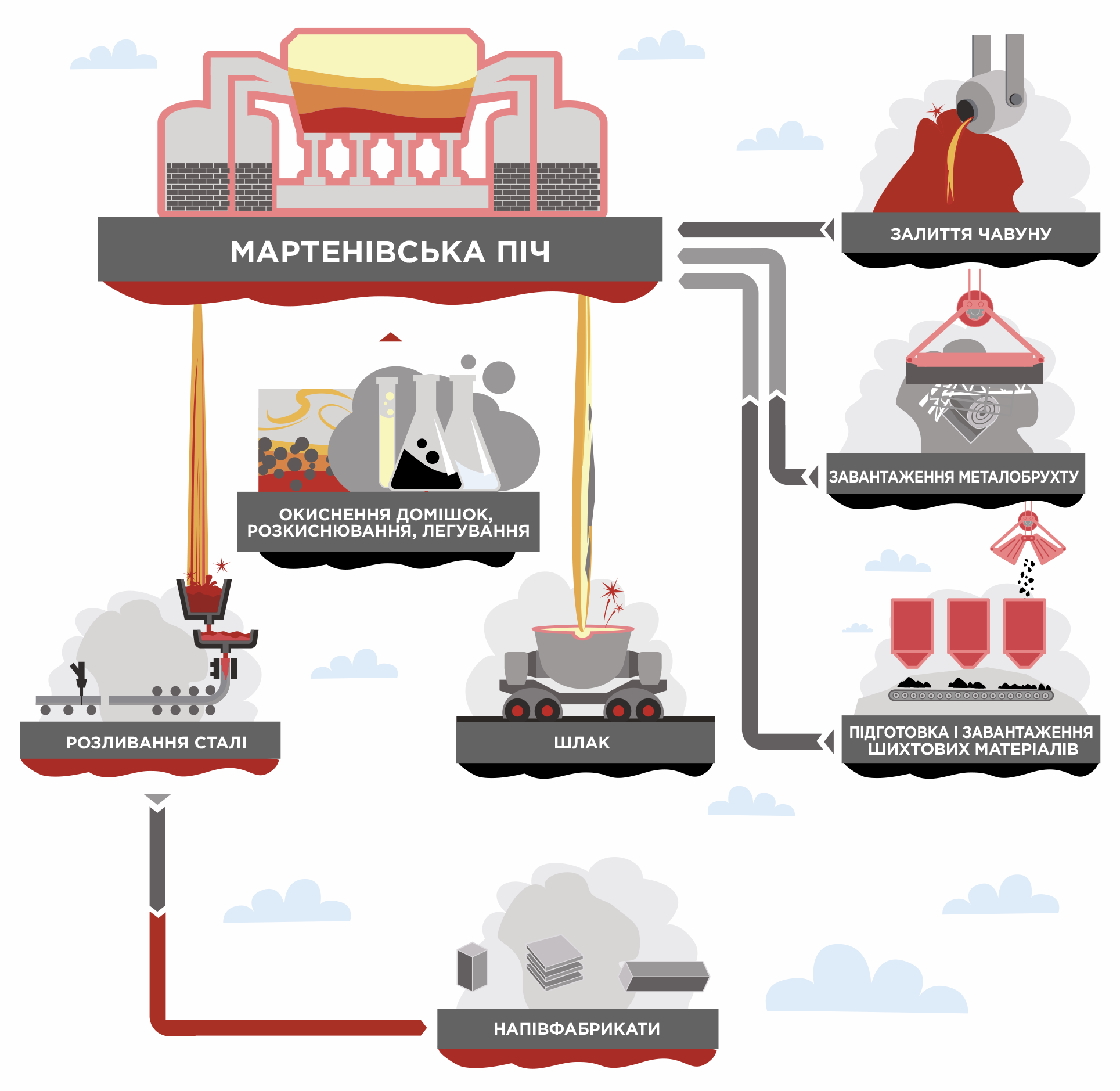
Етап плавки – це розплавлення брухту, розкладання вапняку і розчинення оксидів заліза в шлаку, окиснення домішок шихти. Під час нагрівання з розплаву стрімко виділяються гази, і він починає фонтанувати. Щойно метал «заспокоюється», плавка завершується.
Наступний етап – доведення і розкиснювання металу. Від того, наскільки правильно відбуваються ці процеси, залежить якість готової сталі. Сплав доводять до кондиції: при нагріванні металу видаляються гази і неметалеві сполуки, вуглець окиснюється. Вміст сірки та фосфору зменшується.
Після цього метал розкиснюють і за необхідності легують. За цей час сталевар через оглядові вікна декілька разів бере експрес-проби. Великою сталевою «ложкою» зачерпує метал і перевіряє його на вміст шкідливих домішок, щоб скоригувати хімічний склад. Продукт готовий. Сталь із сталевипускного отвору в печі виливають у ківш. Далі з ковша її розливають у менші за розміром ємності – виливниці, або використовують машини безперервного лиття, щоб зробити готові напівфабрикати. Після того як зливок у виливниці затвердіє, його обробляють на обтискних станах – роблять заготівку, яка згодом перетвориться на металопродукцію.
ЕЛЕКТРОДУГОВИЙ СПОСІБ
Із другої половини ХХ століття все більше сталі виробляється в електропечах. Цей спосіб потребує чимало електроенергії. Тому його розвивають країни, які можуть собі це дозволити: США, Індія і Китай. Сьогодні електросталь посідає близько третини від усього світового виробництва. Найбільше такої сталі виплавляється в дугових печах.
Піч складається із залізного кожуха зі сферичним дном. Усередині кожух викладений вогнетривкою цеглою. Плавильний простір печі накривається склепінням, що повертається у різні боки. Пристрій нагадує величезну мультиварку.
Для приготування страви в «горщику» беруть металевий брухт та інші потрібні для конкретної марки сталі інгредієнти. Приправляють вапняком. Після завантаження інгредієнтів «казанок» накривають кришкою, занурюють електроди і вмикають струм. Вміст «горщика» нагрівається до 1500 °C. Втім енергію дають не самі електроди, а дуговий розряд між ними і шихтою. Саму ідею металургам підказало природне явище — блискавка. Електричний заряд мчить від електродів до рідкого металу так само, як блискавка із хмар прямує до землі.
Понад 7000 км вийде, якщо викласти в лінію усі сляби, виплавлені за 25 років на МБЛЗ № 1 ММК ім. Ілліча. Це довжина річки Амазонка
Після завершення плавки в печі залишається сталь і шлак. Шлак вбирає в себе усі непотрібні домішки і спливає догори. Суть процесу – отримати напівфабрикат необхідного хімічного складу.
Для керування перебігом плавки в печі є робоче вікно, льотка для випуску сталі та вікно для зливання шлаку.
Електропечі бувають різної місткості – від 0,5 до 400 тонн. Час плавки становить лише 40–55 хвилин, що дає можливість робити до 40 плавок на добу. Електропечі дозволяють отримувати якісну сталь. Цей спосіб використовують для виплавки високолегованих, конструкційних, спеціальних сталей і сплавів.
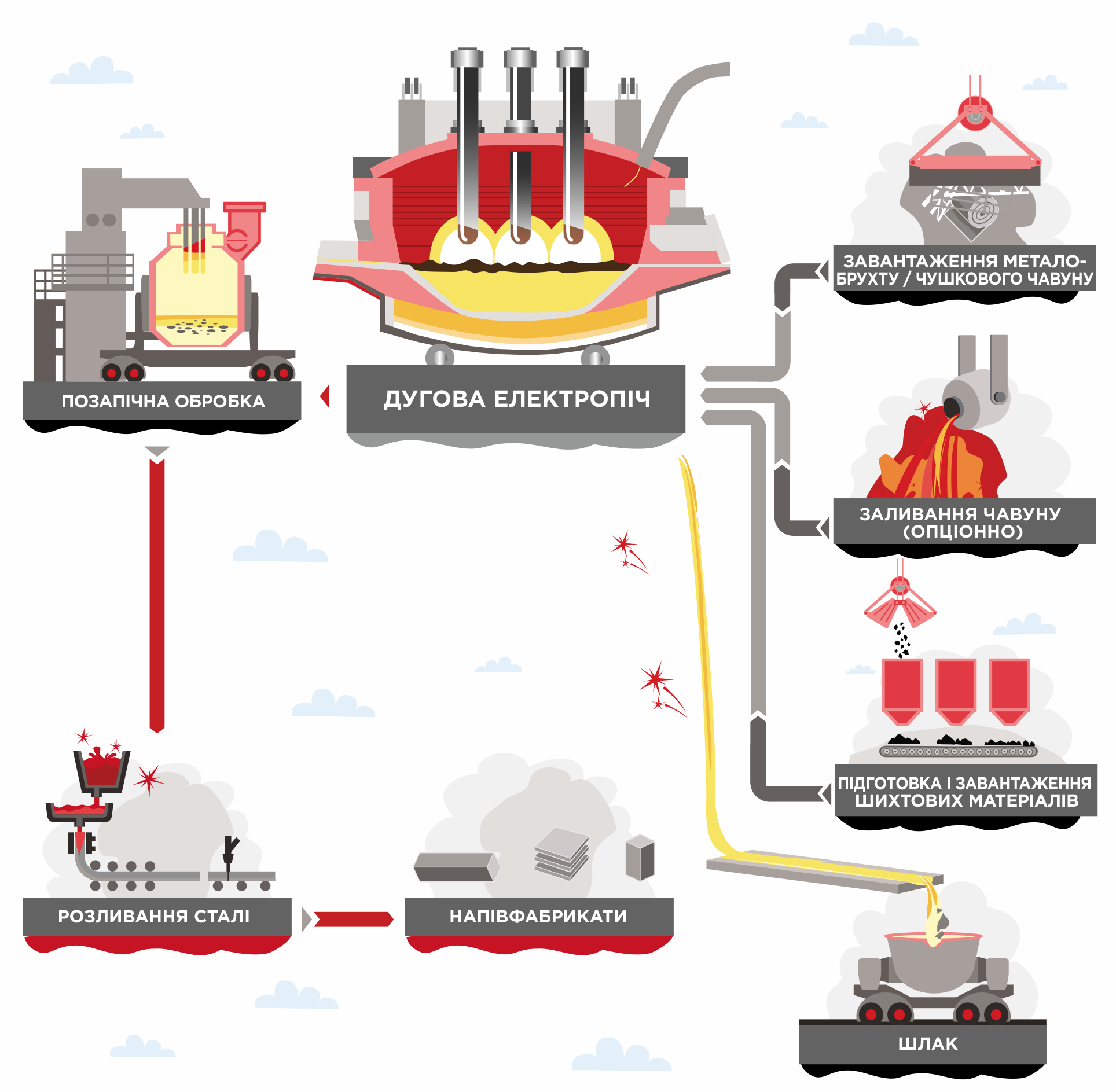
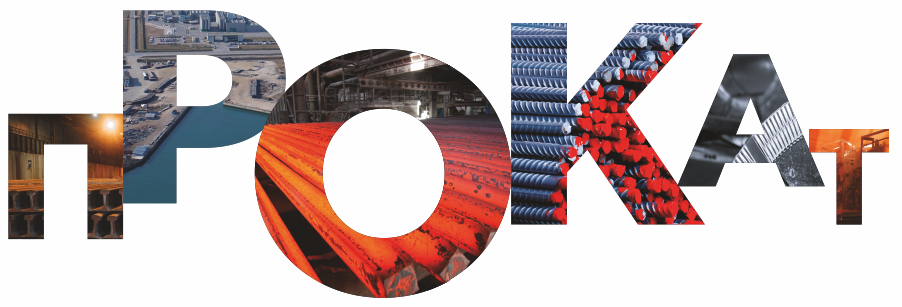
Сталева продукція потрібна усім галузям економіки: 50% використовується у будівництві, 16% припадає на механічне обладнання, 13% – на автомобілі, 5% – на інший транспорт, ще 3% – на електрообладнання.
Сталі, що випускають у світі щодня, вистачить на 548 Ейфелевих веж. На одного жителя Землі припадає в середньому 215 кг сталевої продукції на рік. Україні теж є чим пишатися. Ми – серед найбільших світових виробників сталі. З року в рік металурги винаходять нові марки сталі, щоб випустити ще більше видів продукції. Сукупність різної за формою і розмірами продукції називається сортаментом. Хочете вразити знанням металургійних термінів у розмові – робіть наголос на другому складі.
Продукцію поділяють на плоский прокат, сортовий прокат, труби та гнуті профілі. До цих груп належать різні види продукції. Наприклад, сортовий прокат містить крупний, середній і дрібний сорт – залежно від розмірів. Усі продукти роблять із напівфабрикатів, що відрізняються лише за формою.
Із слябів отримують гарячекатані рулони та листи, із квадратної заготівки – середньосортний і дрібносортний прокат, із блюмів – крупносортний прокат, а із круглої заготівки – труби.
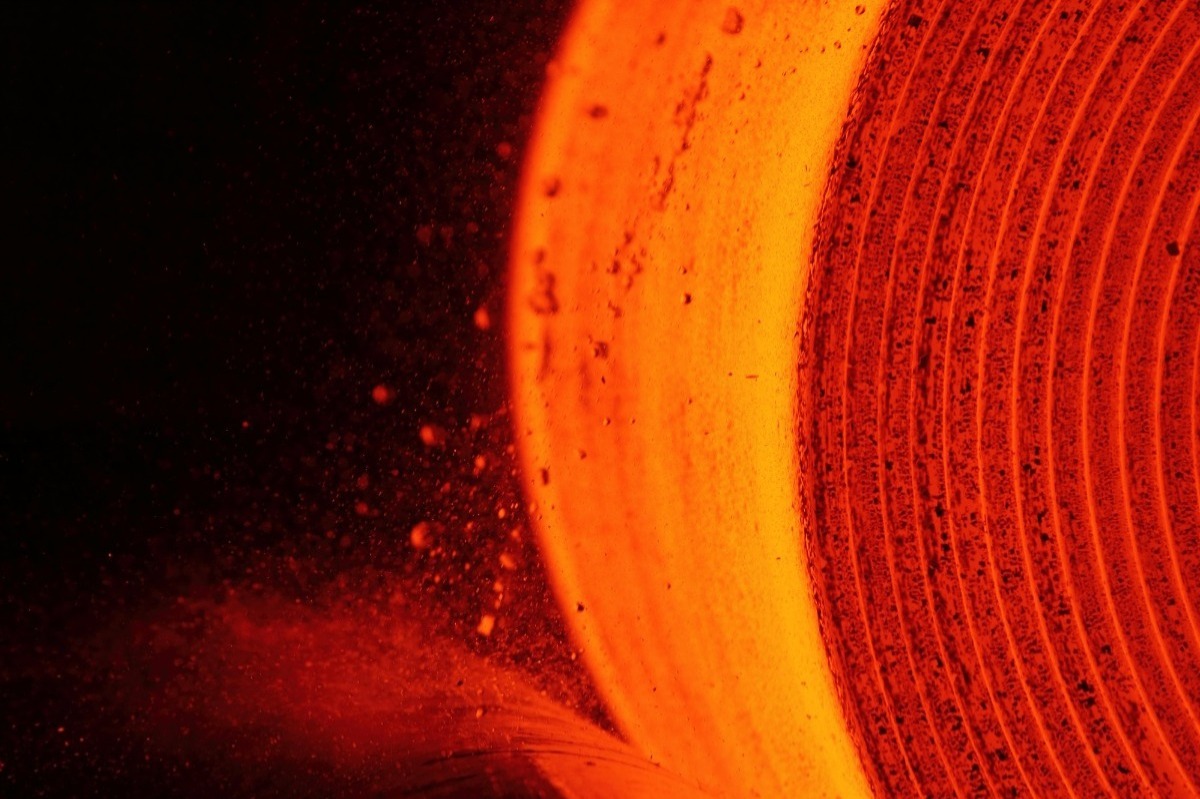

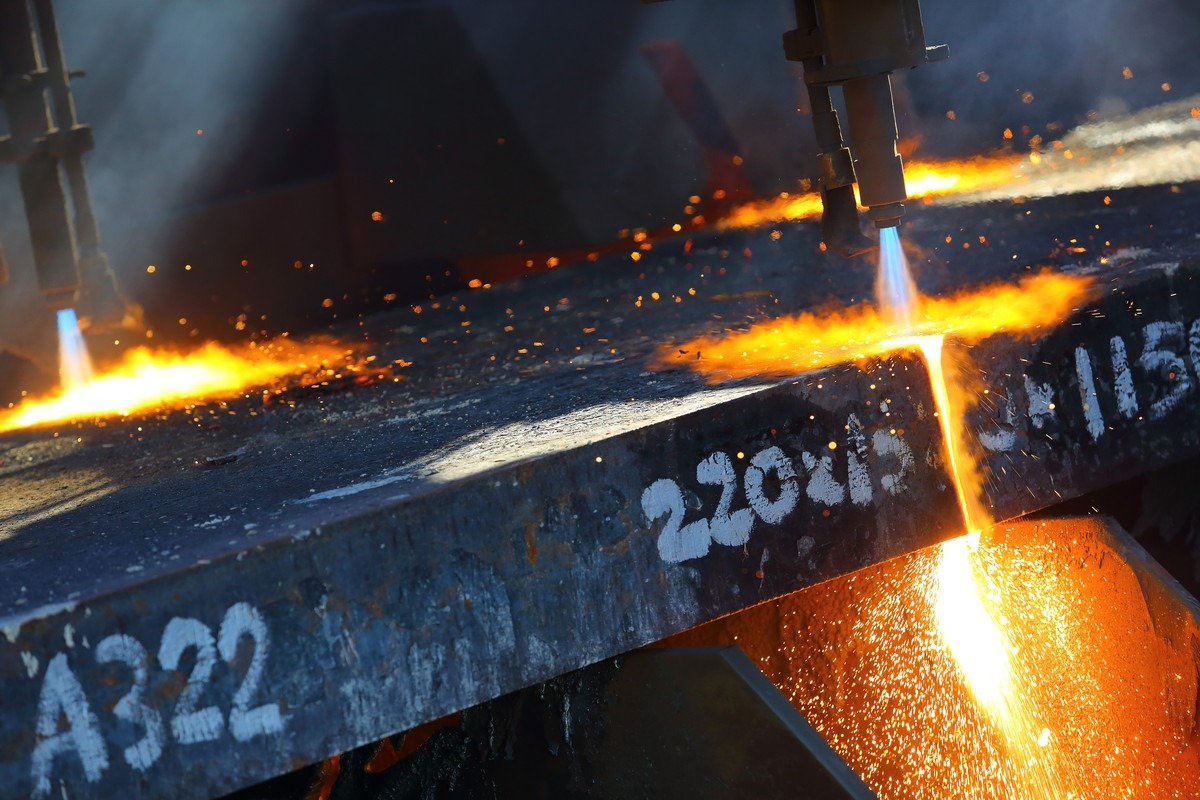
ПЛОСКИЙ ПРОКАТ
Чи бачили ви, як готують коржі для «Наполеону»? Якщо так, тоді вам буде легше зрозуміти, як відбувається прокатка металу. Після того, як ми отримали зливки зі сталі, їх необхідно перетворити на готовий продукт.
Найпоширеніший спосіб деформації металу – це прокатка. Вона виконується за допомогою спеціального стану. Як тісто розкачують качалкою, так і метал пропускають між обертовими валками. Куховарство – добре, але в металургії усе набагато цікавіше!
1 000 000 деталей конструктора LEGO – приблизно стільки містить один сляб, напівфабрикат для виробництва сталевих плит, листів і рулонів. Середня вага – 20-30 тонн
Тут не обмежуються одним видом «качалки». Прокатні стани бувають заготівельні, листові та штабові. Коли сталева заготівка проходить між обертовими валками, її товщина зменшується, а довжина зростає. Залежно від взаємного розташування валків і заготівки прокатку поділяють на поздовжню, поперечну та поперечно-гвинтову.
Найбільше прокату виробляється поздовжнім способом. Так отримують листи, рулони і сортовий прокат. Плоский прокат буває товстолистовим (понад 4 мм) і тонколистовим (до 4 мм).
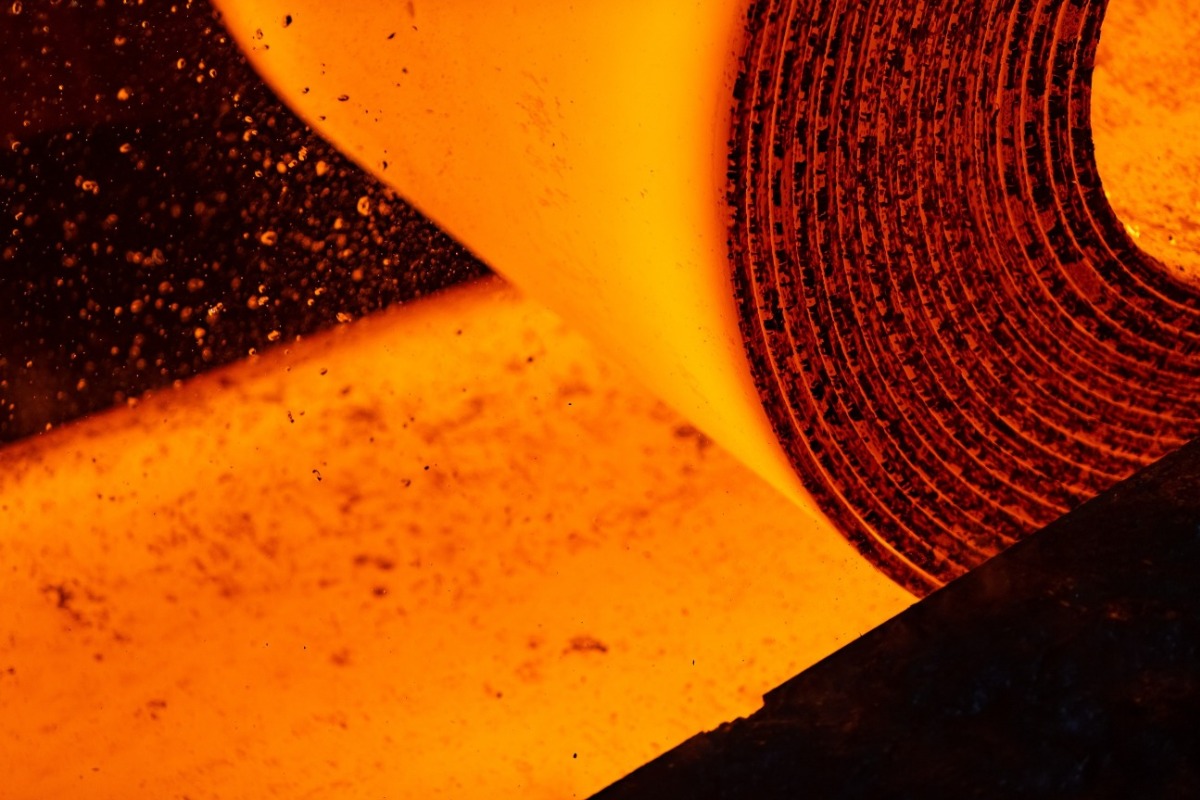
Формування рулону, стан гарячої прокатки на Запоріжсталі
Для приготування пиріжків тісто розкачують теплим, а для пісочного печива – охолодженим. Так і на наших станах є гаряча і холодна прокатки.
Для виробництва товстого листа сталева заготівка (сляб) прямує на стан після машини безперервного лиття. Потім зливок розжарюють у нагрівальній печі та прокатують декілька разів в обох напрямках до потрібної товщини. Метал ріжуть на листи необхідної довжини і доводять до ладу: проводять термічну обробку, очищають від окалини тощо. І ось лист готовий до вживання. На нього чекають суднобудівники, машинобудівники, виробники труб великого діаметра та інші споживачі.
Окрім листів із слябів роблять рулони. Починають так само: сляб нагрівають до температури 1200 ˚С, прокатують, потім очищають від окалини напором води і прокатують ще раз. Метал охолоджують водою чи повітрям і скручують у рулон моталкою. Така сталь застосовується у будівництві, машинобудуванні, виробництві труб або потрапляє на холодну прокатку. Чому холодну? Річ у тому, що за певної товщини гаряча прокатка перестає бути ефективною. Метал швидко остигає, зростає опір деформації, а через часте підігрівання на поверхні утворюється ще більше окалини. Тому тонші за 1,5 мм листи отримують за допомогою холодної прокатки. Вона дозволяє точніше вирахувати товщину остаточного продукту, покращує якість поверхні та механічні властивості прокату.
Перш ніж потрапити на холодну прокатку, гарячекатаний метал проходить травлення. Поверхню прокату обробляють розчином сірчаної або соляної кислоти. Частина окалини розчиняється, частина відшаровується. Метал промивають у чистій воді, а залишки кислоти нейтралізують у лужній ванні. Потім змащують спеціальними маслами чи емульсіями і прокатують. Після того, як прокат досягає потрібної товщини, його термічно обробляють або оцинковують.
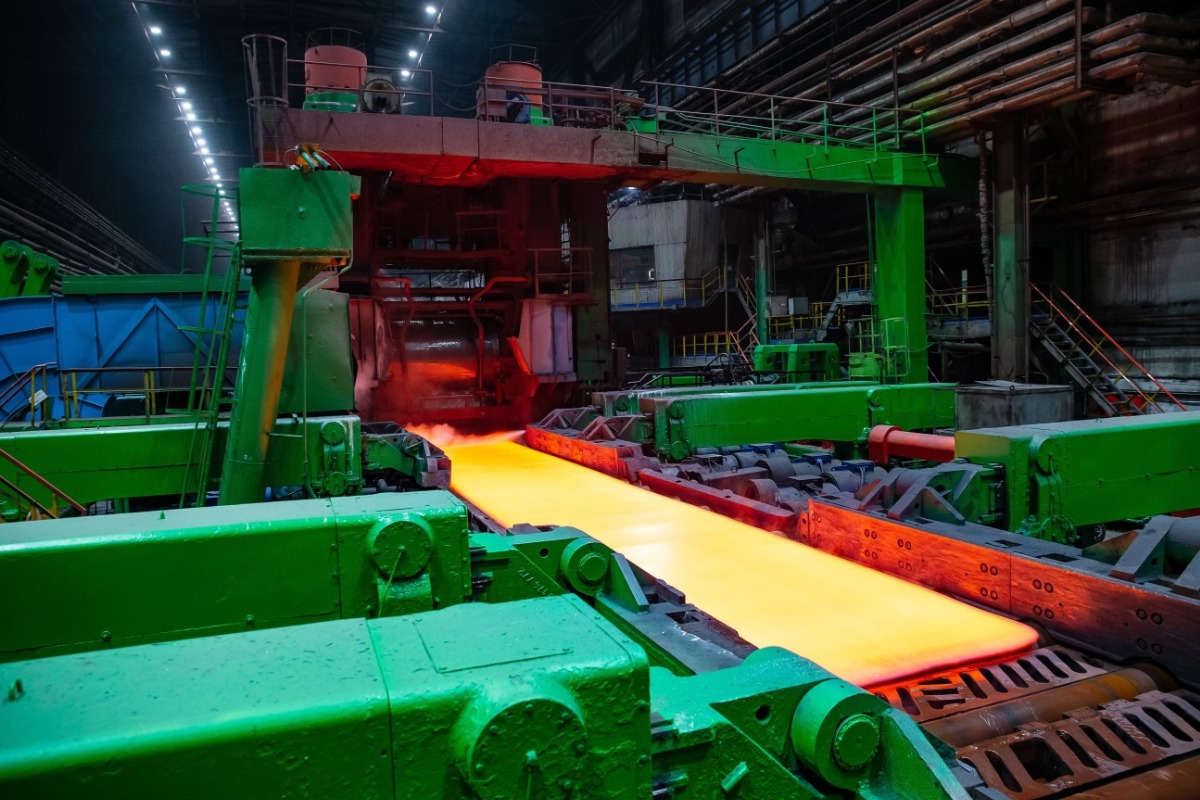
Прокатка сталі на МКІІ
Для зняття наклепу сталь проходить відпалювання. Уявіть, що з хліба знімають скоринку, щоб увесь м’якуш зробити однаково твердим. Відпалювання – це вид термічної обробки, коли метал нагрівається до певної температури, витримується так деякий час і поступово остигає. Під час відпалювання метал «відпочиває», знижується його твердість, а мікроструктура стає однорідною. Після цього прокат остаточно обробляють або дресирують — це холодна прокатка з невеликим обтисканням без змащення. Дресирування покращує якість поверхні сталі. Іноді продукцію відправляють замовникам без відпалювання, в наклепаному стані.
Менше 0,1% маси продукції, що випускають заводи Метінвесту за добу, зможе вивести на орбіту найпотужніша ракета – носій у світі Falcon Heavy Ілона Маска
Завершальна стадія – обробка. У листів або рулонів обрізають кромки, розрізають по довжині, наносять захисні покриття. Щоб зробити прокат стійким до механічних пошкоджень і вберегти від корозії, його покривають цинком, оловом або алюмінієм. Найбільш економічним способом вважається гаряче оцинкування. Для цього прокат проходить через ванну з розплавленим цинком. Оцинковані вироби можуть не іржавіти до 30 років.
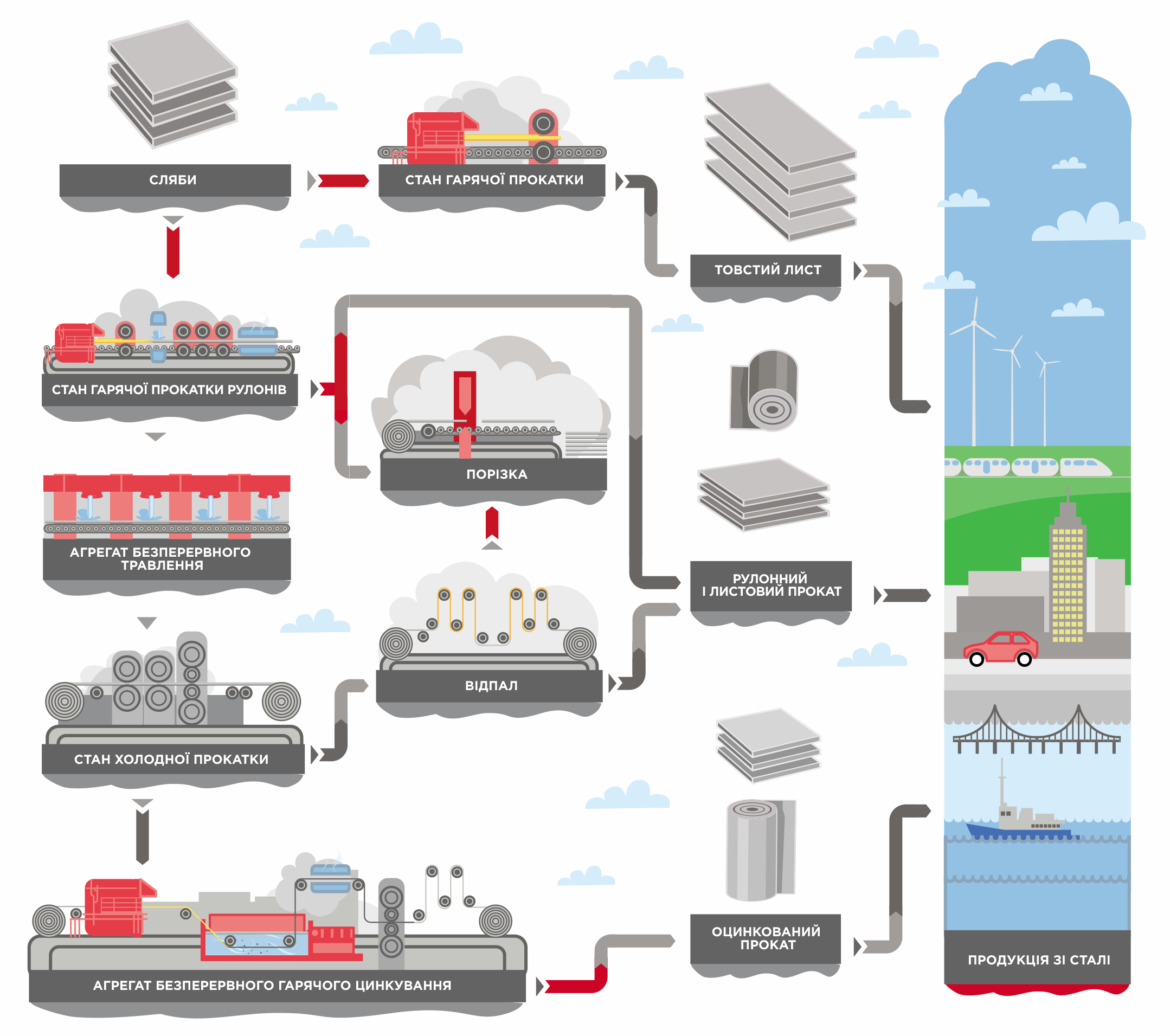
Холоднокатаний рулонний прокат затребуваний у будівництві, також з нього роблять деталі для автомобілів і побутової техніки.
Плоский прокат – листи, рулони, штаби, плити – кінцева продукція лише для металургів. Інші виробники не використовують прокат у своєму первісному вигляді. Його обов’язково переробляють. Сьогодні це рулон сталі, а завтра – дах будинку, кузов машини чи корпус холодильника.
Для споживачів, яким потрібна продукція певної форми, у металургів є окреме меню – сортовий прокат. Щоб розібратися, що це таке, згадаємо улюблену страву дитинства – макарони. Чим химерніші вони, то цікавіше їсти: бантики, зірочки, метелики. Далі ми поговоримо про геометрію тіста і великі форми.
СОРТОВИЙ ПРОКАТ
Один із основних видів продукції прокатного виробництва – сортовий прокат. Це різні профілі – не порожнисті, а суцільні всередині. Вони бувають великого, середнього і дрібного розміру. Профілі поділяються на прості (круг, квадрат, штаба), фасонні (рейки, швелери, кутики, балки) і спеціальні (колеса, кулі).
Усе це розмаїття катається із блюмів чи квадратної заготівки. Пам’ятаєте напівфабрикати із глави про виробництво сталі? Щоб уявити, що таке блюми, відріжемо від «Наполеону» довгу смугу. Блюм – це сталева заготівка квадратного чи прямокутного перетину зі стороною від 140 до 500 мм. Нагадує паралелепіпед. Маса одного блюма може досягати 25 тонн.
Залізниця Земля – Місяць Довжини рейок, вироблених на «Азовсталі», вистачило б для будівництва залізничної лінії до Місяця
Блюм отримують із зливків прокаткою на спеціальному стані або з рідкого металу, що розливається на машині безперервного лиття заготівок. Блюмінг – це стан із двома, рідше – трьома валками. Зливок металу відправляють залізничними платформами до нагрівальних колодязів обтискного цеху. Там сталь нагрівають до 1100–1300 ˚С і на зливковозі доставляють до роликового конвеєра блюмінга. Зливки прокатують у декілька підходів до потрібних розмірів, а потім обрізають передній і задній кінці розкату. Тепер напівфабрикат готовий перетворитися на балки, швелери, рейки та інші форми. На що саме – залежить від того, на який стан потрапить.
Що вам нагадують рейки? Локшину? А, може, спагеті? До повномасштабного вторгення єдиним виробником магістральних рейок в Україні бyв комбінат «Азовсталь». Лише уявіть: за час роботи маріупольський гігант випустив стільки рейок, що ними можна оперезати Землю по екватору 16 разів!
Швидкість скорочує відстані. А рейки – обов’язкова деталь у швидкісній історії поїздів. Після обтискного стану напівфабрикати потрапляють на ділянку нагрівання металу рейкобалкового цеху, де їх знову нагрівають, але вже в печі прокатного цеху.
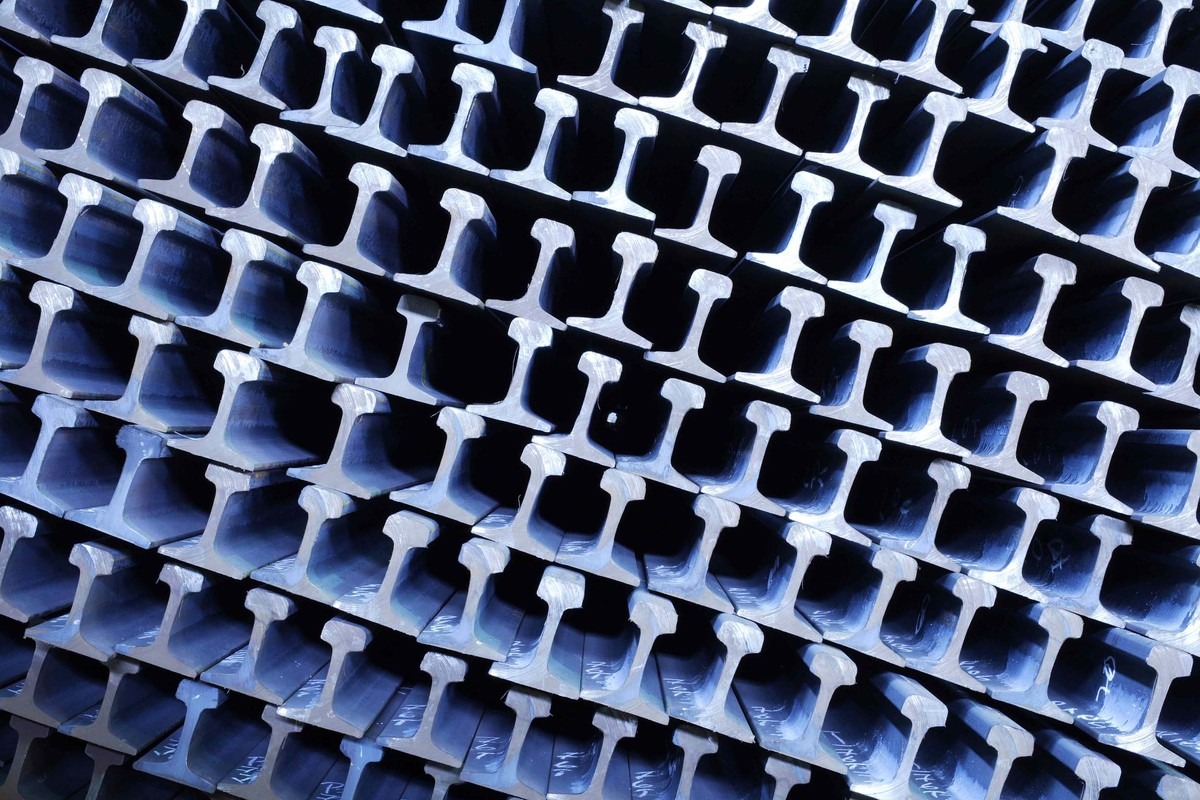
Потім заготівку послідовно обтискають у кількох калібрах, вирізаних у двох валках, що обертаються в різні боки. Під час прокатки рейок блюм подовжується майже удесятеро – з одного блюма виходить дві рейки довжиною по 25 м кожна – такими рейками їздять поїзди в Україні.
Після прокатки рейки та профілі розрізають на потрібні відтинки, таврують, охолоджують на холодильниках і направляють на остаточну обробку та приймання. Наприклад, рейки після прокатки й охолодження правлять на вальцевоправильній машині, перевіряють ультразвуком. Після загартування поверхні та правки на кінцях кожної рейки просвердлюють отвори, щоб згодом з’єднати їх між собою в єдину нитку. Потім рейки їдуть на інспекторські стелажі для огляду і сортування, а звідти – на склад.
Блюм – доволі універсальний напівфабрикат. Крім рейок і спеціальних профілів, із блюмів можна виготовити великогабаритні балки, швелери, кутики й іншу сортову продукцію. Це як гігантські «черепашки» чи «ріжки» з тіста. Технологія виробництва прокату на крупносортних станах подібна до рейкобалкової. Блюм нагрівають у печах і прокатують у декілька етапів. Заготівку послідовно обтискають у кількох калібрах, вирізаних у валках. Після прокатки в останньому калібрі виходить форма готового виробу.
Прокат залишилося транспортувати до пилок гарячого різання, порізати на довжини від 4 000 до 24 000 мм, охолодити та виправити на спеціальних машинах і у разі потреби знову порізати. Цього разу пилками холодного різання на довжини, потрібні замовнику. Потім готову продукцію упаковують, зважують і складають.
І на десерт – рейкові скріплення і помольні кулі. Ті самі рейки, про які йшлося раніше, не можуть існувати самі по собі. Як торт не можна уявити без крему, так і рейки – без скріплень. Це накладки і підкладки. Фігурні підкладки використовуються для надійного з’єднання рейок зі шпалами. А накладки з отворами для болтів з’єднують окремі рейки в довгу залізничну гілку, щоб ми могли подорожувати куди завгодно.
Отже, беремо штаби для накладок, які виробляють у крупносортному цеху. Рубаємо їх на заготівки. Нагріваємо заготівки в печі, пробиваємо отвори, правимо і маркуємо, потім швидко охолоджуємо в маслі та воді й «подаємо до столу» на сортування.
А тепер сервіруємо стіл фруктами: мандаринами, апельсинами, грейпфрутами. Як ви вже здогадалися, мова піде про помольні кулі. Вони бувають різного діаметра – від 40 до 120 мм. Їх використовують для помолу руд кольорових і чорних металів на гірничо-збагачувальних комбінатах, а також у цементній і вугільній промисловості. Тобто, якщо потрібно змолоти щось тверде, кульові млини впораються якнайкраще.
Агрегат, на якому прокатують помольні кулі, так і називається – кулепрокатний стан. Круглі заготівки нагрівають у печах і пропускають через два валки з кільцевими канавками. Валки розташовані під кутом до осі обертання і крутяться в один бік — так із суцільної заготівки між канавками формуються кулі. Тієї миті вони нагадують новорічну гірлянду. Потім їх охолоджують у воді, загартовують і скидають у бункер, щоб повністю остудити готову продукцію.
Наша екскурсія кухнею металурга добігає кінця. Ми разом пройшли весь виробничий шлях – від кар’єру до прокатного цеху. Дізналися, як шматок руди перетворюється на вічний продукт – сталь, і що з неї роблять.
Виробництво – процес захопливий. Спостерігати, як із окремих елементів народжується щось абсолютно нове – неймовірно цікаво. Запрошуємо вас на справжню екскурсію на металургійні комбінати Метінвесту. Там ви на власні очі побачите салют із чавуну, гарячі сляби та розжарену сталь... І жоден яскравий момент не залишиться поза вашою увагою.
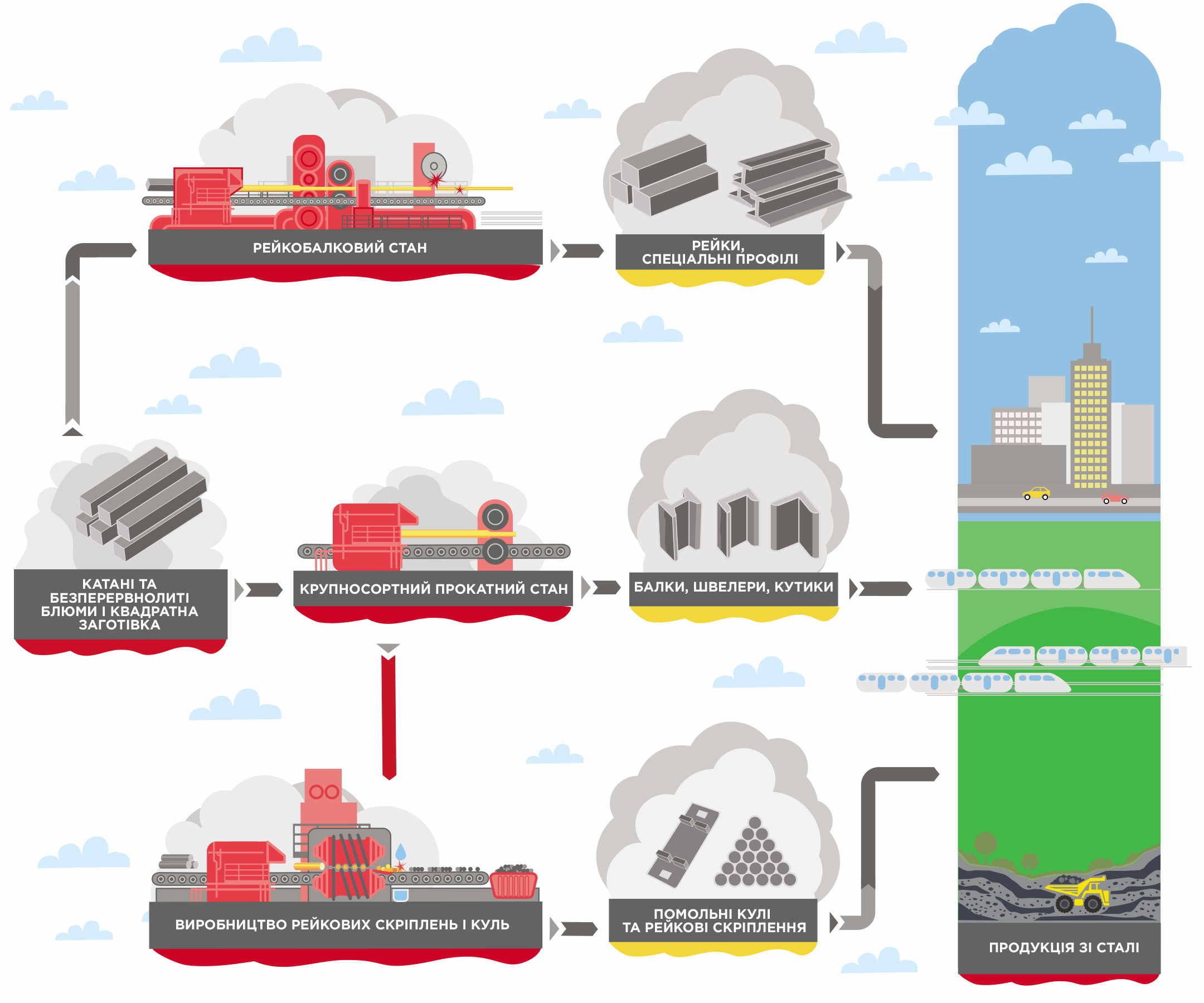

Немов у школяра, який отримав атестат зрілості, за брамою металургійного заводу доросле життя у сталі лише починається.
Коли сталь стає виробом, перед ним відкриваються два шляхи: одразу влитися в роботу, тобто стати частиною будівлі, конструкції, механізму чи приладу, або ж пройти апгрейд і вже потім посісти гідне місце.
ЗІ СТАЛІ – В ДЕТАЛІ
Металургійні заводи випускають величезну кількість різноманітних сталевих елементів: товсті і тонкі листи, арматуру, кругляк, квадрат, рейки, труби, двотаври, швелери, кутики. Усіх і не перелічиш.
Сучасні архітектори не обмежуються стандартним заводським набором металопродукції і можуть створювати конструкції будьякої складності. Виготовити або зібрати необхідну деталь їм допомагають інші заводи — з виробництва металоконструкцій.
Завод металоконструкцій нагадує кондитерську майстерню,
оснащену професійним обладнанням. Для кожної фігурки там є
своя насадка. Тільки замість тіста беруть сталевий лист. Спочатку
роблять заготівки: довгі металеві профілі рубають на гільйотинних
ножицях, а листи розрізають тонким лазером або потоком плазми. Невеликі елементи ділять на деталі високоміцними пилами.
На заготівках вирізають або висвердлюють усі необхідні отвори,
скоси, підрізають і обточують кромки, обробляють поверхню. За
допомогою потужного преса заготівкам надають необхідної форми, роблять загини, виступи. Коли всі деталі готові, можна збирати
конструкцію. Для цього використовують спеціальні кондуктори —
пристрої, що допомагають з’єднувати деталі.
Заводи теж не оминув усесвітній технічний апгрейд. Нові технології дозволяють друкувати конструкції, як це роблять 3D принтери. Готові конструкції відправляють на місце будівництва. Зазвичай їх розділяють на частини і збирають одразу на майданчику. Якщо ж конструкція величезна і її не можна розділити, то транспортування перетворюється на справжнє видовище. До справи беруться багатоколісні платформи, їх супроводжує поліція, а все, що заважає на шляху, тимчасово прибирають.
ЗРОБЛЕНО ЗІ СТАЛІ
Багатоповерхівка, в якій ви мешкаєте, сімейний автомобіль, міст дорогою додому, вітряки та вежі ліній електропередач у полях, корабель на морському горизонті – сталь скрізь. Без неї не можуть обійтися різні сфери промисловості: будівництво, суднобудування, транспорт, гірничо-металургійний комплекс, енергетика і машинобудування. Ось лише декілька прикладів грандіозних споруд, в яких є сталь Метінвесту.
Хмарочос The Shard
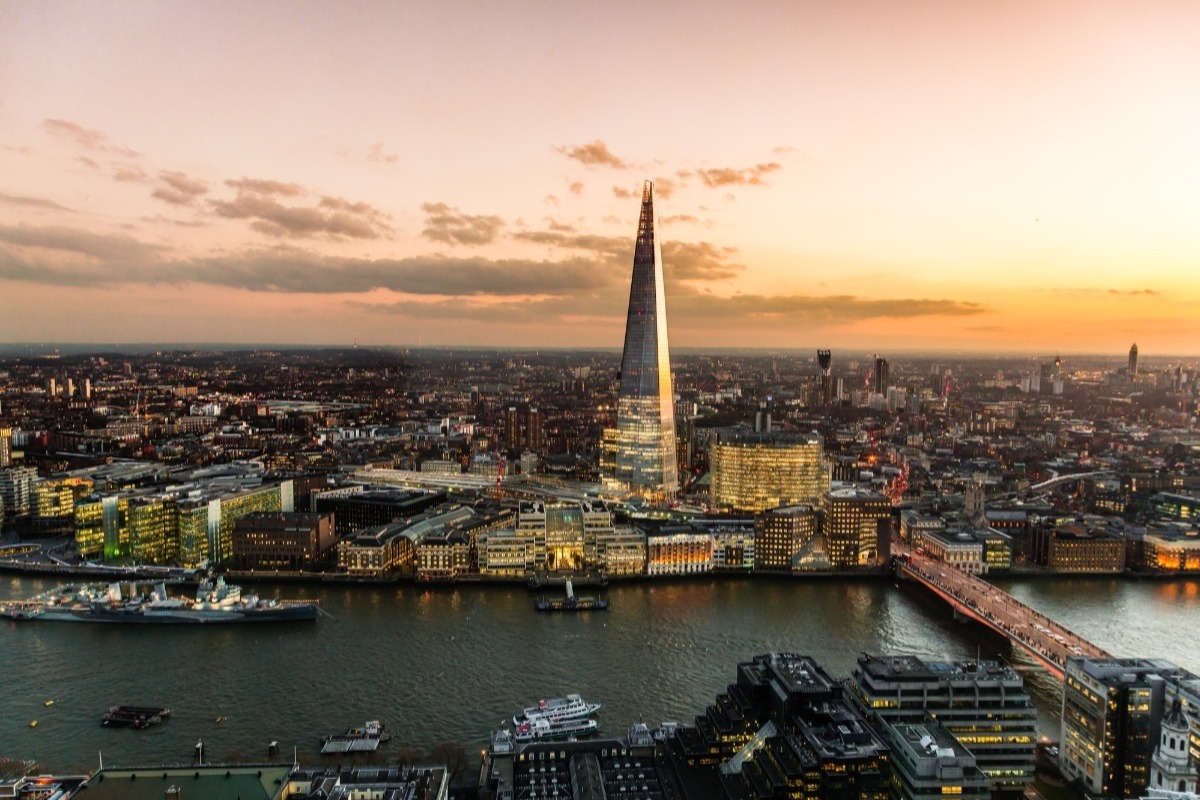
Shard на заході сонця
Найвища будівля в Лондоні та п’ятий за висотою хмарочос у Європі. Побудований у 2009−2012 роках. Піраміда, облицьована скляними панелями, випросталася в небо на 310 метрів. Рвані лінії шпиля вежі нагадують уламок скла. Саме так і називається хмарочос. На 87 поверхах «вертикального міста» площею 127,4 тис. кв. м розташовані офіси, квартири, ресторани і п’ятизірковий готель. Три верхніх оглядових майданчики із 360-градусним оглядом дуже популярні серед туристів. Раніше на такій висоті поглянути на місто можна було лише з борту гвинтокрила.
НСК «Олімпійський»
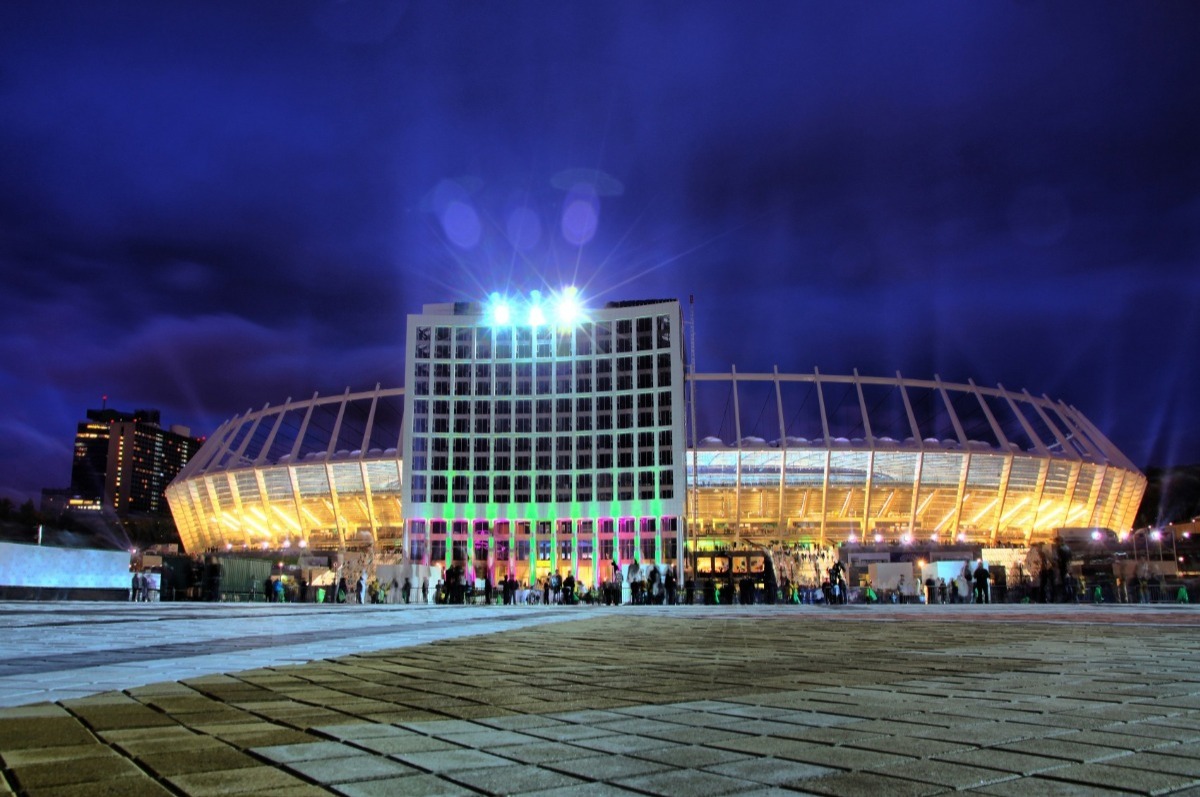
Одна з найкращих спортивних арен Східної Європи
Національний спорткомплекс «Олімпійський» у Києві реконструювали перед проведенням футбольного чемпіонату «Євро-2012». Стадіону − 95 років, за цей час він пережив чотири реконструкції. Місткість арени – понад 70 тисяч глядацьких місць, загальна площа – 145 тис. кв. м. Це найбільший стадіон в Україні й один із найбільших у Європі. Тут відбуваються головні футбольні матчі та концерти зірок світового масштабу.
Круїзний лайнер Carnival Vista
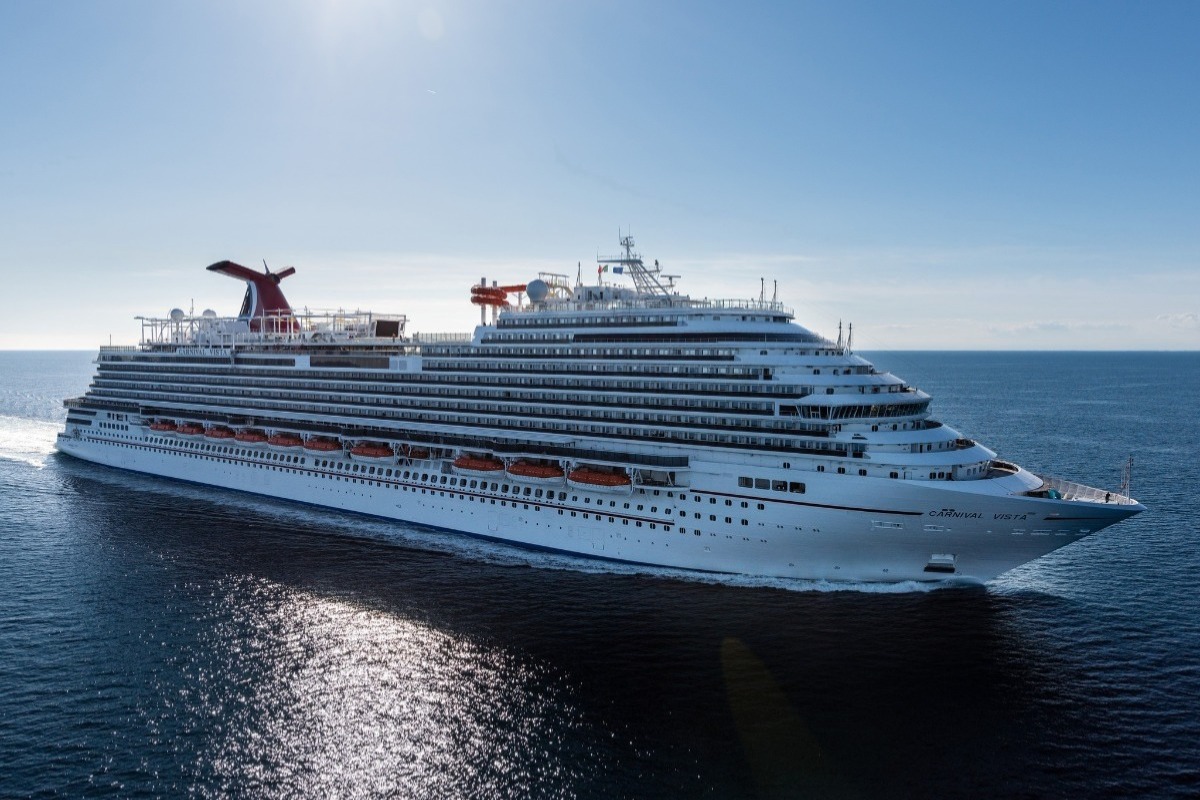
По морях, по океанах
Сучасний круїзний лайнер Carnival Vista спустили на воду у 2016 році. Судно на 15 палуб, довжиною 322 метри, може прийняти на борт майже 4 тисячі пасажирів. Лайнер курсує вздовж берегів Європи й у Карибському морі. На кораблі можна пограти у футбол, баскетбол, волейбол, міні-гольф, боулінг, відвідати мотузковий парк, IMAX-кінотеатр.
Сонячна електростанція на Львівщині
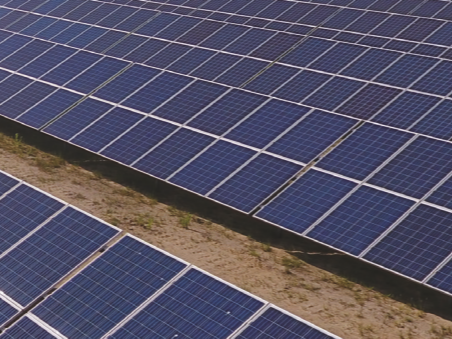
Сонячна електростанція потужністю 72 МВт
Поблизу села Терновиця на Львівщині на місці колишнього хімічного заводу будують сонячну електростанцію потужністю 72 МВт. Цього вистачить, щоб забезпечити електроенергією близько 8 тисяч квартир з електроплитами чи понад 500 сучасних тролейбусів. Першу чергу станції вже відкрили – на площі 12 га розмістилися понад 20 тисяч сонячних панелей.
European Extremely Large Telescope
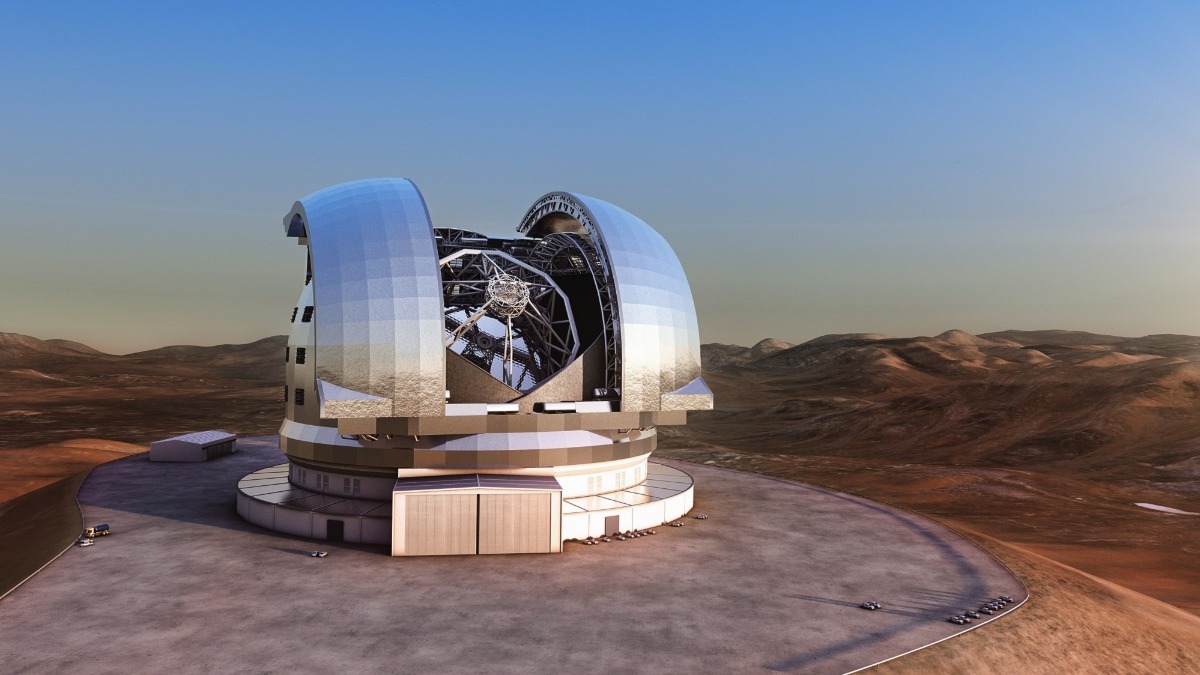
Найбільше око людства, що дивиться в небо
Європейський величезний телескоп або «найбільше око людства, що дивиться в небо». Найбільший у світі телескоп для дослідження планет за межами Сонячної системи, чорних дір і темної енергії Всесвіту побудують до 2024 року в чилійській високогірній пустелі Атакама. Йому належить дізнатися, чи є життя на інших землеподібних планетах. Головний інструмент обсерваторії – адаптивна оптична система із п’яти дзеркал. Діаметр найбільшого дзеркала – 39 метрів, воно складатиметься із майже 800 шестикутних дзеркал діаметром 1,4 метра. Це дзеркало зможе збирати в 13 разів більше світла, ніж інші телескопи, щоб отримати детальніше зображення. Обертальний купол телескопа матиме розмір футбольного поля (86 метрів у діаметрі). Загальна маса конструкції становитиме п’ять тисяч тонн, із них три тисячі – рухома частина. Фінансує будівництво Європейська південна обсерваторія (ESO) – міжнародна дослідницька організація, до якої входить 16 країн.